Boron Carbon Capture Research
Carbon capture – Boron Carbon Capture Research –is a way to reduce carbon emissions and could play a key role in combating global warming. Pre- and post-combustion carbon capture is possible. Boron’s properties as a solid absorbent allow carbon dioxide to be captured more efficiently in the first stage of the capture process.
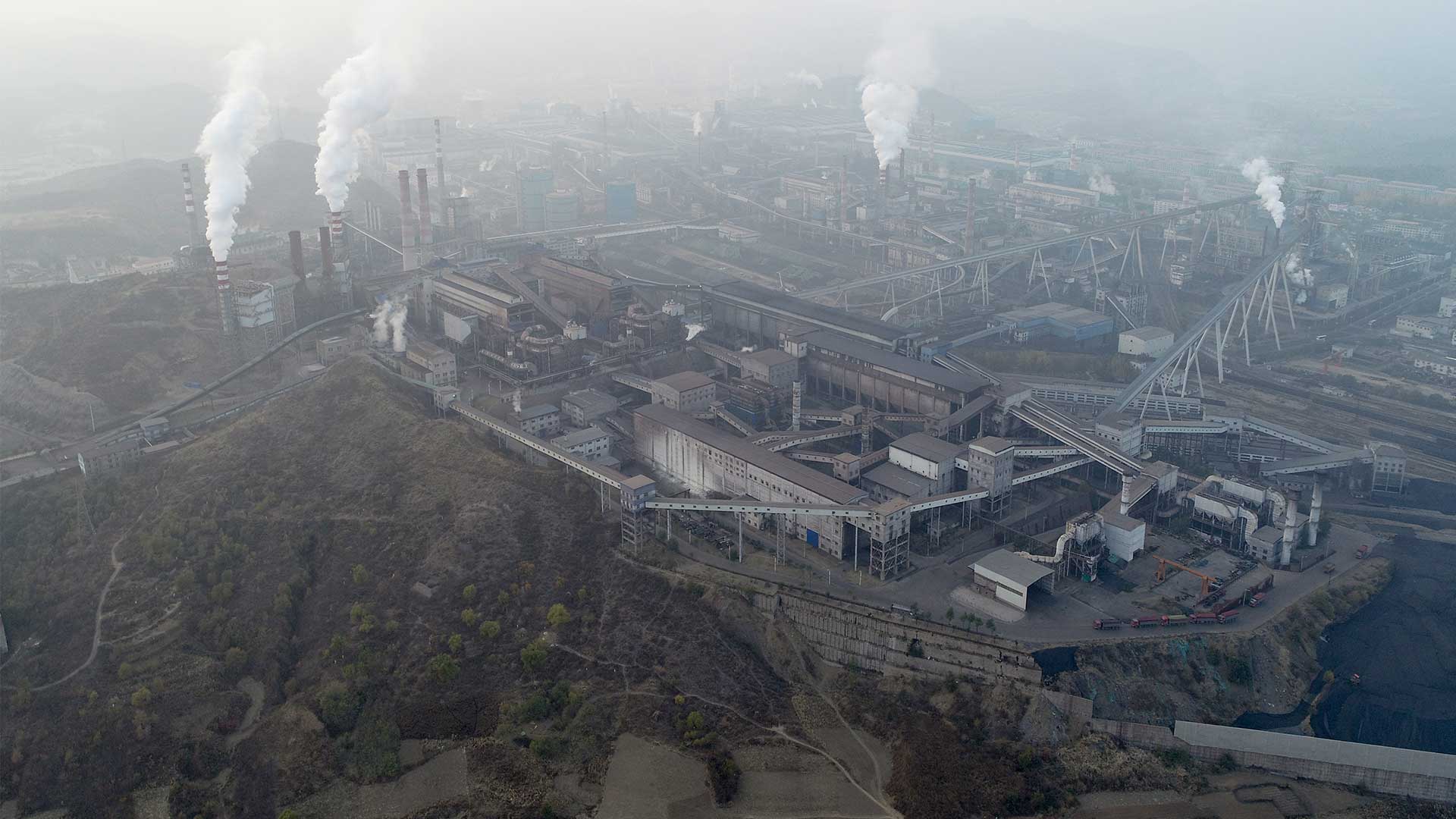
Boron Carbon Capture Research
In a three-step process, carbon dioxide created by power generation or industrial activity, such as steel production or cement making, is captured, transported, and then buried deep underground. By doing so, we can prevent it from entering the atmosphere and contributing to climate change.
Pre-combustion – Improving efficiency through pre-combustion carbon capture
Pre-combustion carbon dioxide capture is the process of capturing CO2 from a combustion exhaust stream before combustion occurs. Chemical solvents are used to trap CO2. Industrialists have used this method since the 1950s, but it was not widely adopted until the 1990s when new technologies made it more affordable and easy to use.
Boron’s Properties as a Solid Absorbent
Boric acid (H₃BO₃) is one of the most common compounds used by pre-combustion systems for carbon capture. It is an excellent carbon dioxide absorber. In fact, boric acid absorbs carbon dioxide so well that it can even remove some of it from the air.
It is also able to withstand high temperatures and pressures, which makes it useful for a wide range of applications. These properties make it an excellent carbon dioxide trap.
How the Process Works
Here is an example of how the process works on a small scale. The carbon capture process might be more complex in larger plants.
A scrubber is used to absorb carbon dioxide from exhaust gases at the beginning of the process. Following that, the mixture of gas and water is pumped into a chamber. After mixing, a bed of boric acid is sprayed over the mixture. When the gas reacts with the boric acid, the carbon dioxide dissolves into the liquid.
The solution flows from the scrubber back into the chamber as soon as all carbon dioxides have been dissolved. The result is pure carbonated water.
Carbon dioxide is removed from exhaust gas multiple times until no carbon dioxide remains. It is now safe to release the exhaust gas back into the atmosphere.
Why is Pre-combustion CCS Important?
In addition to providing a higher level of carbon capture than conventional methods, pre-combustion carbon dioxide capture is important. Traditionally, carbon dioxide is removed after combustion.
The pre-combustion method captures carbon dioxide in the formation process. As a result, less energy is needed to capture carbon dioxide.
Difference Between Pre-combustion and Post-combustion Carbon Removal?
Post-combustion carbon removal involves removing carbon dioxide after combustion. Post-combustion carbon removes carbon dioxide after combustion has occurred. This means that the amount of carbon dioxide removed is limited to what is available in the exhaust gases. If there is not enough carbon dioxide in the exhaust gases to be captured, then none will be removed.
Post-combustion carbon emission reduction is often called ‘afterburners’ or ‘post-combustion’. However, these terms do not refer to the type of engine. Instead, they refer to the location where the carbon dioxide is removed.
The main advantage of pre-combustion over post-combustion carbon emissions reduction is that it allows for much higher levels of carbon capture.
The main disadvantage of pre-combustion is that it requires additional equipment and processes. For example, a separate scrubber must be added to the system.
Post-Combustion Carbon Capture
Post-combustion capture is the process of removing CO2 from power station flue gas and transporting it for storage in a suitable geological formation. It is one of the many methods used to mitigate the effects of carbon emissions from fossil fuels. However, this process isn’t always an effective one. The best solution for post-combustion emissions is a combination of technologies. Here’s a look at the process.
Techniques Involved in Post-Combustion Carbon Capture
CO2 is captured by two main techniques: CO2 adsorption and post-combustion carbon capture. Currently, only the gas-to-air separation process has completely eliminated CO2 from flue gases. The first method, scrubbing, involves using a chemical reaction to remove CO2 from flue gases. The second method, thermal capture, is more expensive, but it can also remove a large amount of carbon.
Several research groups have confirmed that absorption is the most mature post-combustion CCS technology. In the last two years, a variety of advanced carbon-capture technologies have been developed. The most common one is the use of an adsorbent, which can be a mix of different materials, including zeolites and activated carbon. The third technique, bio-fixation, uses a membrane to trap CO2.
The latest technology is a hybrid capture system that integrates attributes of different technologies. The main advantage of this approach is that it can reduce the energy cost of CO2compression and reduce the costs associated with the process.
It can also improve the performance of the gas purification and separation process. The most important drawback of this technique is that it requires modifications to the steam cycle. The only drawback to this method is that it is not suitable for all applications.
A new process has been developed called hybrid capture. This process combines multiple types of carbon capture technologies and enables the use of multiple techniques. Its main advantage is that it prevents CO2from escaping into the atmosphere.
There are currently several commercially available systems that can help reduce CO2 emissions. The goal of a hybrid system is to combine attributes of multiple technologies in a single unit. In addition to a hybrid system, another technique is a membrane-based one.
Goal of Post-combustion Capture
The post-combustion capture of CO2is intended to be used in power plants. Once the CO2 has been transported, it is stored in geological formations suitable for the process. After being compressed, the CO2is released into the atmosphere. In this way, it can be transported to any location and be stored for future generations. These technologies are both cost-efficient and effective. Ultimately, a hybrid system will reduce the costs of post-combustion carbon capture.
Benefits of Post-combustion Carbon Capture
There are many benefits to post-combustion carbon capture. It is a cost-effective option that prevents emissions of CO2into the atmosphere. The technology is available for both large-scale and industrial applications. As long as the gas is treated with carbon-free amine, it will help the environment. Its benefits also extend to the environment. This technology is a viable solution for the reduction of CO2pollution.
The first generation of Post-Combustion Carbon Capture (PCC) plants is already in operation. A single unit of this process can capture up to one million tons of carbon dioxide per year. Moreover, this technology is more cost-efficient than most other technologies. It can also be a part of a hybrid system. But there are a number of challenges, which prevent this technology from becoming mainstream. The technology is costly, so it needs to be optimized for the process in question.
A hybrid system combines multiple technologies and is cost-effective. It can be used to capture CO2and other impurities. Thermoflex is a high-performance model that can be used to simulate the performance of an adsorbent-based process. Thermoflex has a wide range of benefits and is a reliable choice for many industries. Its cost is relatively low.
Commercial Post-Combustion (PCC) plants are among the most effective methods for capturing CO2from flue gases. In the U.S., a typical PCC plant can remove 90% of CO2from 240 MW of gas-fired electricity. The technology has several advantages over first-generation capture processes. The PCC technology is efficient, and it can be retrofitted into existing power plants.