Boron and Borates in Paper Production
Borate compounds are widely used in chemical processes and recovery by paper mills all over the globe. Sodium borohydride is used in boron in paper production primarily to bleach paper in the preparation stage. Boron is also used in the form of borax pentahydrate to support causticising. Borate autocausticization is a cost-saving technique that can help paper mills save money on material, recovery, and energy.
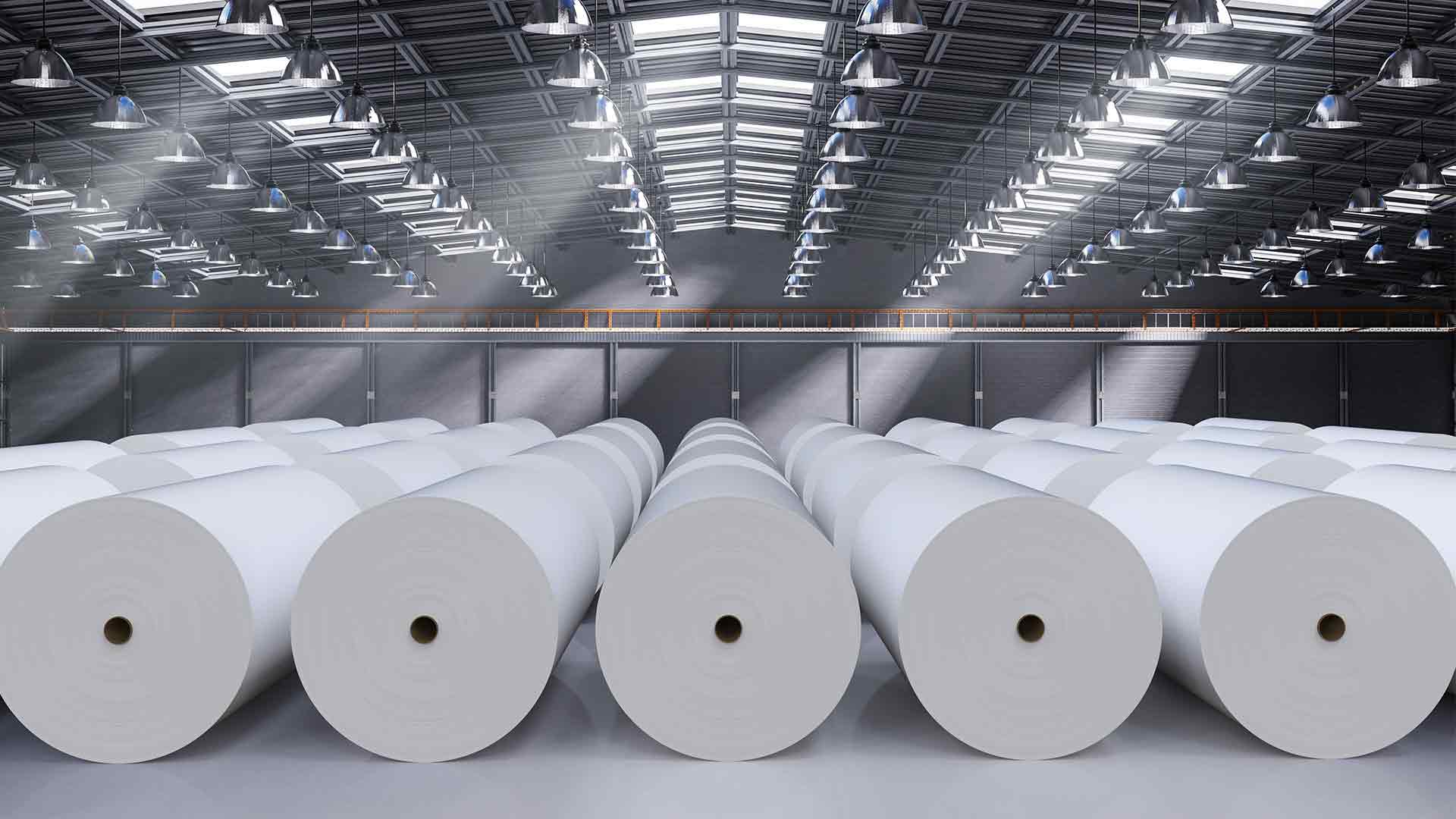
Boron in Paper Production
Borate Compounds Used in Paper Production
Before we look at Borates compounds used in paper production, here is a quick overview of the paper production process: Paper mills are complex, requiring many processes to make wood into paper. The final product required determines the processing options and the type of wood used.
Paper Production: An Overview
Pulp for papermaking can be made from virgin fiber using chemical or mechanical methods or by recycling paper. The primary raw material is wood. Used paper is the main raw material for recycling. However, straw, hemp, and cotton can also be used in some cases.
The two-step process of making paper is when a fibrous material is made into pulp and then into paper. First, the harvested wood is processed to separate the fibers from the lignin. The pulp can be made chemically or mechanically. Depending on the paper produced, the pulp is bleached and then further processed. The pulp is then dried in the paper factory and pressed into paper sheets. An increasing percentage of paper and other paper products can be recycled after use.
Pulp Bleaching
Sodium borohydride – NaBH4 – acts as a reducer in sodium hydrosulfite (Na2S2O4) bleach during the mechanical pulping process. Hydrosulfite is a chemical that decolorizes wood’s lignin. This is in contrast to chemical pulping, which removes most of it. Lignin is responsible for the brownish color of unbleached mechanical pulp.
A sodium borohydride bleaching agent produces high-finished strength paper. It has good printing, ink-absorbing, brightness, and yield. While paper bleached with hydrogen peroxide bleaching agent is 10% brighter than similar products, production costs are higher.
Sources of Sodium Borohydride
Canada, Sweden, and Finland are the top producers of sodium borohydride for mechanical pulp processing. A few producers are concentrated in sodium borohydride production, including Aviabor from Russia, Vertellus Specialty Materials from the USA, Jiangsu Huachang Chemical from China, Kemira from Finland, and Montgomery Chemicals from the USA.
Dow Chemical was a prominent manufacturer, but it agreed to sell its sodium-borohydride business in the first quarter of 2015 to Vertellus Specialty Materials. Dow Chemical produced BOROL, a mix of sodium borohydride & sodium hydroxide. This is then added to a mixture of aqueous sodium hydroxide and liquid/aqueous sulfide to make sodium hydrosulfite bleach. The BOROL bleach generating unit allows a mechanical pulp mill to generate its hydrosulfite bleach at a fraction of the cost of commercial bleach.
Boron Paper Bleaching
Source: https://micropump.com/solutions/pulp-and-paper-bleaching
Causticizing
Pulp is the basis of the paper. This pulp can be made using the sulfate method, which involves cooking woodchips in strong white liquor. This process results in chemicals circulating in the pulp mill’s recycle line. These chemicals are adjusted by a causticizing procedure using quicklime.
The lime is carbonated, and the resulting lime mud is burned in the mill’s furnaces. Rio Tinto has also developed a partial borate autocausticizing technology (PBAC) using Neobor, borax pentahydrate, as an alternative to conventional lime causticizing.
Pulp mills use PBAC for various reasons including reduction of lime mud consumption, for lime mud disposal, to increase white liquor/pulp output, which helps reduce energy/maintenance costs), and removes blockages in the causticising circuit.
This process converts some Na2CO3 in the smelt to NaOH within the smelt dissolving tank. The conventional caustiziser continues to cause the rest of Na2CO3 to dissolve in the smelt dissolving tank. The liquor cycle is completed by adding borax pentahydrate. Hydration of the borate melt yields sodium metaborate (NaBO2) and caustic. Sodium metaborate, which is water-soluble, stays in solution and forms caustic in the chemical recovery cycle. To compensate for process losses, borax pentahydrate will be required.
Neobar provides several benefits. Lime mud is created when quicklime is used in the causticization process. This lime mud must be recycled or discarded. Borate autocausticizing decreases the lime required for white liquor production, which results in less waste. This means that less lime is used in the recovery process and reduces CO2 emissions. The mills save money by replacing 10 to 50 tons of lime with Neobor. Because Neobor significantly reduces the energy required to burn lime and make quick lime, mills can also lower operating costs. Neobor can increase white liquor production without investing in equipment upgrades. This results in significant operational efficiency improvements.
There is no need for special equipment to load it, so mills can continue using existing equipment with minimal capital investment. Neobor is easy to add, depending on which mill it can be added at any stage of the liquor cycle.
PBAC technology is used in pulp mills worldwide to complement conventional lime causticizing. RTM and Buckman, an American producer of specialty chemicals for pulp & paper production, announced in 2009 a license agreement to market the proprietary technology in Africa (South Africa), Asia (China, Indonesia, South Korea, and Thailand).
Paper Production Companies
Below are some of the top paper-producing businesses around the globe.
International Paper is the world’s largest pulp and paper mill and the leading producer of pulp-based packaging, paper, and paper. The company converts renewable resources into products people can rely on every day. It is located in the USA. With 72.397 million tonnes of paper produced, the United States of America is the second-largest paper producer. The US recovered 52 million tonnes (315 pounds) of paper per capita in 2015.
Georgia-Pacific Corp. is a leading manufacturer of tissue, pulp and paper, packaging, building materials, chemicals, and other chemicals around the globe. This company is a world-famous manufacturer and marketer of building products, tissue packaging, paper, cellulose, and other related products.
Finland’s Stora Enso is the largest paperboard producer and paperboard manufacturer in terms of capacity. Stora Enso still has its primary market in Europe. However, the company also has North America, Latin America, and Asia. The company is a leader in providing sustainable solutions in packaging, wood constructions, biomaterials, paper, and global markets.
Kimberly-Clark Corp. is the USA’s leading hygiene product group. It has several globally recognized brands in its K-C portfolio. This company is focused on the hygiene sector and organized into three business segments – personal care, consumer tissue, and business-to-business.
Oji Paper is Asia’s largest producer of Pulp and Paper. The company manufactures the products and is active on the Japanese market. It has forest interests of 143,000 hectares worldwide and imports approximately 3.6 million BD tonnes of chips into Japan. The company offers a variety of products, including newsprint, publication papers, corrugating media, tissue, and thermal papers.