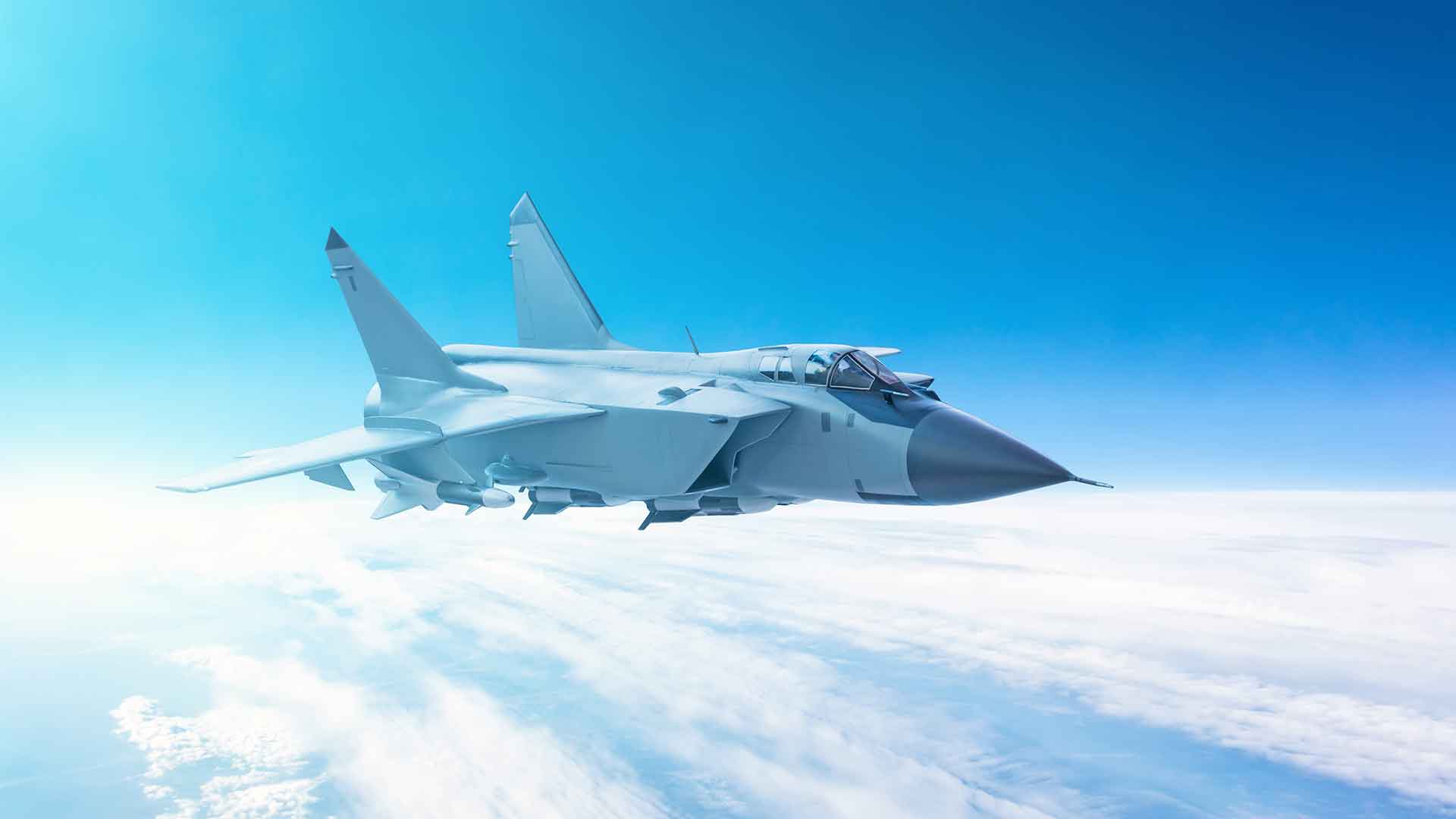
What makes Boron different from other materials?
The boron atom can create a range of materials and alloys that are important for projects in the Aerospace industry. Due to their similar boiling points, the element tends to form borides with other metals, especially aluminium, titanium, and copper. This creates a solid material resistant to corrosion or oxidisation from exposure to various types of environments.
It’s properties make it difficult for different elements (especially Oxygen) to penetrate through its chemical bonds, meaning that this metal will not rust over time and maintain its strength even when exposed to harsh conditions such as extreme temperatures (-200C up until 1000C). For example, Boron is added to engine components, so they do not become brittle.
Moreover, It can be doped with other elements to produce various properties. By doping Boron with Aluminum, you can create a material that has the conductivity of Copper but does not corrode like Iron or Steel would in saltwater.
Another way Boron makes Aerospace and defence applications so advantageous is its ability to withstand extreme temperatures without melting or becoming brittle and being an excellent conductor of electricity at low cost. Due to these unique qualities, it typically comes into play when designing parts for aircraft because it performs better than most metals over time while also creating less interference within electrical systems.
It’s stability even leads some military contractors to use it on ships since it will stand up against steel structures exposed to saltwater for years without showing any signs of corrosion.
These same characteristics have made it worthwhile when creating delicate instruments like telescope mirror cells because they need only be supported at their edges instead of being rigidly mounted on three sides with additional structural support welded or bolted into place before brazing-the entire cell frame could then be constructed without having any part protruding past the finished design profile.
Boron Carbide’s growing importance in the aerospace industry
As per a research study by FMI, the global market for boron carbide is estimated to be valued at around US$ 118,000,000 in 2018, which is expected to expand at a CAGR of ~4% throughout the forecast period of 2019 – 2029.
Today, its carbide is used in three major sectors – aerospace and defence, electrical energy storage devices (e.g., batteries) and high-temperature ceramics. Boron Carbide’s growing importance in the aerospace industry is based on its ability to withstand extreme temperatures with a melting point of over 5600 degrees Celsius and an excellent resistance against corrosion from molten salts found at various levels inside jet engines during the takeoff phase.
The properties which make its Carbides attractive for use as an alloying agent includes chemical inertness at elevated temperatures or exposure to gases such as hydrogen fluoride, low thermal expansion coefficient (~0.06% per degree Kelvin), etc.
The global boron carbide market is estimated to grow over the forecast period due to numerous factors, including research and development of bulletproof vests in the defence sector. As it has been found that Boron Carbide can be used for developing military tanks as well as enhancing bullet-resistance properties of body armour, ongoing advancements in the defence sector will augment consumption across geographies.
The world’s demand for boron carbide is expected to rise significantly because many reasons behind this increase, such as a significant number of developments relating to protection technology. The first reason is an increasing amount of investment going into researching new ways to protect people from bullets, including creating better protective gear like ballistic helmets and armoured vehicles made out of different materials.
Boron Fibre: The underrated scientific breakthrough
Origin
In January 1969, 2 different corporations were contracted by the military to design their F-14 and F-15 aircraft, respectively. Both aircraft were fixed-wing designs that required a robust and high-modulus fibre to reduce flutter and minimise the weight of each plane.
The revolutionising material on the horizon was carbon fibre; however, it came in only short lengths. There weren’t enough suppliers for their needs, so they turned elsewhere: its fibres were found to have a good balance of rigidity and weight. The first corporation decided that this lightweight yet strong type of fibre would be perfect for horizontal surfaces like tails. In contrast, the second contractor opted for using boron as both outer skin (flat) or rudder and vertical surface such as fuselage panels.
The use of Boron Fibers became history-making when these high-performance fibres first appeared in these production aircraft. Because of its’s ingenuity and function, General Bernard Schriever went on to call the production of continuous boron fibre the most significant breakthrough in materials in the last 3,000 years.
Application in Space Structures
A new application for boron fibre is used in space structure components for optical imaging. Boron, the only thread with a positive coefficient of thermal expansion (CTE), has been hybridised with high-modulus graphite fibres to produce composite structures that have zero CTE and stiffness as high as 56 Msi.
This was accomplished by working closely with L3Harris this past year on developing towpregs made from 4 mil thick monofilaments of it’s using cyanate ester polymers. With this towpreg, L3Harris and Aurora Flight Sciences were able to fabricate high-value satellite components resulting in manufacturing cost reductions of 30% or more. The wider use of AFP will increase the design flexibility and performance of these materials.
Boron Nitride: The future of Aerospace?
Boron nitride (BN) is a ceramic material that was first developed for use in high-temperature applications. Boron Nitride powders were the first synthesised by the decomposition of boric acid at 1500°C and higher, yielding mixtures with nitrogen concentrations between 60% to 95%. The properties of BN depend on the composition and production conditions such as temperature, pressure, atmosphere or fluxing agents used during synthesis.
Boron nitride is a compound that features two distinct components. It combines boron and nitrogen, which are both elements with an atomic number of 5 or less on the periodic table. You may have seen this material in white powder form at your local hardware store, as it’s used for polishing metal surfaces to remove scratches and make them shiny again.
In recent years, scientists created thin sheets of graphene by using direct-exfoliation techniques where they peeled off layers one atom thick from graphite flakes like peeling skin from apples! These sheets can be much more durable than other materials such as copper siding because their particles bind together so tightly due to strong chemical bonds between its carbon molecules.
There are various methods available to process Boron Nitride powder into shapes, including hot pressing or injection moulding. Boron Nitride can be processed either wet or dry from powdered form. Powdered forms have better thermal conductivity than solid bodies, making them applicable for heat dissipation in electronic components. Boron Nitride also has a high dielectric constant, making it an excellent choice for circuit boards that require insulation between circuits and is perfect for use as insulators.
In addition to these properties, Boron Nitride ceramics are strong enough to withstand extreme temperatures up to 2000°C (3632 °F), they display a low thermal expansion coefficient which makes them perfect for heat sinks, and long-term durability means they can be reused over and over again without breaking down or shedding material into the environment!
Potential Applications in Aerospace Industry
New grades of boron nitride are now available in large sizes in production quantities? Hot-pressed Boron Nitride is being made into a controlled chemical composition that can be produced in large quantities.
Further, grades of hot-pressed boron nitride, available from Union Carbide Corporation’s Carbon Products Division research, have been heralded as a “breakthrough” by material experts. One grade has already gained wide acceptance for its superior performance when used for insulators, spacers and containing channels in plasma arc heaters.
One should note that another new grade of Boron nitride has outstanding resistance to moisture pickup and improved high-temperature properties. The more data we collect, the better understanding designers have on how it can be used in future applications–from home appliances like furnaces or dishwashers to electronics for things such as circuit boards.
These applications’ versatility only points to the potential usage of new grades of Boron Nitride in aircraft and spaceships of the future. Because of their untapped potential, governments worldwide are conducting extensive research on new grades of Boron Carbide to get ahead and improve upon their existing technology.
Takeaways
Boron and its chemical compounds can provide much-needed solutions and serve as alternatives to our existing equipment. Better equipment allows for increased fuel efficiency, better aerodynamics, and improved cost optimisation. Similarly, the use of that in the military is set to boom even further in the coming years as military bodies across the world are developing better armour that can save thousands of lives on the battlefield.
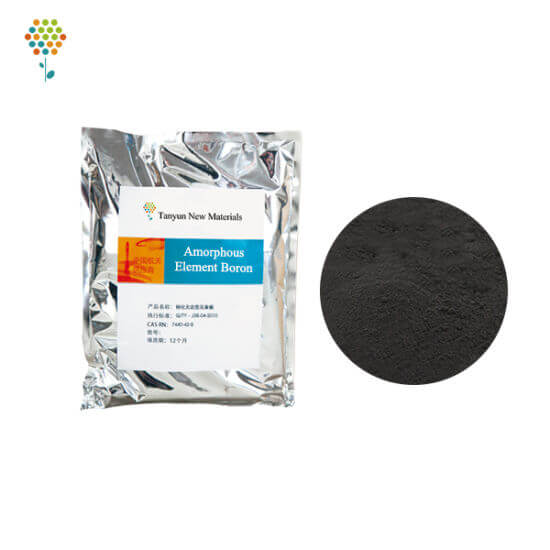