Boron in Sports Equipment
Boron as boron fiber and boron steel has excellent tensile strength. Boron is used in sports equipment like golf clubs, fishing rods, tennis rackets, and bicycle frames. It renders them the required power, flexibility, lightness, and durability, thus, contributing to better performance. The sports goods company, Mizuno, has emerged as a leading manufacturer of sports equipment composed of boron.
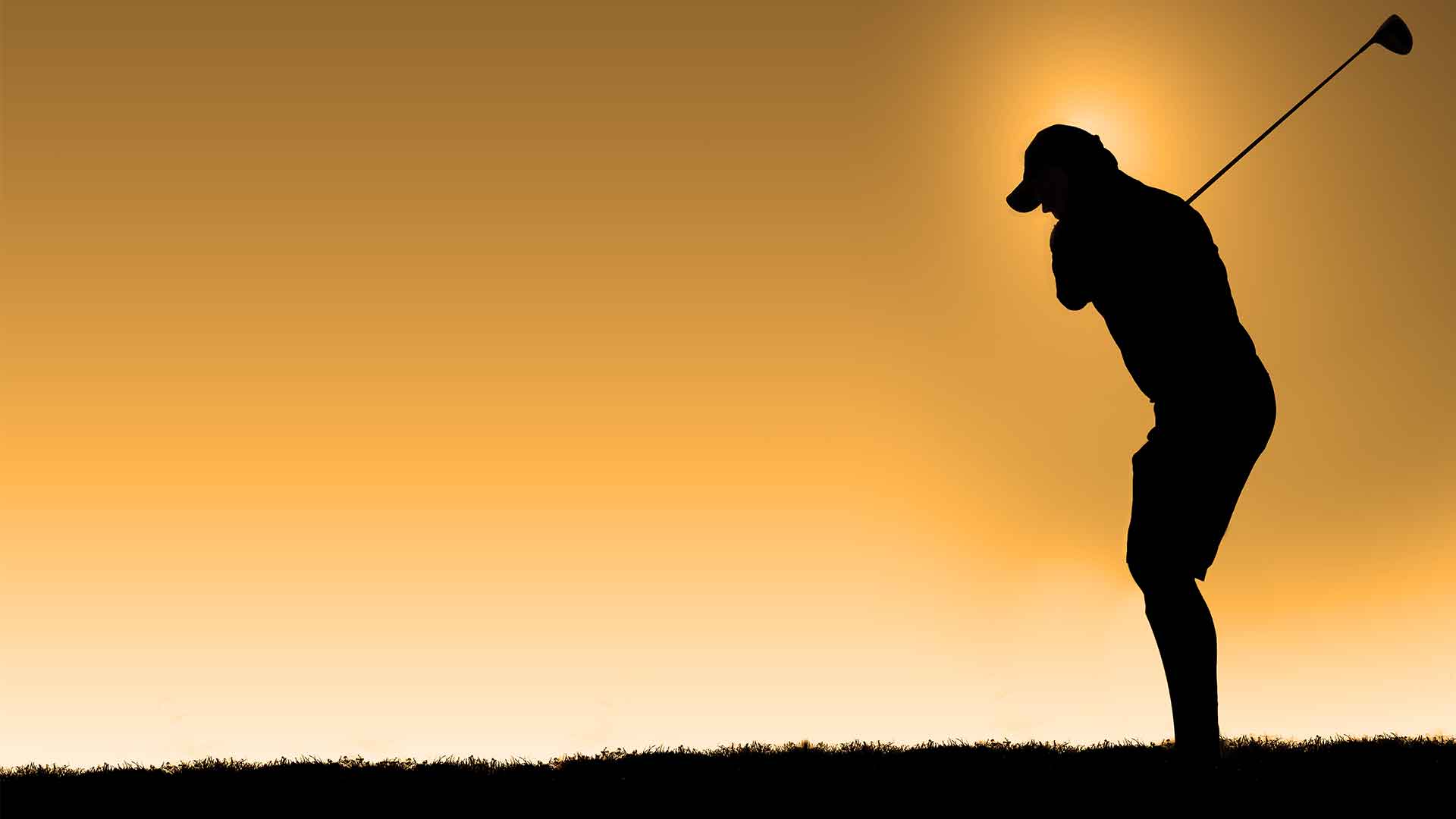
Boron in Sports Goods
Boron Fiber
Boron fiber is the boron compound mainly used in applications for sporting goods. It is commonly known as boron filament, an amorphous element of B5 by-product, representing a primary industrial usage of elemental (free) boron. Boron fibers were created to increase stiffness in composite materials.
These fibers were initially developed when glass fibers were used mainly to reinforce composites. Boron fibers can be made by chemical vapor deposition of boron onto approximately 12 mm tungsten or carbon wire (core). Boron fibers are 100-200mm in diameter. Boron fibers will deteriorate when they contact aluminum or titanium matrixes at temperatures above 500°C. Thus, chemical vapor deposition is used for covering the fiber surface with a layer of silicon carbide, SiC.
Boron fibers have high compressive and tensile strength and are incredibly stiff. Boron fibers have a tensile strength between 3-4 GPa, and Young’s modulus ranges from 380 to 400 GPa. An epoxy matrix often accompanies the boron fiber.
Boron fibers are so strong that they can repair cracked aircraft skins. Because of its close thermal expansion to aluminum and the absence of galvanic corrosion potential, boron fibers are ideal for this purpose.
Boron Fiber as a Strong Material for Sports
Boron fibers are lightweight, high-strength materials mainly used in advanced aerospace designs as composite materials. Boron fibers have commercial applications too. They are use strength and flexibility for fishing rods, (tennis) racquets, and golf clubs – for rigid golf shafts and tennis rackets.
Fishing Rods
Another early use of boron was a fishing rod made with boron fiber. The rod’s “feel” for anglers earned it a cult status. In 1971, Don Phillips created the first fly fishing rod made from boron. The boron/graphite hybrid rod was designed later. In 1974, boron rods were manufactured and were introduced to the fishing community. Boron was not available in long-term strips at the time and required graphite to support it. The amount of boron found in so-called boron rods is typically less than 25 percent.
Boron is now usually used in the fishing pole’s butt ends. Some fishing rod blanks may have a layer of boron and other materials wrapped around them. Boron adds strength and power, while its stiffness makes it easy to recover from bends.
The incorporation of graphite and other materials into fishing poles was a new development in technology since the eighties. R.L. Winston, Browning, and Shakespeare are some of the few remaining manufacturing companies that produce boron fishing poles. Fly rods, spinning rods, and baitcasting rods are standard boron rods.
Tennis
The Prince Boron tennis racket was one of the first applications for boron fibers in sporting goods. Additionally, it saw widespread popularity among amateurs and pros. Boron is lighter than carbon (the main constituent of graphite), so it was used in graphite composition to make the frame lighter (e.g., compared to a 100% graphite frame) but to make it stiffer (being denser for the same amount of material in a layup). Boron is a component of composite layup ingredients.
It has two main problems: it is more expensive and more fragile. However, boron transmits vibrations better than graphite because it is lighter and stiffer. Frames made of boron are very durable. Beginners who aren’t proficient in their swing may find that boron frames are difficult to control and more painful on the arms. Boron is a significant difference in graphite shafts for golf clubs. Boron reinforcement was why Yonex shafts were well-respected for their excellent distance control and low torque.
Golf
The most effective use for boron fiber in sports goods was in the early 1990s when people used it in golf shafts. Longer length and boron were added in the golf shafts to improve feel, especially in Japan. With the introduction of Callaway Golf’s Big Bertha driver, boron fiber gained popularity.
The driver was a huge hit with golfers. However, the shaft had breakage issues as the club did not have any reinforcement when the rod entered the clubhead. The problem was solved by inserting a small flag of boron fiber prepreg in the shaft area. It led to boron-fiber golf equipment manufacturers (OEMs). Textron Specialty Materials, the precursor to Specialty Materials, Inc., introduced the Boron Certified Program.
This program verified that the golf shafts bearing the “Boron Certified” sticker had sufficient boron fiber for increased strength. The widespread use of boron fiber for golf shafts was ended when most manufacturers moved their manufacturing to China.
Boron is also used in drivers for hardness – see the case study below for more information.
This new approach over this is the traditional way to make golf irons with steel, fire, and lots of hammering from a blacksmith or by pouring molten metal into molds that resemble Jell-O.
Although you can still find forged clubs, modern machines make them more than traditional blacksmiths. They are rarely found on tks and, if they are, they are usually in bags of pros or low-handicap golfers.
Case study: Mizuno’s Golf Equipment
However, just because the era of sporting goods using boron has slowed down, it does not mean there is no place for it in today’s industry. Boron technology is still used in ultra-lightweight golf shafts, golf club heads, and drivers for improved performance, strength, and durability.
Mizuno, a sporting goods company, claims it has figured out how to crack that nut using a patent-pending process called Grain Flow Forging. Chris Voshall, Mizuno engineer, says that it is different from standard forging in that it has a patent that covers bending and stretching before the club’s formation.
Mizuno’s Forging Process for Heads
The company has been adding boron to the forging process to create stronger clubs. It’s not complicated; only three parts per million boron are required in 1025 mild-carbon. It results in a more robust and durable club but has a thinner face. The club’s 2016 forged iron lineup has a look that is only 1.7mm thick. Mizuno cuts the space behind the face using either an end mill cutter (or a T-slot cutter, depending on which club it is).
Mizuno begins with a 6-inch-long metal bar. It is then stretched and bent into the desired shape. Hence, it is easier to shape the final result later. Voshall says that it gives the product a consistent feel from one piece to another.
Voshall states that we would need 2.5 to 3 millimeters without the boron for an ordinary forging. He says that the clubface is thinner for more speed. A faster ball travels farther. It can gain an additional yard or two by increasing its speed by just one mph. Mizuno claims that its new forged clubs can increase speed up to 3 mph. It could give you an extra yard or two under ideal conditions.
Mizuno’s Boron Golf Club Models
Mizuno introduced its 1025 boron steel in its JPX 850 Forged Irons in 2016. The idea was to make the faces smaller so that the clubs could hit the ball further. This iron was Golf Digest’s top-rated game-improvement club. It is currently bringing this technology to both its upper and lower levels.
Engineers realized that 1025 boron was 30 percent stronger than 1025 carbon steel. Making the steel more durable could also make iron faces thinner. A wedge such as Mizuno’s T7 is more durable because it is sharper, more precise, and lasts longer.
To further enhance the precision of Mizuno’s loft-specific groove designs, the T7 features forged 1025 Boron Steel. As with many Mizuno wedge designs, the lower lofts (45-53 degrees) have a narrower groove that optimizes spin on full shots. The higher lofts (54-62 degrees) have a broader and shallower groove to increase spin on side shots. Boron gives the strength to make the groove’s extreme geometry last longer.
The company launched the JPX919 model in 2018. In terms of ball speed, it is Mizuno’s fastest one-piece forged steel iron. This weight reduction allowed for a lower center of gravity, making flying the long and mid-irons easier. Boron was infused in the billet to make it 30% stronger. This allowed for greater design possibilities when forged heads were made.