COATING FIREARMS WITH BORON
The firearm industry has been using nickel boron coatings for many years, and this is largely because of the protective and anti-corrive benefits that it offers. Nickel boron coating results in a highly wear-resistant surface, and it also provides excellent corrosion resistance. The tradeoff to these advantages is that NiB-X coated guns are more expensive than guns with traditional chrome plating or other types of metal finishes. High-Performance Coatings with Boron; NiB-X Nickel Boron, a high performance coating that offers maximum protection against corrosion and wear. This protects your firearm investment from the elements and is guaranteed to last.
In 2000, the patent was issued for Generation 4 nickel boron, (US patent 6066406, C. Edward McComas). Generation 4 was characterized by the implementation of lead tungstate as the stabilizer in place of thallium sulfate. UCT Coatings Inc. holds the exclusive rights to Generation 4 under the brand names UltraCem, Fail Zero, and EXO.
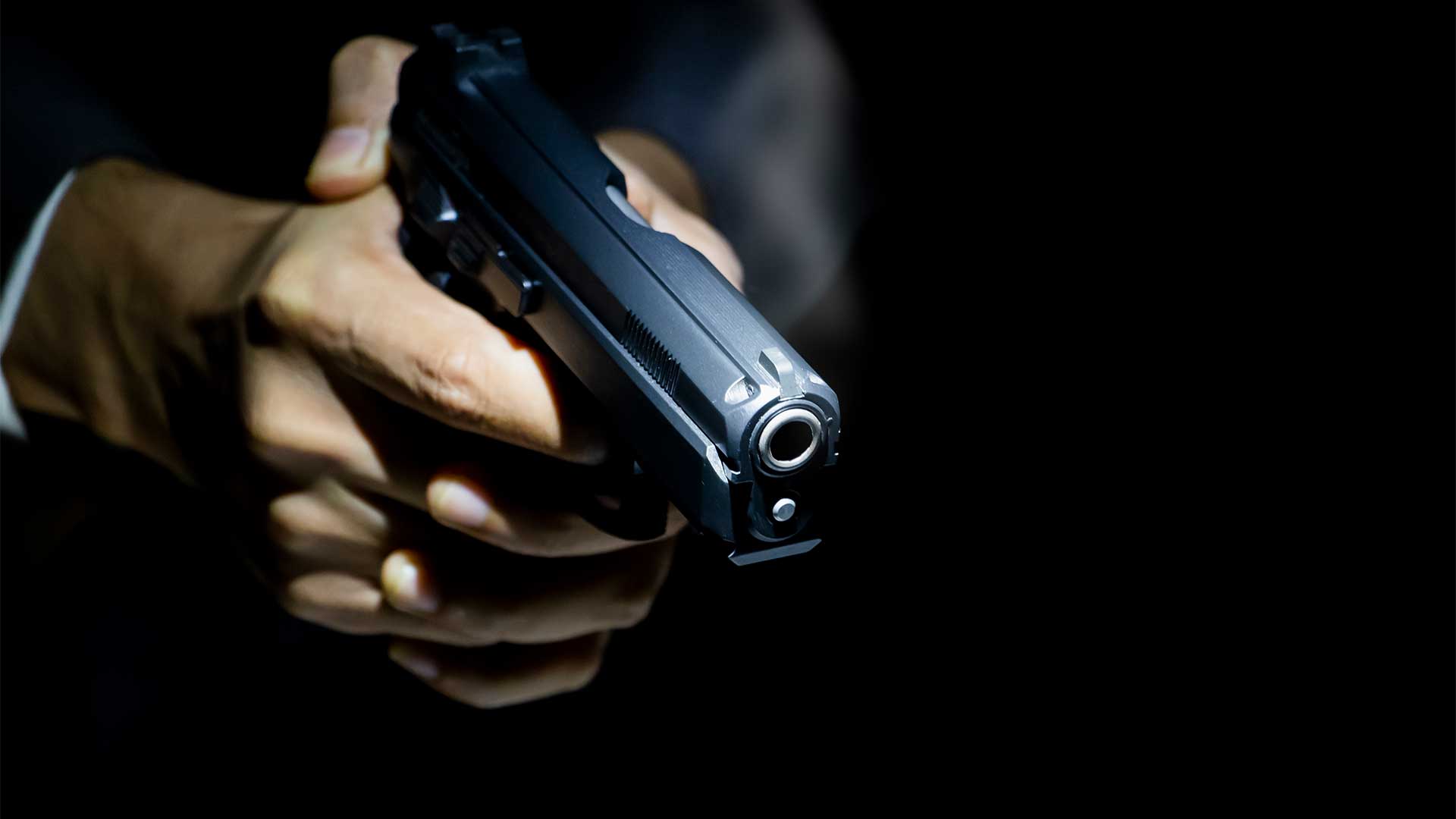
Electroless nickel-boron plating
Alkaline Electroless Nickel Boron (NiB) is an autocatalytic coating process. The coating is deposited from an aqueous solution which contains either an alkylamineborane or sodium borohydride as a reducing agent, a source of nickel Ions, a buffer, complexant, and control chemicals. Alkaline nickel boron coatings are classified as Type 1, Nickel thallium boron or Type 2, nickel boron.Also known as NiB-X, electroless nickel boron plating is the firearms industry’s first choice for corrosion and wear prevention. Electroless nickel boron plating offers a surface so hard that it will outlast traditional chrome or other metal finishes by more than three times over. This makes it an excellent investment when considering all of the long term benefits.
Ultrasound-assisted nickel boron plating
A variation on the coating is the Ultrasound assisted process of application. The formation of NiB-X layers is not sensitive to temperature, and it can be done within a wide range without any problem. This means you do not need to worry about adverse effects due to high or low temperatures for your application.
Comparisons
The process involves immersion of the part in alkaline solution containing nickel ions at elevated temperature under high electric field strength. Boron ions are injected into the nickel-rich coating by thermal decomposition of a boron compound. The resultant microcrystalline nickel-boron layer contains approximately 20% to 30% boron, which is responsible for the corrosion protection and wear resistance properties such as hardness and adhesion.
In comparison with ferritic nitrocarburizing (FNC), NiB-X has excellent corrosion protection. It also provides better adhesion than FNC to most substrates, and is easier to maintain in terms of surface condition and appearance. In comparison with traditional electroless nickel (EN), the NiB-X coating process can be used up to higher temperatures without a significant reduction in hardness or wear resistance.
Expert Discussion
One of the pioneers in the field of nickel boron is WMD Guns. They have developed their own high-end type of nickel boron coating called “NiB-X.” Whereas some companies just dip their firearm parts in a nickel boron compound and then ship it out, other companies employ people who hold a PhD in chemistry or metallurgy, to help with the application process.
According to Wynn Atterbury of WD Guns,
“Every firearm has a coating of some type but most of the legacy coatings are hundreds of years old. The new coatings can provide friction, wear, and corrosion protection far better than the legacy coatings. This provides the shooters an enhanced experience for the entire life of the firearm.
Coatings can ease the cleaning and maintenance of the firearm, reduce wear on the components, and increase the reliability of the entire system.
Another aspect that enhances the shooting experience making components with an aesthetic quality to them, or a cool factor. People like to personalize their firearms, and with our arsenal of coating technologies, we can help them do that.”
COATING FIREARMS WITH BORON
The firearm industry has been using nickel boron coatings for many years, and this is largely because of the protective and anti-corrive benefits that it offers. Nickel boron coating results in a highly wear-resistant surface, and it also provides excellent corrosion resistance. The tradeoff to these advantages is that NiB-X coated guns are more expensive than guns with traditional chrome plating or other types of metal finishes. High-Performance Coatings with Boron; NiB-X Nickel Boron, a high performance coating that offers maximum protection against corrosion and wear. This protects your firearm investment from the elements and is guaranteed to last.
In 2000, the patent was issued for Generation 4 nickel boron, (US patent 6066406, C. Edward McComas). Generation 4 was characterized by the implementation of lead tungstate as the stabilizer in place of thallium sulfate. UCT Coatings Inc. holds the exclusive rights to Generation 4 under the brand names UltraCem, Fail Zero, and EXO.
Electroless nickel-boron plating
Alkaline Electroless Nickel Boron (NiB) is an autocatalytic coating process. The coating is deposited from an aqueous solution which contains either an alkylamineborane or sodium borohydride as a reducing agent, a source of nickel Ions, a buffer, complexant, and control chemicals. Alkaline nickel boron coatings are classified as Type 1, Nickel thallium boron or Type 2, nickel boron.Also known as NiB-X, electroless nickel boron plating is the firearms industry’s first choice for corrosion and wear prevention. Electroless nickel boron plating offers a surface so hard that it will outlast traditional chrome or other metal finishes by more than three times over. This makes it an excellent investment when considering all of the long term benefits.
Ultrasound-assisted nickel boron plating
A variation on the coating is the Ultrasound assisted process of application. The formation of NiB-X layers is not sensitive to temperature, and it can be done within a wide range without any problem. This means you do not need to worry about adverse effects due to high or low temperatures for your application.
Comparisons
The process involves immersion of the part in alkaline solution containing nickel ions at elevated temperature under high electric field strength. Boron ions are injected into the nickel-rich coating by thermal decomposition of a boron compound. The resultant microcrystalline nickel-boron layer contains approximately 20% to 30% boron, which is responsible for the corrosion protection and wear resistance properties such as hardness and adhesion.
In comparison with ferritic nitrocarburizing (FNC), NiB-X has excellent corrosion protection. It also provides better adhesion than FNC to most substrates, and is easier to maintain in terms of surface condition and appearance. In comparison with traditional electroless nickel (EN), the NiB-X coating process can be used up to higher temperatures without a significant reduction in hardness or wear resistance.
Expert Discussion
One of the pioneers in the field of nickel boron is WMD Guns. They have developed their own high-end type of nickel boron coating called “NiB-X.” Whereas some companies just dip their firearm parts in a nickel boron compound and then ship it out, other companies employ people who hold a PhD in chemistry or metallurgy, to help with the application process.
According to Wynn Atterbury of WD Guns,
“Every firearm has a coating of some type but most of the legacy coatings are hundreds of years old. The new coatings can provide friction, wear, and corrosion protection far better than the legacy coatings. This provides the shooters an enhanced experience for the entire life of the firearm.
Coatings can ease the cleaning and maintenance of the firearm, reduce wear on the components, and increase the reliability of the entire system.
Another aspect that enhances the shooting experience making components with an aesthetic quality to them, or a cool factor. People like to personalize their firearms, and with our arsenal of coating technologies, we can help them do that.”