Boron has been proven to be an excellent lubricant for engine components. University of Utah researchers found that parts coated with boron had 50% less friction than others. This may result in significant fuel savings and increased engine durability. Boron should become an essential ingredient in fuilds, fuels and engine technology once its potential benefits are further clarified.
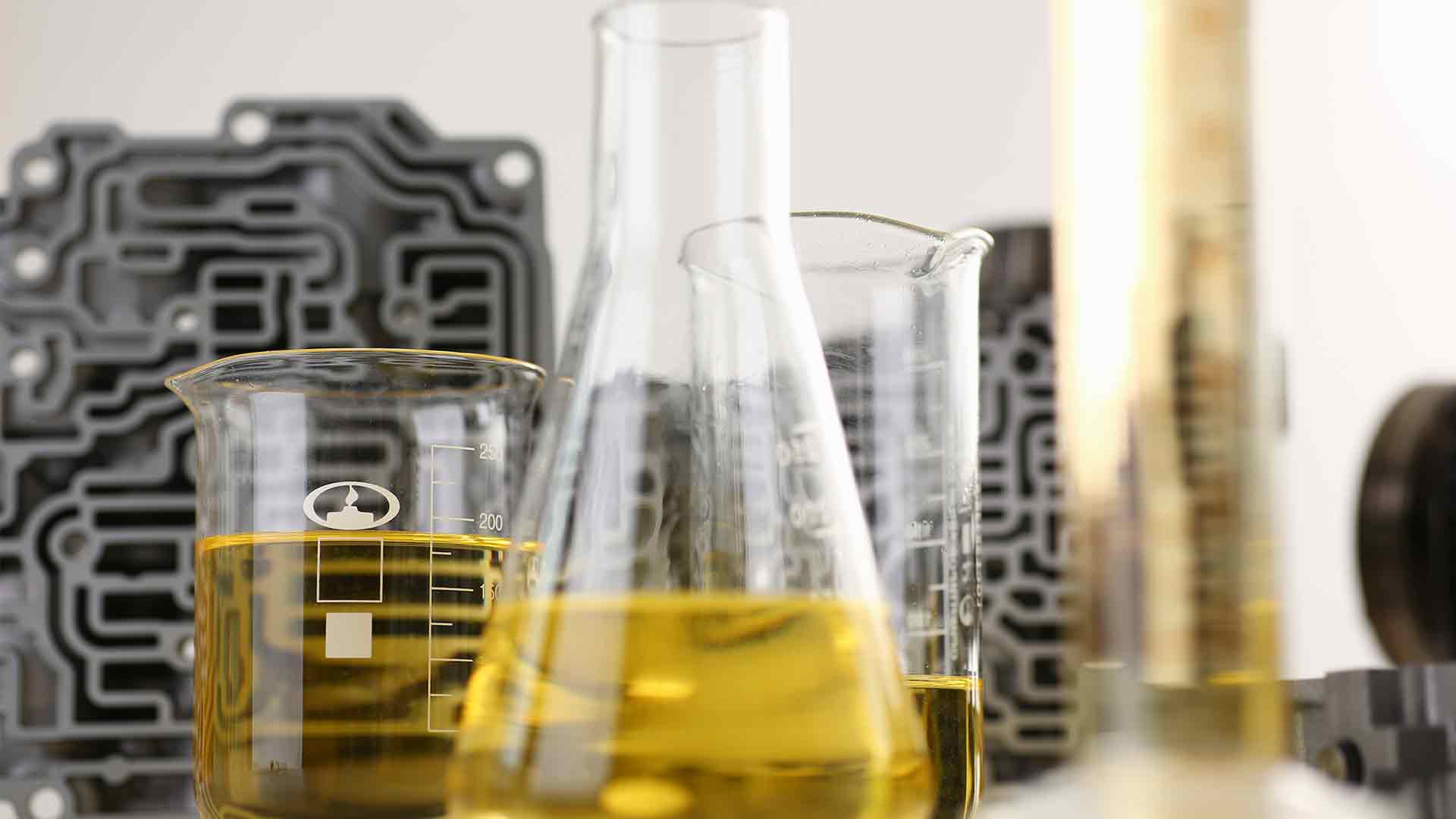
Boron Fuel Additives
Benefits of Boron as a Fuel Additive
An excellent example of boron applications in fuels and fluids is manufacturing industrial and automotive fluids, such as lubricants, hydraulic fluids, water treatment chemicals, closed system heat exchanger fluids, antifreeze, brake fluid, fuel additives, and metalworking fluids.
Among the numerous benefits, boron imparts to these fluids are the following:
- Lubrication
- Corrosion inhibition
- Buffering action
- Freezing-point reduction
- Boiling-point elevation
- Stabilization of thermal oxidation
- Prevention of sludge formation
- Reduction in moisture sensitivity
The addition of boron to gasoline increases engine performance, improves battery performance, reduces emissions, improves engine efficiency, and reduces fuel consumption. The gasoline engine’s performance is at its best with boron additives, and emissions are significantly reduced. The use of boron also results in a decrease in CO₂ emissions.
Diesel engines can benefit significantly from adding boric acid or borate salts to improve the combustion process and, consequently, reduce the number of nitrogen oxides (NOx) emitted by the exhaust.
Boron also improves the flow characteristics of fuels by lowering their viscosity. Reducing corrosion caused by acidic gases also enhances engine performance.
Boron is a light, challenging element that possesses metallic and non-metallic properties. It is hence classified as a metalloid element. Boron reacts readily with many elements and forms covalently bonded organic/inorganic compounds as a chemical element. Ionic and metallic bonding is also possible with a wide range of metal borides and borates.
A popular solid lubricant in metal forming operations involving high temperatures, h-BN is highly recognized for its slippery properties in the lubrication industry. The lamellar boron compound boric acid (H₃BO₃) can reduce friction and wear in many tribological applications. Other boron compounds (especially borate esters) were synthesized and used as lubricants in the past.
Lubricating oil that contains boron-doped elements changes NOx emissions. Furthermore, boron additives improve exhaust gas quality by reducing hydrocarbons and carbon monoxide. It is possible to increase the combustion temperature up to 1000 degrees Celsius.
The Science Behind Boron Fuel Additives
A great deal of chemistry has been studied about organoboron compounds, and several have been tested for pressure and corrosion resistance properties in oils and greases. The general characteristics of solid lubricants H-BN and H₃BO₃ are discussed below, followed by types of boron-based nano lubricant. The lubricity of boric acid as a micro-and colloidal additive in oils is a topic of interest to researchers. Also, boron-doping in the lubricating oil can reduce NOX emissions.
Boron-based lubricants: general characteristics of H₃BO₃ and H-BN
Hexagonal boron nitride is a well-known solid lubricant and is used by industry for various applications. Its structure is similar to graphite, but unlike graphite, it is white (hence, occasionally referred to as “white graphite”). Its atomic layers are made of two-dimensional arrays of strongly (covalently) bonded boron and nitrogen atoms.
As in graphite, bonding between the atomic layers is van der Waals type and, hence, relatively weak. In tribological testing, these layers slide over one another and thus provide low friction. When tested in the open air, the friction coefficient of h-BN is 0.2-0.3.
Boron has also been tested as a micro colloidal additive in oils and greases, and at concentrations of 1 wt.% or more, it shows excellent wear resistance. Despite the recent production of h-BN nanotubes, sheets, and nano-powders, there has not been much experimental work on the lubrication behaviour of nano-h-BN dispersed in oils or greases. However, there are studies into the tribological behaviour of nano-h-BN structures and their potential as colloidal nano-lubricant additives.
H₃BO₃ is also a solid organic lubricant made of boron. Mineralogy textbooks call it “sassolite.” The strongly bonded sheets are boron, hydrogen, and oxygen atoms, just like h-BN. Boric acid exists in two primary forms: Metaboric acid (H₂O•B₂O₃ or HBO₂) and orthoboric acid (3H₂O•B₂O₃ or H₃BO₃). The most common form of orthoboric acid is formed by the hydration of boric oxide (B₂O₃).
There are three types of metaboric acid: orthorhombic or α-metaboric acid, monoclinic or ß metaboric acid, and cubic or γ-metaboric acid. While all of these boric acid types exhibit layered crystal structures, orthoboric and orthorhombic metaboric acids are by far the most common. Scientists are particularly interested in evaluating these major boron compounds for friction and wear properties.
Boric Acid and its Derivatives
H₃BO₃ and ????-HBO₂, as noted above, possess self-lubricating properties as a result of their layered-crystal structures. Consequently, they can have very low friction and wear coefficients when sliding tribological interfaces.
For example, atomic sheets of H₃BO₃ can align parallel to the direction of relative motion and then slide over one another with relative ease to provide a low friction coefficient. According to previous studies, the presence of multiple bond-forming capabilities (i.e., ionic, covalent, hydrogen, and van der Waals) enables boric acid to adhere firmly to sliding surfaces of metallic and ceramic materials.
Boric acid particles dispersed in base oils perform well in lubrication. The friction coefficient is measured with a pin-on-disk machine, consisting of a stationary steel pin that rubs against a rotating steel disk or flat. Pins are either flat or hemispherically tipped (the pins typically have a radius of 127 mm on one face).
As the pins rub against the disk surface, lubricants are applied to the disk surface. A load is applied to the pin using dead weights. 20 N loads were used for the specific tests conducted, and linear velocities were adjusted to 0.01 and 0.1 m/s. The tests were carried out at room temperature and in open-air, with relative humidity ranging from 30% to 60%.
The friction coefficient for sliding steel surfaces is 0.15 when base PAO is used. In contrast, when PAO is blended with one wt.% nanoparticle boric acid (NBA), the friction coefficient is reduced to 0.05. As the sliding speed is diminished toward the end of the test, the friction coefficient is decreased further, possibly due to the formation of a slick boron-rich boundary film. In terms of mechanism, solid boric acid nanoparticles are transported by liquid oil to the vicinity of the contact zone and then dragged into the contact interface during sliding contact.
These molecules are deposited as thin (a few nanometers thick) boundary films on rubbing surfaces within the contact zone. As a result of their sheer properties, boundary films can protect sliding surfaces from wear and reduce friction.
To enhance these sliding surfaces’ anti-friction and anti-wear properties, the molecules in these nanoparticles might rearrange themselves into a plate-like boric acid structure. In addition to providing protection, boron-rich boundary films can also reduce wear and tear.
Final Thoughts
The research provides ample evidence that boron compounds can provide higher lubrication and protective benefits in fuel additives and fluids in general.