Boron Oil Extraction
Modern civilisation has been much influenced by the discovery of petrochemicals. The entire human race is driven by this natural resource, dubbed liquid gold. Petrochemical derivatives are overwhelmingly present in our lives – as plastic bags/wrappers that envelop everything from food items to clothing, as cosmetics, as the spandex garments that drape us so flawlessly, as fertilisers, or even as moulded furniture, to its crudest form – as gasoline in our car tanks, jet fuels and kerosene for cooking!
With oil defining our lives, industrialisation, and global economies, there is a need to extract every drop of it that is so painstakingly drilled. The liquid gold is limited and precious, and hence, comes boron, man’s formidable ally in boron oil extraction.
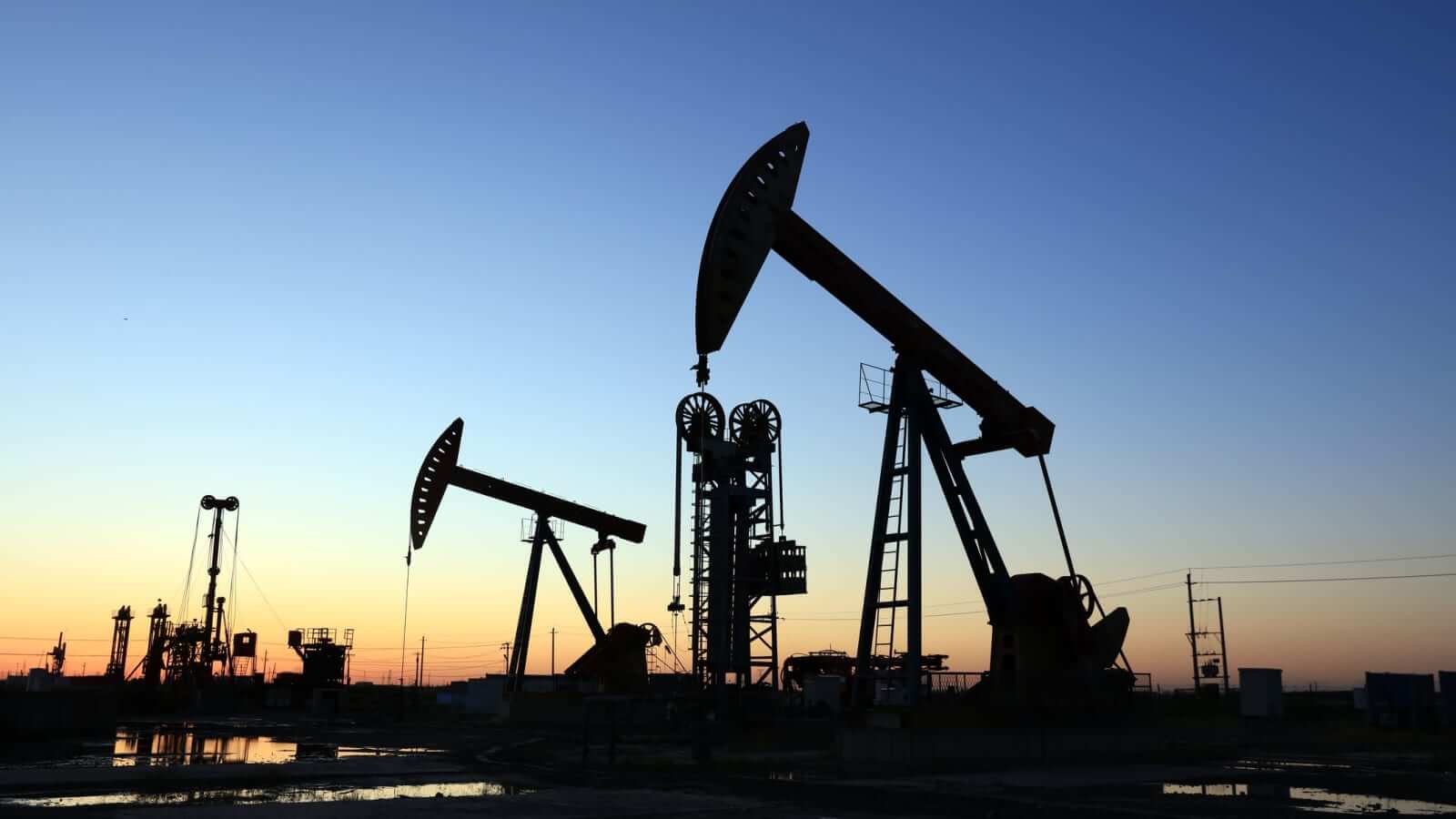
Extraction
The Business of Oil Refining
The history of the petroleum industry dates back to the first century BC as recorded in one of the earliest known Chinese writings I Ching. It cites how oil was used in its raw state (without refining) and elaborates upon oil’s discovery, extraction, and extraction. The earliest known oil wells were reported to have been drilled in China in AD 347 or even earlier.
Ever since those times, man has experimented, failed, and tried to perfect techniques of oil refining. From using extensive bamboo pipelines in the initial days to cable tools to rotary drilling in the 20th century, the man eventually mastered the techniques of oil drilling.
In the US, the history of the petroleum industry dates back to the early 19th century, although the indigenous peoples, like many ancient societies, are known to have used petroleum seeps since prehistoric times.
In the US, petroleum became a major industry following the oil discovery at Oil Creek, Pennsylvania, in 1859. For much of the 19th and 20th centuries, the US was the largest oil-producing country in the world.
As per the BP Statistical Review of World Energy 2020 (https://www.bp.com/content/dam/bp/business-sites/en/global/corporate/pdfs/energy-economics/statistical-review/bp-stats-review-2020-full-report.pdf), more than 95 million barrels per day (bpd) were produced during 2019 – roughly the same level as in 2018 and a 17% increase compared to ten years earlier.
With 17 million barrels per day, the US became the world’s biggest oil producer in 2017, overtaking Saudi Arabia to claim the top spot. The country has 18% share of the entire global output. In 2019, about 69% of total US crude oil production came from five states namely Texas, North Dakota, New Mexico, Oklahoma, and Colorado, respectively.
Challenges of Recovering Oil
As rare and precious oil and gas are natural resources to man, so are the challenges to extract them from the belly of the Earth. Hundreds of years of oil and gas explorations in extremely challenging environments, remote corners of the Earth, and from greater depths have enabled mankind to use the resource that has predominantly fueled industrialization.
The innovations in the oil industry are not just limited to drilling. From deeper wells, longer than ever before drilled into the Earth’s crust, to time constraint in recovering yields from these wells, to squeezing the last drop available from a well without wasting energies and money on repairs and replacement, engineering solutions have become paramount.
The oil and gas industry’s dependence on specialty chemicals for seamless extraction and affordable supply makes boron its formidable ally.
Boron and Borates
Boron is a metalloid, a chemical element with the atomic number 5. Found in nature as borax, or sodium tetraborate decahydrate (Na2B4O7·10H2O), it is found naturally on Earth throughout the world, including in seawater and soil.
When a naturally occurring element boron combines with oxygen and other elements to form inorganic salts, borates get formed. Borates are essentially salts formed by the combination of boric acid with a base or positive radical.
Boron in oil Wells
Historical data indicates that the first vertical wells came up in the 1930s, the first hydraulic fracturing job took place in Oklahoma in 1949, while commercialization happened in 1950. With oil and gas being the primary sources of energy driving economies, more sophisticated techniques have been developed to take advantage of these challenging geological deposits. However, it is not clear when borates were introduced in the sector.
Apart from being more environmentally friendly than competing metal cross-linkers used in oil and gas stimulation, borates’ unique properties and behavior make them an ideal option for multiple oilfield applications including retarder in concrete, lubricant, alkaline buffer to reduce water hardness, lost circulation treatments, and profile control, alkaline surfactant, hydrogen sulfide scavenger (an oxidizer of hydrogen sulfide gas), pulsed neutron well logging and hydraulic fracturing fluids. Boron is an anodic inhibitor, anti-microbial, and is the most common cross-linkers.
Borates are multifunctional additives used to control pH, viscosity, and corrosion, and to provide lubrication and various other chemical and physical effects.
Presently, borates are used in the oil fields at various phases including drilling and oil recovery.
During the drilling phase that involves locating the energy deposits, borates are used as a set retardant for cement that is additionally supported by a steel casing. Borates react with the calcium portion of the Portland cement by creating a calcium borate coating that slows down the setting of cement. Borates typically are not used exclusively as a set retardant but are included with other polymer-based systems.
Insoluble borates (Colemanite and Ulexite) are used to prevent the flow of fluids into the brine reservoir containing the completion fluids, without causing any damage to the well.
Boron and Fracking
Borate is used in fracking fluids since it reacts with soluble polymers both natural and manmade for gelation. Borates act as cross-linkers to increase or decrease the viscosity of these gels due to bond formation and breaking during variations of extreme pressure and temperature.
Borate-based cross-linkers are applied to link with polymer chains and create the viscosity required with pump pressure to fracture the rock where the oil and gas are located. Borate-based cross-linkers are used in low to mid-range polymer systems, while metallic-based cross-linkers (zirconium, titanium) are used for high-temperature polymer systems.
Borates are self-buffering, not requiring other additives to adjust the pH of the fracking solution. In addition, the alkaline borates offer an anticorrosive value when systems can become acidic.
Preborates (a reaction of Etibor 48 and hydrogen peroxide) are used as fluid breaking solutions post-completion of the fracturing process. They release the borax as a buffering compound and the hydrogen peroxide as the oxidizing agent.
Sodium perborate is used to oxidize hydrogen sulfide and offer antimicrobial value in destroying the sulfide-producing bacteria that produce this dangerous gas.
Green Boron Application for Blockage Removal
In June 2020, ACS Omega published a study entitled “Development of a New Borax-Based Formulation for the Removal of Pyrite Scales” (https://www.ncbi.nlm.nih.gov/pmc/articles/PMC7315426/) by Musa Ahmed, Ibnelwaleed A. Hussein, Abdulmujeeb T. Onawole, and Mohammed A. Saad, that brings to light a new green formulation based on borax.
The study proposed K2B4O7 for pyrite scale removal. In the oil and gas industry, pyrite forms one of the most hardened scales in reservoirs, which hinders the flow of fluids. Consequently, this leads to blockage of the downhole tubular, formation damage, and complete shutdown of production and operational processes.
The new formulation showed the potential ability to dissolve pyrite without generating the toxic hydrogen sulfide (H2S), apart from showing increasing dissolution rates, lesser corrosion rate, and is very economical.
To this day, scientists are working on formulations to make use of borates more efficiently in oil recovery.