Underground Mining For Hard Rock
Underground mining is most commonly done in pursuit of metals, gems, and other valuable resources. Hard rock mining is the practice of extracting minerals from hard ore or sedimentary rocks rather than softer ones such as oil or coal. It involves using a variety of sophisticated technologies to break through solid rock faces in order to access these resources deep underground.
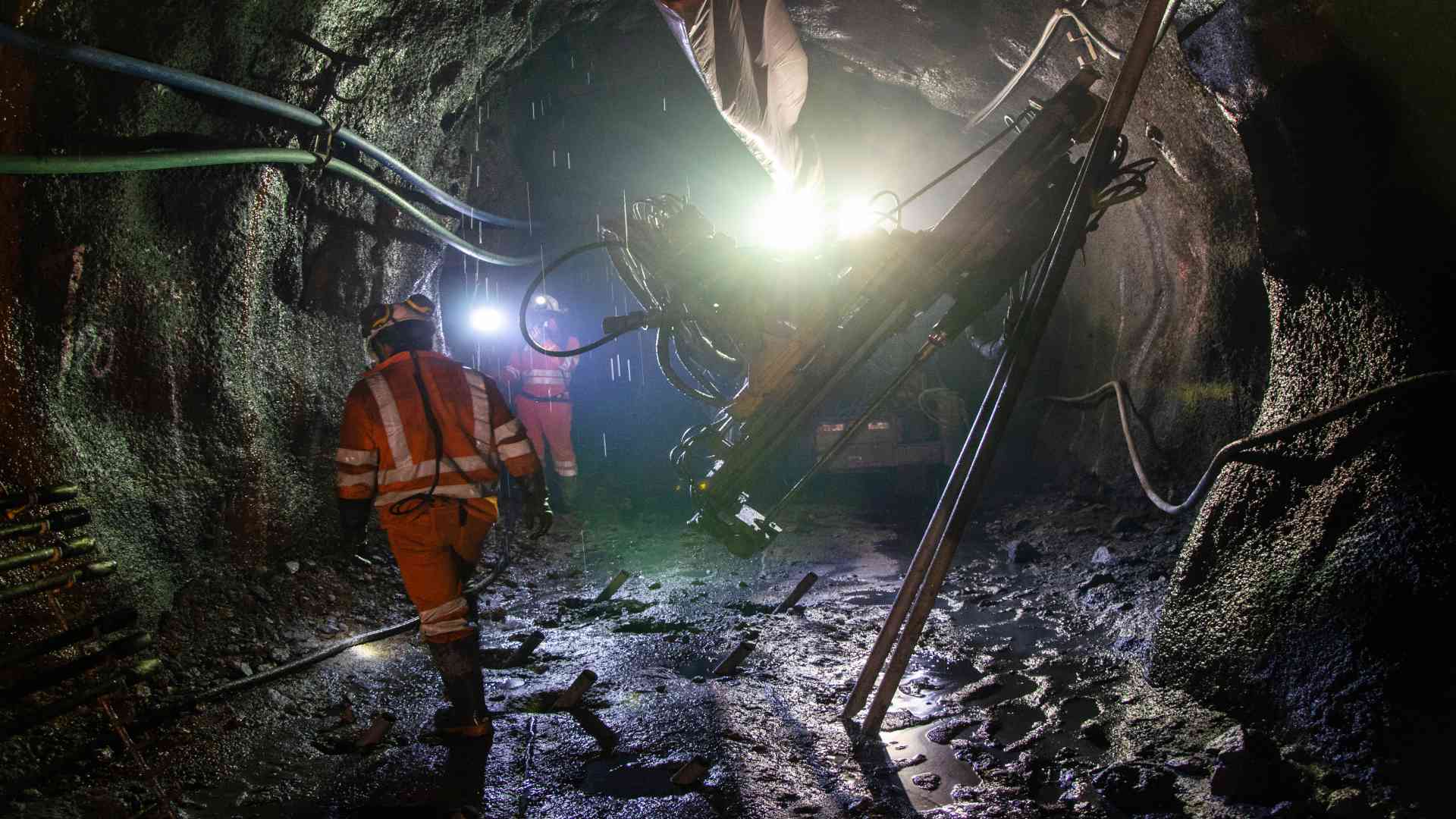
Underground Mining
Hard Rock Mining Process
Hard rock mining is an incredibly important and complex process that involves various techniques in order to safely extract valuable minerals from hard rocks. It has been used for centuries to mine silver, gold, iron, zinc, copper, lead, tin, and nickel-containing ore bodies which help to provide essential materials for the world’s economies.
Recently it has also evolved to include large ore bodies containing gems such as rubies and diamonds. This requires advanced mining methods that are much more precise than traditional methods of mining due to their intricate nature.
The goal is always to ensure maximum safety while adequately extracting these precious stones or metals from the ground without doing significant damage to the environment or surrounding properties.
There are three steps for hard rock mining.
1. Exploration
This involves locating and evaluating a suitable ore deposit using surveys, remote sensing, and drilling.
Surveys aid in identifying conditions that may confirm the existence of an extractable mineral deposit. A desktop survey examines aerial photographs, geologic and geophysical maps, and published reports, while a site survey shows a stream, sediment, and rock sampling.
Remote sensing is another valuable form of site survey. Most naturally found materials acquire specific wavelengths of sunlight. Each mineral has a distinct spectral signature due to its chemical composition, particle size, degree of crystallinity, and formation temperature. The spectral signature of reflected sunlight measures how it interacts with a surface. Aircraft or satellite systems can collect spectral data over large areas and thus identify possible ore deposit locations.
Drilling is usually done when geologic conditions are favorable, and surface sampling confirms the presence of an ore body. Drilling is used to collect ore body core samples at different depths for inspection and assessment. If any further exploration of the deposit is required, drilling is used to define the deposit’s boundaries and the size and grade of the ore. Based on a small number of samples, sophisticated statistical techniques are used to indicate the attributes of ore bodies.
Seismic surveys – The process of conducting a seismic survey begins with the placement of electronic receivers, known as geophones, in strategic locations. These receivers measure the shock waves’ speed produced by small explosions detonated at or near the surface. The data collected by the geophones are used to determine the time it takes for shock waves to reflect from varying points between various geological formations. This information can then be used to identify the presence of certain geologic formations of interest.
Although indirectly related to exploration, the following activities are essential in understanding a mining operation:
- Access and haul roads, rail lines, barge terminals, and utilities are part of the site development process.
- Mining facility construction includes designing shafts, support buildings, and housing facilities.
- Development of beneficiation facilities such as pipelines, conveyance systems, leach pads (if required), processing ponds, and a mill (if required).
2. Extraction
It is the process of removing ore deposits from the ground. Surface mining and underground mining are the two main types of extraction.
Surface Mining
The most common type of hard rock mining used today is surface mining. It includes digging to extract ore from the ground. Surface mining is less expensive than underground mining due to lower machinery and maintenance costs. Surface mining begins with the following steps:
- The first step is overburden removal, which removes the waste rock that lies above the ore deposit. The amount of mining waste that must be removed fluctuates but is frequently enormous. Gangue materials are the less valuable materials typically associated with more valuable ore deposits.
- The next step is blasting, which involves detonating high explosives to break up the ore and waste rock.
- Once the ore has been blasted, it must be mucked – this is the process of removing and transporting it from the blast site using heavy machinery.
- After mucking, the ore goes through primary crushing. This reduces the material size to be transported to the mill.
- The ore is then moved from the mine to the mill using trucks, rail cars, or conveyors, a process known as hauling.
The two primary forms of surface mining are open-pit and strip mining:
- Open-pit mining is the most popular type of surface mining. It includes a concentrated excavation of the land and can differ in size from a small, superficial site to a large pit more than 1000 feet deep and covering several square miles. Topography, the size and location of the ore deposit, the mineralization of the ore, and other factors all influence the final structure of an open-pit mine.
- Strip mining is a type of surface mining used to extract ore deposits that are horizontal and near the surface. This type of mining moves linearly and can cause long-term disruptions to the landscape.
Underground Mining
Underground mining is a technique used to mine valuable minerals and ore deposits that are located beneath the surface of the Earth. The techniques employed in this form of mining can be broken down into three main classes: unsupported, supported, and caving methods.
The choice of method often depends upon the competency or stability of both the orebody and host rock. Unsupported techniques include cut-and-fill stoping, where ore is removed from top to bottom within a stull or open space while caving methods involve working downwards by allowing rocks above an excavation site to collapse under their own weight.
Supported underground mining involves taking advantage of natural geological structures such as faults and fractures that create support pillars that can be left intact when removing access tunnels through surrounding rock masses.
Underground mining becomes necessary when either stripping ratios become uneconomical or because surface use would be prohibited for legal reasons (such as protecting important natural resources). Specific considerations must also be made in underground mines for health, safety, and ventilation purposes due to limited visibility and large amounts of dust generated during operations.
In conclusion, underground mining is an essential method for extracting valuable resources whilst maintaining respect for important laws and regulations regarding land use restrictions reducing any risk associated with extraction activities at highly regulated sites such as national parks or industrial sites near residential areas.
3. Beneficiation
Beneficiation involves separating the desired mineral from waste rock in ore. Almost all crude ore should be decreased in size before beneficiation. Primary crushing lowers ore from 2-4 foot boulders to 8-10 inches in diameter. Secondary crushing lowers the ore to pieces no larger than one inch in diameter. Large rotating cylinders compress the material into a fine powder. When water gets to the finely ground mill, the slurry is formed.
Beneficiation is of various types, including
- Gravity separation – It is based on large density differences between the target metal (for example, gold) and the substances in which it is discovered. It is also necessary for the target metal to be unbound from the surrounding rock matrix. Trommels, sluices, spiral concentrators, cyclones, jigs, and shaker tables are some examples of gravity separation equipment.
- Flotation – A method of recovering lead, copper, platinum, and zinc suitable for small particles. The addition of a reagent chemical to ore slurry induces the minerals to be less dense than the gangue and rise to the tank’s surface during floatation.
- Leaching – The method of extracting a dissolved metallic compound from ore is leaching. It includes dissolving the ore in a suitable solvent, including sulfuric acid or sodium cyanide solution.
Hard Rock Mining of Boron
Hard rock mining has immediate environmental results on surface vegetation and other wildlife. The world’s two largest boron producers, Eti Maden (Turkey) and Rio Tinto (California, USA), operate hard rock mines that are highly asset-intensive.
When it comes to capital intensity, it is believed that 60% – 70% of capital utilized in a mining project is committed to mining-related activities, with the remaining 30% – 40% in successive concentrate processing steps; the ratio linked with in-situ leach mining (solution mining) more closely resembled 20% -30 % of capital utilized into mining-related activities, with the remaining in related concentrate process.
According to Davidson’s report, an equivalent hard rock mining at Fort Cady designed to target 500sTPY of boric acid equivalent output will require 2 to 3 times the capital that is predicted to be used to build 5E’s targeted in-situ operation.
They believe that the capital investments and operating costs of hard-rock mining are considerably higher than those required for 5E advanced material’s (FEAM) solution mining operation. Moreover, hard rock mining operations generate tailings, which must be managed and maintained properly, incurring additional costs. FEAM’s in-situ process does not generate any waste product, making it a more efficient and cost-effective option.