Boron Magnets Prize for Pioneer
Dr. Masato Sagawa, President of NDFEB Corporation in Kyoto, Japan, has been awarded the 2022 Queen Elizabeth Prize for Engineering for innovative work on Boron magnets prize. He invented the neodymium-iron-borate magnet, which is at the heart of green energy and carbon reduction efforts, powering wind turbines and other renewable systems.
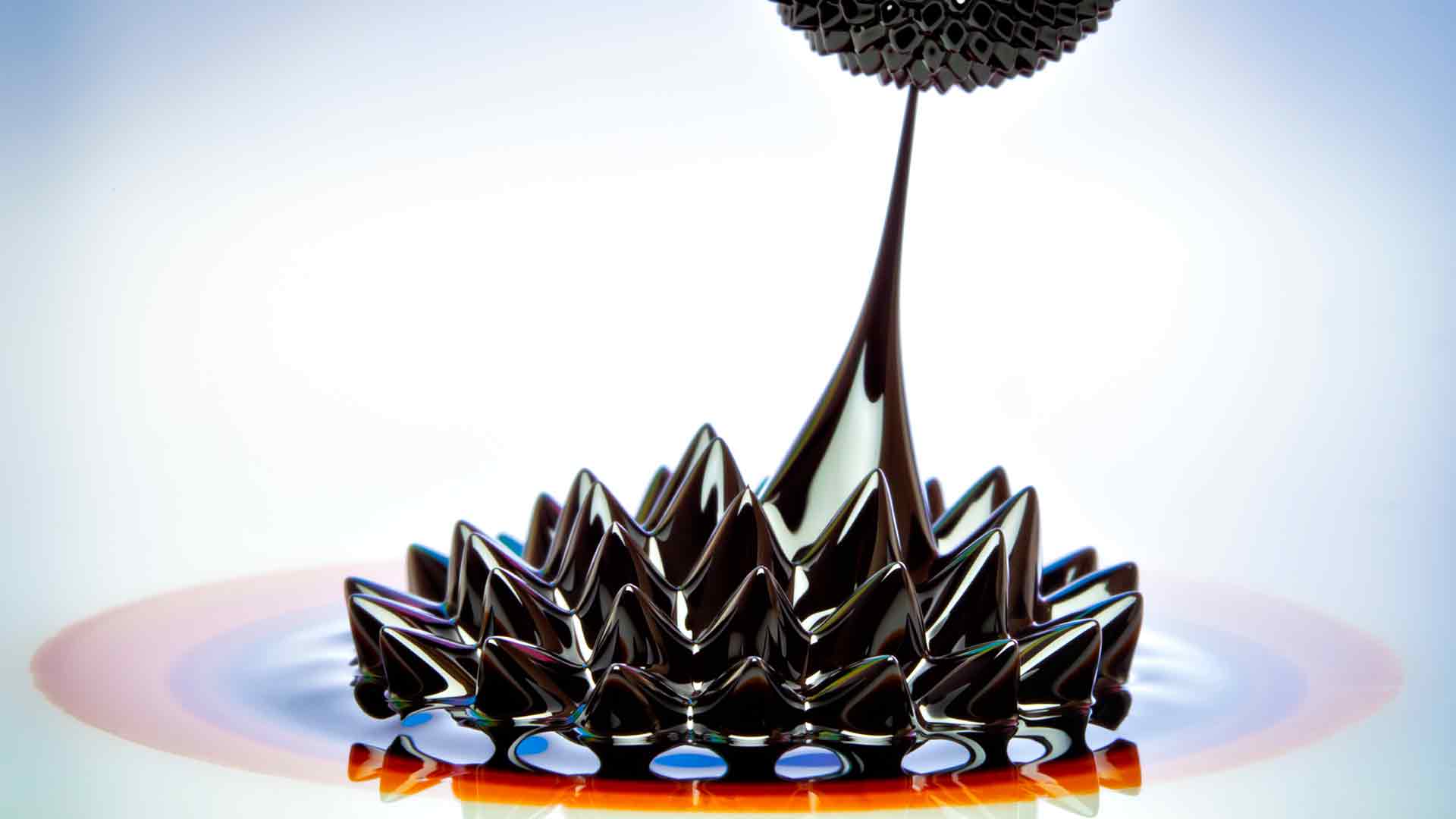
Boron Magnets Prize
Dr. Masato Sagawa has been awarded the 2022 Queen Elizabeth Prize for Engineering for his invention of the neodymium-iron-boron magnet (Nd-Fe-B), the strongest commercial magnet available. It is found in multiple commercial applications to direct clean energy efficiently. It is at the heart of green energy and carbon reduction efforts, powering wind turbines and other renewable systems.
NdFeB Magnet Technology
A neodymium magnet or NdFeB, or Neo magnet, is the most widely used rare-earth magnet. It is constructed from neodymium, iron, and boron alloy to form the Nd2Fe14B crystalline structure. Magnetic properties of neodymium magnets depend on the alloy composition, microstructure, and manufacturing technique employed.
The magnet was first developed independently in 1984 by General Motors and Sumitomo Special Metals, forming the basis for commercialization as the most vital type of neodymium magnet available today
Neodymium is a magnetic metal with antiferromagnetic properties. Its magnetic properties appear at low temperatures below 19 K (−425.5 °F) in its purest form. However, some neodymium compounds with ‘transition metals,’ i.e., iron and ferromagnetic, have Curie temperatures well above room temperature. These compounds are used to make neodymium magnets.
Strength
Several factors give these magnets their strength. The Tetragonal Nd2Fe14B crystal structure has a high ratio of magnetic force versus magnetic moment. This means a material crystal preferentially magnetizes along a specific crystal axis while not easily magnetize in other directions.
The neodymium magnet alloy microcrystalline grains are aligned in a strong magnetic field at manufacturing. Their magnetic axes all point in the same direction. The resistance of the crystal lattice to a change in direction provides strong resistance to demagnetization.
The neodymium atom has four unpaired electrons in its electron structure compared to 3 in iron. The unpaired electrons in a magnet need to be aligned so that their spin is in the same direction, thereby generating a magnetic field. Magnetic energy is about 18 times greater than “ordinary” ferrite magnets by volume and 12 times by mass.
Structure
The Nd2Fe14B crystal structure has alternating layers of iron atoms and a neodymium-boron compound. The boron atoms are not directly responsible for magnetism. Instead, they improve cohesion by strong covalent bonding.
Applications
Nd-Fe-B technology has been crucial for the advancement of the personal computer industry and the automotive sector. The development of lightweight hard disk drives depended on the power of magnetic fields that could be delivered within a compact volume. Nd-Fe-B magnets move the read-write heads traversing the disk. Nd-Fe-B magnets power many common everyday items – from mobile phones and electric power tools to jewelry clasps and door latches.
Neodymium Boron magnets are popular for precision actuators, sensors, and hobbyists. Magnetic demagnetization is resistant to this metal, which is extremely strong. Their performance is unaffected by extremely high temperatures.
The use of these metals for high-technology applications has increased significantly over the past few years. Electronic components have been miniaturized due to the development of high-energy products. It has been made an indispensable part of daily life by developing massive hard drives, lightweight headsets, and anti-lock braking systems.
Manufacturing
Because of different manufacturing processes, the magnets are divided into two subcategories, namely sintered NdFeB magnets and bonded NdFeB magnets. They have replaced other types of magnets in many applications in modern products that require strong permanent magnets, such as electric motors in cordless tools, hard disk drives, and magnetic fasteners.
A neodymium-iron-boron magnet is manufactured using the orient print press [ OPS] process. An alloy composed of neodymium, iron, and boron is ground into a submicron powder using a ball mill. Neodymium, iron, or boron-iron alloys are aligned and pressed into basic blocks in a strong magnetic field. As a result, the material is melted into a solid.
Furthermore, boron is also part of the manufacturing process of these magnets, along with neodymium and iron. These alloys are often known as NdFeB and are highly effective. They are capable of lifting thousands of times their weight. By the middle of this decade, the market for Nd-Fe-B magnets is expected to be worth approximately $20 billion.
Neodymium magnets are capable of withstanding extremely high levels of electrical current. The component can withstand high-frequency movements of up to one million volts.
Biography of Dr. Sagawa
Masato Sagawa was born in Tokushima, Japan, on August 3, 1943. The inventor of sintered permanent magnet NdFeB, is a Japanese scientist and entrepreneur. As a result of his invention of and development of the highest performing sintered Nd-Fe-B type permanent magnets and contribution to energy conservation, Hagawa was awarded the Japan Prize in 2012.
The innovation was initially developed by Sagawa at Fujitsu Laboratories during his time there between 192-1982 before he went on to further develop the research at Sumitomo Special Metals in 1982.
In 1988, Sagawa founded Intermetallics, an R&D facility where he continued to work on neodymium magnets. In 2012, he founded NDFEB Corporation 2012, where he is the president.
In addition to receiving the 2022 Queen Elizabeth Prize for Engineering, he received the Japan Prize in 2012; Dr. Sagawa is also a co-recipient of the IEEE Medal for Environmental and Safety Technologies to develop rare earth-iron-boron permanent magnets for use in high-efficiency motors, generators, and other devices.
In an interview with BBC News in early 2022, Sagawa stated, “This is the biggest award I have ever received.” He had previously received the Japan Prize, a significant award; however, it is substantial due to its international reach.
It was during the early 1980s that Dr. Sagawa made his breakthrough. The strongest permanent magnet was a combination of samarium and cobalt (Sm-Co). Cobalt is a rare metal, and the scientist was aware that if a solution could be found based on iron, that would provide a much cheaper and more helpful product than cobalt.
To achieve this, he combined iron with neodymium, which is the third most abundant rare-earth element. Rare-earth elements are found in the Earth’s crust and are used for different purposes. Adding boron to the mix increases the Curie temperature – the point at which magnetic properties are lost.
Magnetic materials are used primarily in the manufacture of vehicles. There are many instances where a magnet is used either as an integral part of the motor or to initiate an electric current – from the pump that applies screen wash to the windscreen to the sensor that activates the anti-lock braking system.
A tribute to Dr. Sagawa would not be complete without the mention of Dr. John Croat. When collaborating with General Motors, the Americans reached the same material solution independently at the same time. Meanwhile, the IEEE 2022 Environmental and Safety Technologies Medal has been jointly awarded to Sagawa and Croat. According to the Queen Elizabeth Prize chairman, Lord Browne of Madingley said, judges, perceived Sagawa’s manufacturing process gave him the edge over Dr. Croat.
In addition, the powdered method used by Sagawa is more expensive than the melting and bonding process used by the Americans and does not have the same versatility of application. However, the resultant magnet is a significantly more powerful unit.
A great idea can look great on paper, but to achieve success, one must demonstrate the ability to manufacture it on a large scale and at a price that people will accept, according to Lord Browne. Sagawa has demonstrated that engineering is about delivering. While scientists come up with great ideas, such as the Higgs Boson, engineering has to deliver. Sagawa’s innovation achieved this very successfully.
Dyprosium (Dy), an essential element that increases magnets’ resistance to heat, is highly scarce. This 78-year-old scientist continues to improve his technology. He is now attempting to reduce the amount of another rare-earth element that is used in trace amounts. Dr. Sagawa said that the goal is to minimize dysprosium’s use to less than 1% of the composition and preferably not use it.
Moreover, the above latest research will lead to neodymium magnets will be used even more widely on the market, particularly in electric vehicles.
The Queen Elizabeth Prize for Engineering
The Queen Elizabeth Prize has traditionally been awarded every other year. However, it has now become an annual event. The recipient of the prize receives a check for £500,000, as well as a trophy that the Queen or her representative presents. The Queen Elizabeth Prize for Engineering is expected to raise our awareness and appreciation of Dr. Sagawa’s accomplishments.