Boron in Traction Motors
Boron in traction motors – Smarter, better, cheaper, faster — is the mantra of today’s global economy. As organizations seek to streamline operations and do more with less, they increasingly focus on advanced logistics vehicles and mobile robots to help get the job done. From smart warehousing in retail to materials handling in manufacturing to telepresence robots in healthcare, robotic vehicles constitute a fast-growing technology sector.
Indeed, by 2022, analysts expect the global market for automated guided vehicles (AGVs), alone to reach $2.65 billion(1). OEMs will need electric traction and steering technologies and products that perform unquestionably to meet demand. Those assemblies also must be rugged, economical, and easy to install, operate, and maintain. Electric traction and steering solutions deliver on all counts.
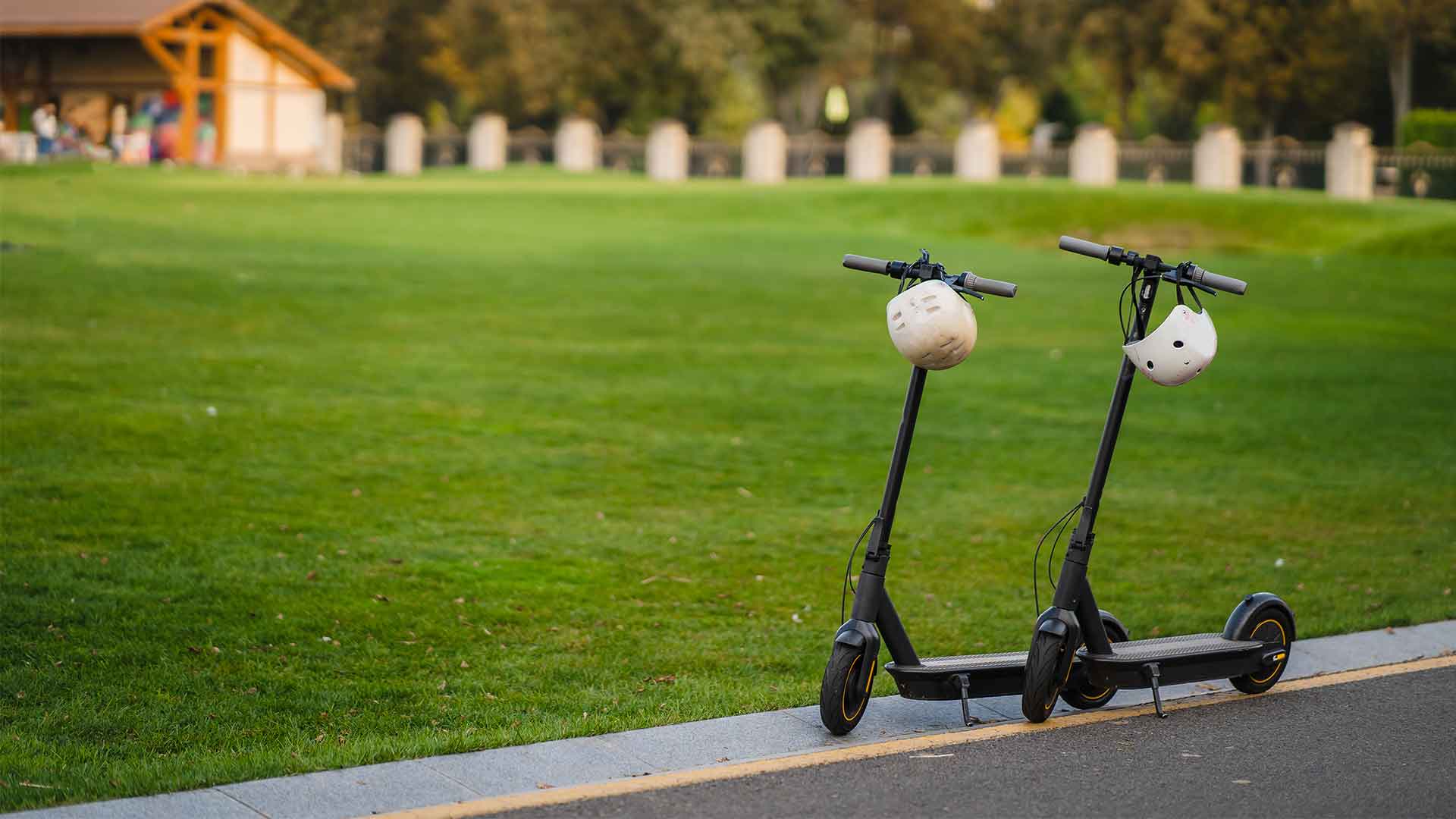
Boron in Traction Motors
Boron in traction motors is a new area where significant progress is being made. Traction and steering solutions can be divided into two classes: electrical and hydraulic. We won’t cover hydraulic-based solutions here, except to acknowledge the use of electric motors to drive pumps in electrohydraulic applications. Electric steering and traction solutions are cleaner than their hydraulic counterparts and comparatively more efficient.
Electrical traction motors are powered by electricity and generate the power to rotate the wheels of heavy vehicles and other transport machines like trains. The turning force produced by traction motors is transmitted to the wheels via the driving gear unit and axle. Traction motors are typically mounted in the trucks where the wheels are housed. Features include:-
Low maintenance: Completely sealed structure prevents dust intrusion. Reduced number of components for fewer items requiring maintenance and reduced frequency.
Low noise: Completely sealed structure to keep noise at a minimum. Improved accessory devices such as cooling fans also help keep noise levels low.
High reliability: Robust structure achieved by integrating the stator and brazing the rotor bar using high-frequency heating.
Permanent Magnet Traction Motors Use Boron
PM traction motors use boron-based neodymium iron boron (NdFeB) permanent magnets in the rotor, which spin the rotor in response to a rotating magnetic field produced in the stator. According to Adamas, PM traction motors can provide up to 15 per cent more efficient than induction motors, and are the most power-dense type of traction motor available.
“Looking ahead, we expect demand for PM traction motors, and the boron rare earth magnets they contain, to continue on a path of explosive growth as EV demand soars and the sales-weighted average motor power (kW) per EV continues to rise,” stated Adamas.
Traction Motors In Robotics
Service robot deployments are increasing, but industrial and logistics applications dominate today’s automated vehicle market. The types of vehicles in widespread use include warehouse and factory-floor trucks, hoists, pushers, tuggers, and various types of mobile robots. They move unit loads from point to point, put items on and off shelves, fill pallets, load and unload trucks and assist humans in doing their work. They are operated under a variety of environmental conditions, including extreme heat and cold; dirt, dust, and moisture; and more.
Electrically driven vehicles can be quite competitive with hydraulic versions. Typical electrically driven AGVs can handle loads of up to 20,000 pounds, for example. They are normally battery powered and can be programmed to automatically return to their charging stations when required. They are clean, quiet, and more precise than hydraulic solutions.
This combination of characteristics makes electric actuators appealing for a wide range of industrial and service vehicle applications.
Motors Used In Drones
The selection of a drone motor for a particular drone propulsion system will depend on many factors, particularly the weight of the drone. A drone motor needs to be able to generate enough thrust to counteract the weight of the drone and enable it to achieve liftoff.
The torque of a UAV motor represents its ability to change from one speed to another. Higher torque value motors are required for larger propellers and will draw more current than lower-torque motors.
Generally speaking, brushed motors are used in the smallest drones, whereas larger drones and UAVs will use brushless motors, as they can carry the extra weight of the additional electronics. Brushless drone motors also require an electronic speed controller (ESC) to operate. The chosen motors are usually electric motors, DC motors, permanent magnet motors or drone servo motors.
Looking Ahead – Coming to your Streets soon!
As scooter technology develops and they become more ubiquitous on our roads, we can watch as they speed by driven by technologies that include boron-assisted neodymium magnets to harness the necessary green power to keep the machines going forward.