Boron Production
Boron is a naturally occurring chemical element. Fifth, on the periodic table, it doesn’t exist in elemental form. It combines borax, boric acid, kernite, ulexite, colemanite, and borates. It combines with oxygen to form borates.
These have myriad applications across various fields. There are more than 200 minerals that contain boric oxide, but relatively few are of commercial significance. These are found mostly in arid regions of California and Turkey. Pure boron is extracted and converted into various agricultural and industrial products through diverse and complex processes.
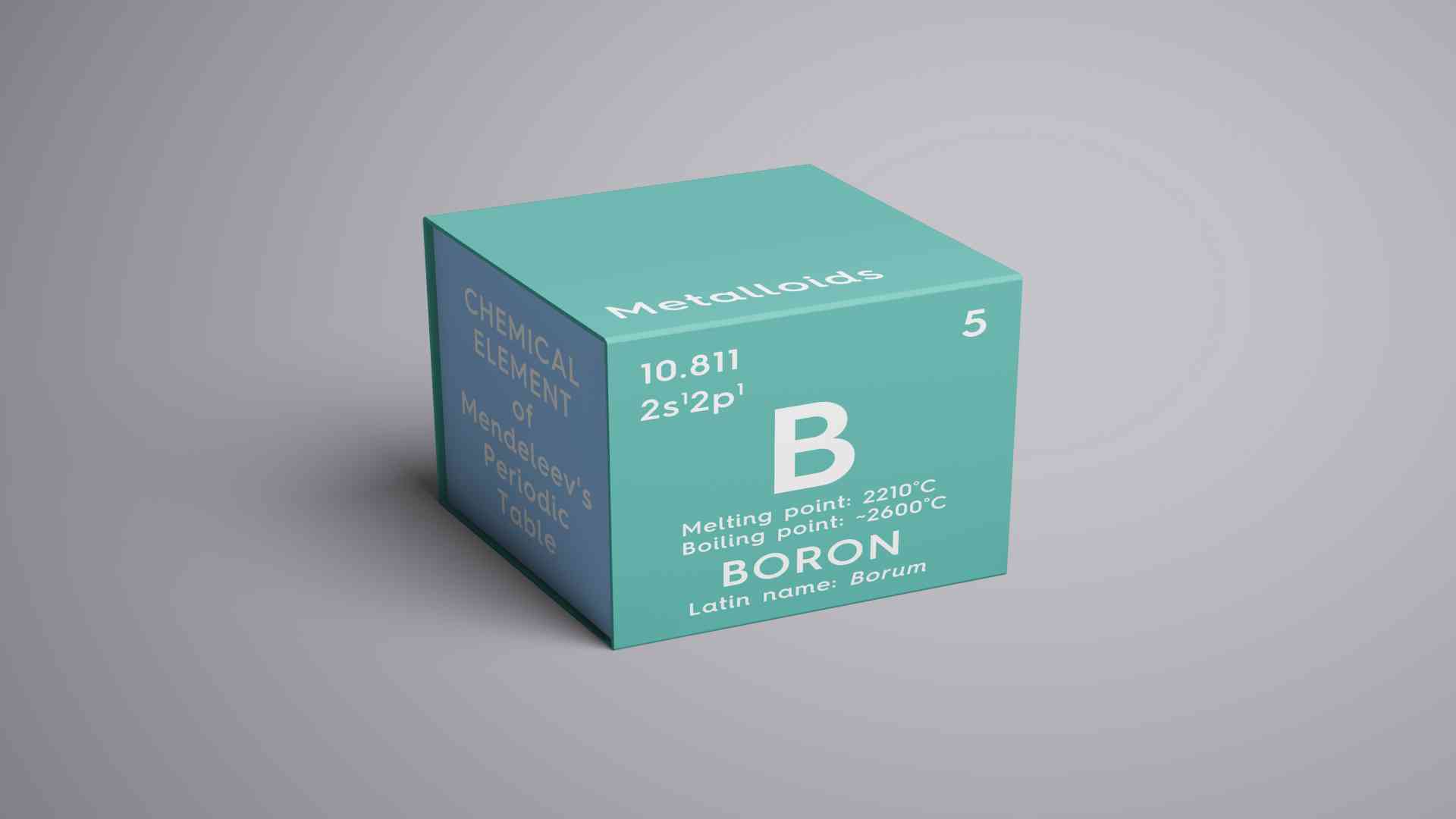
What are Boron and Borates?
Boron is a chemical element with the atomic number 5. A semimetal of leading group 13 is mainly found in the oceans, coal, sedimentary rocks, and some soils. Borates are a family of chemical compounds with boron as their central atom with specific oxidation states among the three valence levels.
They have many uses, from water treatment to glass or ceramic crucibles and fireproofing agents. In chemistry, they are used as oxidizing agents. In metallurgy, they are non-toxic replacements for lead and mercury salts in some alloys, such as oil-hardening type bearings made from high units of copper and borax.
Where is it Naturally Found?
The primary source of both boron and borates is mining minerals containing boron, for example, colemanite, ulexite, tincal & kernize. Three minerals represent almost 90% of the borates used by industry: borax, a sodium borate; ulexite, a sodium-calcium borate; and colemanite, a calcium borate.
Only certain deposits located in dry regions like Turkey or California – American Pacific Borates’ Fort Cady resources – allow them to be mined economically due to their location near surface water sources which acts as an affordable chemical processing plant for turning these elements into valuable products such as fertilizers. Other areas where the deposits are found are arid regions of Argentina, Chile, Russia, China, and Peru.
A Brief History of Boron Production
Boron was first isolated (1808) by French chemists Joseph-Louis Gay-Lussac and Louis Jacques Thenard, who independently prepared it from boroxides, potassium metal. The impure amorphous product brownish-black powder was the only form of this element known for more than a century. In 1867, Sir Humphry Davy discovered pure crystalline forms to reduce its halide compounds using hydrogen heated over an electrically powered tantalum filament at 600°C – 700 °F (320 º C).
As stated in An Introduction to Boron” by William G. Woods from the Office of Environmental Health and Safety, the University of California, Turkey’s borate industry began in 1865 with the mining of calcium pandermite. Several deposits were found across America at about this same time, including ulexite and colemanite near Death Valley (which could be converted into sodium tetraborate by reaction).
The Kramer deposit—now known as Boron—California was first discovered in 1913 when it consisted primarily of molybdenum ore, but soon afterward, tincal ores appeared. Finally, new minerals like rasorite had been encountered, eventually becoming an essential source for the country’s most essential export—borax itself.
The Environmental Health Criteria (204) report suggests that the total world production of boron minerals was approximately 2,750,000 tonnes in 1994. About 800,000 tonnes of commercial borate products were manufactured from the minerals—mainly agricultural and industrial products.
Production Processes
Mining from Natural Deposits
Drilling
To mine boron from natural deposits, it’s necessary for a company or individual miner first to have access to and knowledge of its location. Drilling is an important part of exploration and is the best way to sample what could be lurking underneath. Information about the deposit’s location composition comes from a computerized drill file which helps develop long-term mine plans for future use in mining decisions.
Blasting
Drills are used to break up the rock at a mine’s excavation site. Drilled holes can become blast holes, filled with explosives and detonate when necessary for mining processes like blasting loose sandstone (overburden) above boron ore or creating tunnels through hard formations of rocks.
Shoveling and Transportation
After the ore and overburden are loosened, enormous shovels scoop up rubble from below. The ore needs to be crushed before it is refined. Later, it is transported via an extended system.
Refining
The first step in refining boron ore is to crush and grind it into a finer powder. Next, the ground boron ore is mixed with water. Insoluble rocks, sand, and other solids are removed using screens. Then it’s heated until it becomes a liquid.
After cooling, the mixture turns into a white solid called boric acid. Borax crystals are made by heating boric acid to evaporate water and leaving behind pure crystalline borax.
Finally, the refined product is washed and dried before being packaged for sale or used as an ingredient in other products.
Evaporation
A new process has been developed to extract boron from seawater and evaporate brine to produce sodium sulfate crystals. The method of boiling water and adding a chemical to make sodium sulfate crystals is called evaporation. Seawater is used as the liquid solvent for the brine that contains boron ions which turn into solid when you heat them enough (typically over 100 degrees Celsius).
The extraction process extracts these valuable B2+ cations from deep beneath our oceans and other minerals like magnesium chloride or silicon dioxide, which all end up on land where they’ve been known to contribute significantly towards making fertilizers. The input materials are inexpensive, while the output can be used in various industries for making plastics or fertilizers with fewer environmental impacts than traditional manufacturing practices.
Mining by Conversion of Coal Into Coke
Coal conversion into coke has been used for centuries. Nowadays, it is possible to extract boron from this by converting the gas directly or through hydrogenation, which turns CO2 and H²O molecules back again, leaving behind pure boron. The first step is the combustion, where lignin and other chemicals are released as byproducts that are not burned during the process but condensed at its ceiling to form a solid residue called coke. Once this conversion happens, boron can be extracted from it and used for various purposes, such as fertilizer or pesticide.
Uses of Boron and Borates
Borates are a unique class of chemicals with many interesting properties. They have been used for years to create products like fertilizers and pesticides. Still, with ongoing research, it has been discovered that boron has potential applications in several other fields and serves as a more efficient and affordable alternative. Today, borates are used in various applications; the major markets are insulation fiberglass, textile, detergent, and bleach.
Borates impart strength, heat, and impact resistance to glass and glass fibers. It is used in fire retardants, wood preservatives, pest control products, and herbicides. It is also crucial in maintaining plant, animal, and human health.
Note:
As of 15/03/2022, American Pacific Borates is now listed on NASDAQ under the ticker FEAM (5E Advanced Materials). Find details – here.