Boron in California
Boron is found in California in the form of colemanite and ulexite. Boron can be found in arid regions worldwide, including Turkey, Argentina, Chile, Russia, and the USA. California is home to more than half the US Boron production. The Hector Basin, San Joaquin Valley, and the Mojave Desert are primary sources.
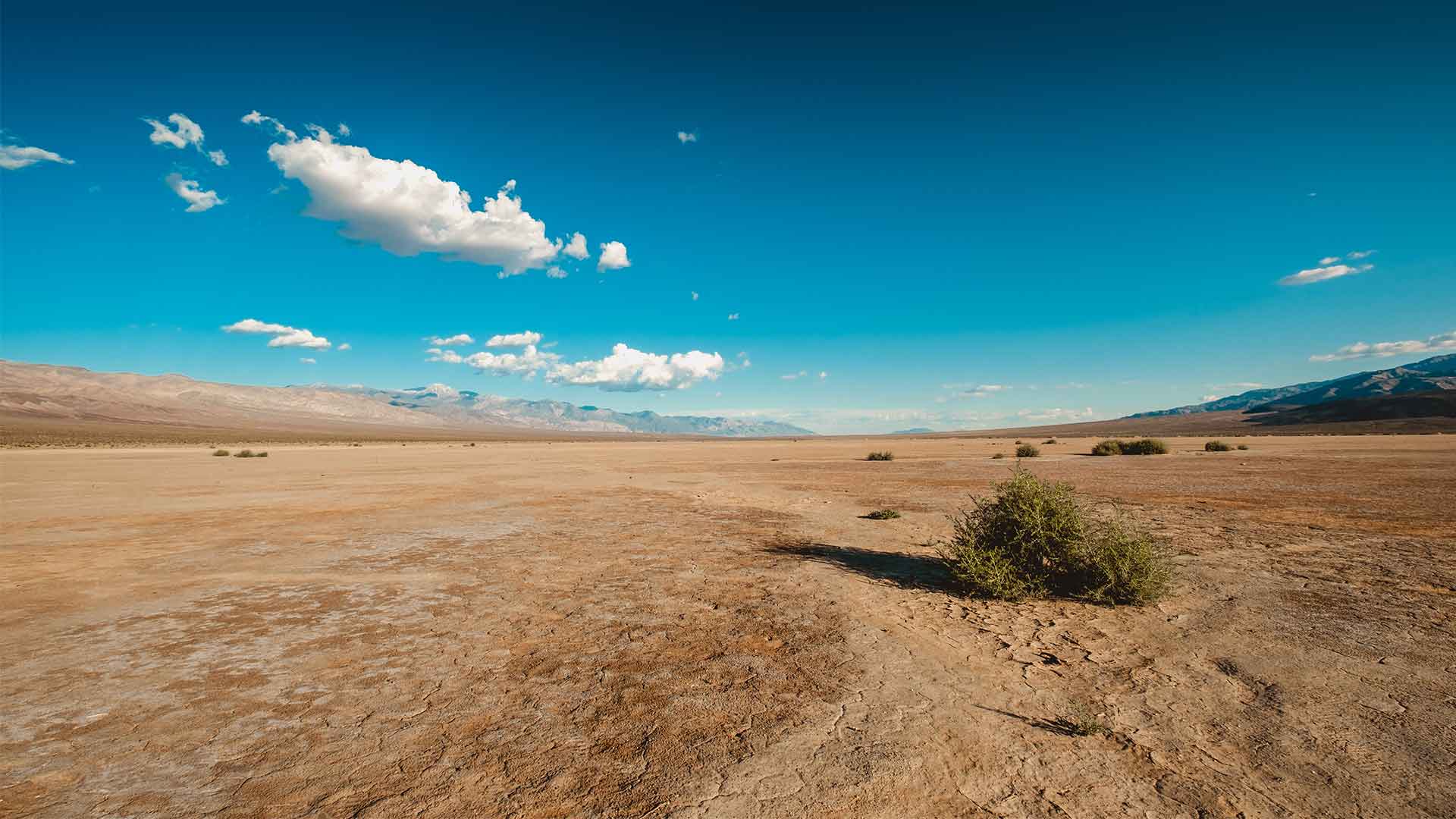
California
Extraction of Boron
Boron in California is believed to have been sourced from thermal waters that flowed from the region’s hot springs during active volcanism. These hot springs vented into the Hector Basin, which contained a large desert lake. Borates were precipitated as the thermal waters entered the lake and cooled or as the lake waters evaporated and became saturated with boron. Colemanite, the least soluble mineral, evaporated on the receding margins of the lake.
Boron is extracted from borate deposits. Borates include borax and boric acids, both examples of minerals that belong to the Borates family. Recent technological advances and increased consumer demand have fuelled increased interest in Mining Borates.
The Borax Lake Region
Three large deposits are found in this region. The eastern side of Borax lake is where the primary deposit is found. It extends to the mountains. Deep shafts have been created to extract boron minerals from the secondary deposit. The secondary deposit is located north of Borax lake. Mammoth lakes in California are where the deposit is located. It contains both borax as well as boride minerals. Borides are found in tertiary deposits. They can be extracted using deep shafts or open-pit methods. It is called the “Borax Hill Deposit.”
California’s Boron industry employs approximately 500 people. Around 70% work at the Borax lake Mine, while 30% work in other mines. Borax Inc. is the largest employer, while Borax Products Company processes borax from it.
The Borax Lake Mine is traditionally California’s most productive mine. In 2007, it produced 1,923 tonnes of boron oxide concentrate. Boron Mountain Mine was the second most productive mine, producing 803 tonnes of Boron concentrate in 2007.
In 1999, Borax production peaked (Boron concentrates), and the cost of Boron oxide has increased significantly over the years. Borax lakes have been rediscovered as a potential for high investment and return.
Companies in California
There are significant Boron extraction operations in California, namely Rio Tinto and US Borax with newcomers, like American Pacific Borates, to the region exploring historical sites of borates reserves and committing investment to deliver boron to the market as demand rises for uses in advanced energy, food security, and decarbonization.
5E Advanced Materials
5E Advanced Materials (FEAM) is a producer of Borates with mining operations based in California. FEAM’s Fort Cady Project is situated right in the heart of California’s borate reserves. It is a large and rare colemanite deposit that is not owned by Rio Tinto or Eti Maden. It has also the most significant traditional borate occurrence owned by neither significant borate producers Rio Tinto, nor Eti Maden.
The Fort Cady Borate deposit was first discovered in 1964. From 1977 through the early 2000s, the deposit has undergone exploration, pilot ISL testing, feasibility studies, and limited production. ABR purchased a 100% interest in the Project in May 2017 from Atlas Precious Metals Inc. Since that time, the Project has undergone additional exploration, permitting, and development activities.
Following exploratory drilling, a mineral resource estimate was prepared for the Project in late 2017, and updated in December 2018 where a feasibility study outlined a three-phase project to produce 450 kstpa boric acid (BA) and 20 kstpa sulphate of potash (SOP). This estimate has been further increased in 2021.
Note: As of 15/03/2022, American Pacific Borates is now listed on NASDAQ under the ticker FEAM (5E Advanced Materials). Find details – here
Rio Tinto
Rio Tinto’s Miocene Kramer bed is divided into three distinct parts, the Saddleback basalt, Shale, and Arkose members. This includes up to 800 feet of arkosic sandstones that are silty and interbedded in tuffaceous and tuffaceous clays. The Kramer ore body, roughly lenticular in sedimentary form of Borax (Na2B4O7.10h2O), and kernite (7.4h2O), contains interbedded claystone. The central crystalline facies are successively surrounded by facies of ulexite (7.4H2O), colemanite (6O11.5H2O), and barren claystone (Ca2B6O11.5H2O). The Kramer borates may have been deposited in a small, structural, non-marine associated with thermal (volcanic) spring activity during the Miocene.
Seven stratigraphic units are used to divide the Sodium borate facies:
- The four highest-grade units are the Upper, Middle, and Lower ores. They all contain more than 75% borax.
- The three general low-grade units A-zone and B-zone, contain less than 60% borax typically.
- Basal ore is one of the thinnest and most extensive high-grade units. The lower ore, on the other hand, is thicker and higher grade.
All units are only found in the thick central part of the sodium-borate facies. The sodium borate facies contain a variety of clay-tuff and claystone marker bed beds that maintain stratigraphic control.
US Borax
U.S. Borax is committed to providing the world with quality materials in a sustainable and responsible manner, despite borate deposits being found relatively infrequently throughout the environment.
1. Mining and refining:
Mining and refining are major components of their business. They are the world leader in refined borate ore production, producing 1 million tons annually from their Boron mine. The unique site measures 2.8 km wide, 3.2 km long, and 230 m deep; it also houses 80 minerals including four critical to industrial applications: Tincal, kernite, ulexite & colemanite which we process into commercial grade pentahydrate/decahydrate borates as well as anhydrous goods like boric acid at numerous ISO14001 certified sites worldwide.
2. Blasting and drilling:
Blasting and drilling serve as essential components in the exploration process. By introducing drills into a computer-driven system, companies gain valuable insight into underground minerals allowing them to map out long-term mine plans accordingly.
3. Hauling and Shoveling:
The mine is alive with roaring engines and the thunderous sound of large shovels, scooping up ore fragments from its depths. Massive haul trucks then transport 220 tons worth of material to crushing machines that break down rocks into smaller pieces for efficient refining processes. Across the refinery, conveyors wind their way around buildings as they ferry vital resources between locations.
Evolution of Boron
In 1994, the world’s total production of boron minerals was 2,750,000 tonnes. Commercial borate products made from these minerals contained approximately 250,000 tonnes of Boron. This corresponds to 800,000 tons of boron oxide (B2O3). Crystalline Boron costs $5/g on average. Boron can be used to make boron fibers. It is deposited on a core of tungsten by chemical vapor deposition (see below). Boron fibers can be used in lightweight composite applications such as high-strength tapes.
This is only a tiny fraction of the total boron usage. Ion implantation introduces Boron into semiconductors in the form of boron compounds.
In 2012, the global consumption of Boron (almost exclusively as boron compounds) was approximately 4 million tonnes of B2O3. Boron refining and mining capacities are adequate to support the expected growth over the next decade.
In recent years, the form of Boron has changed. Concerns about arsenic have led to a decline in the use of colemanite ores. Consumers are now using refined borates or boric acid, which have lower levels of pollutants.
Many boric acid producers have invested in new capacity due to increasing demand. Turkey’s Eti Madane Mine Works, a state-owned company, opened a boric acid plant at Emet in 2003. It has a production capacity to produce 100,000 tonnes annually. Rio Tinto Group has increased the power of their boron plant from 260,000 tonnes per annum in 2003 to 310,000 tonnes by May 2005. Plans were to increase this to 366,000 tonnes annually in 2006.
The rapidly growing demand for high-quality Borates has made it difficult for Chinese boron producers to keep up with the fast-changing market. This has resulted in imports of sodium Tetraborate (borax) growing 100-fold between 2000 & 2005 and boric acid exports increasing by 28% annually over the same period.
High growth rates in glass fiber, fiberglass, and borosilicate production have driven global demand. The rapid rise in the output of reinforcement-grade, boron-containing fiberglass has offset the development in Europe and the U.S. of boron-free reinforcement-grade fiberglass.
Recent advancements in energy costs may hurt the use of insulation-grade fiberglass and the consequent increase in boron consumption. Roskill Consulting Group predicts that the world’s demand for Boron will rise by 3.4% annually to 21 million tonnes by 2010. Asia is likely to see the highest demand growth, with an average 5.7% annual increase in demand.