Volvo Cars are now Built with Boron for Extra Strength and Safety
Volvo cars are renowned for their promise of safe, secure results, and boron is a key contributor to meeting this expectation. It’s an alloy in carbon steel that reinforces the weakest areas in Volvo cars, providing further peace of mind when driving them. Popular models such as the S90 sedan or XC90 mid-size SUV have seen great success on Indian roads thanks to these safety features, offering drivers assurance no matter where they go.
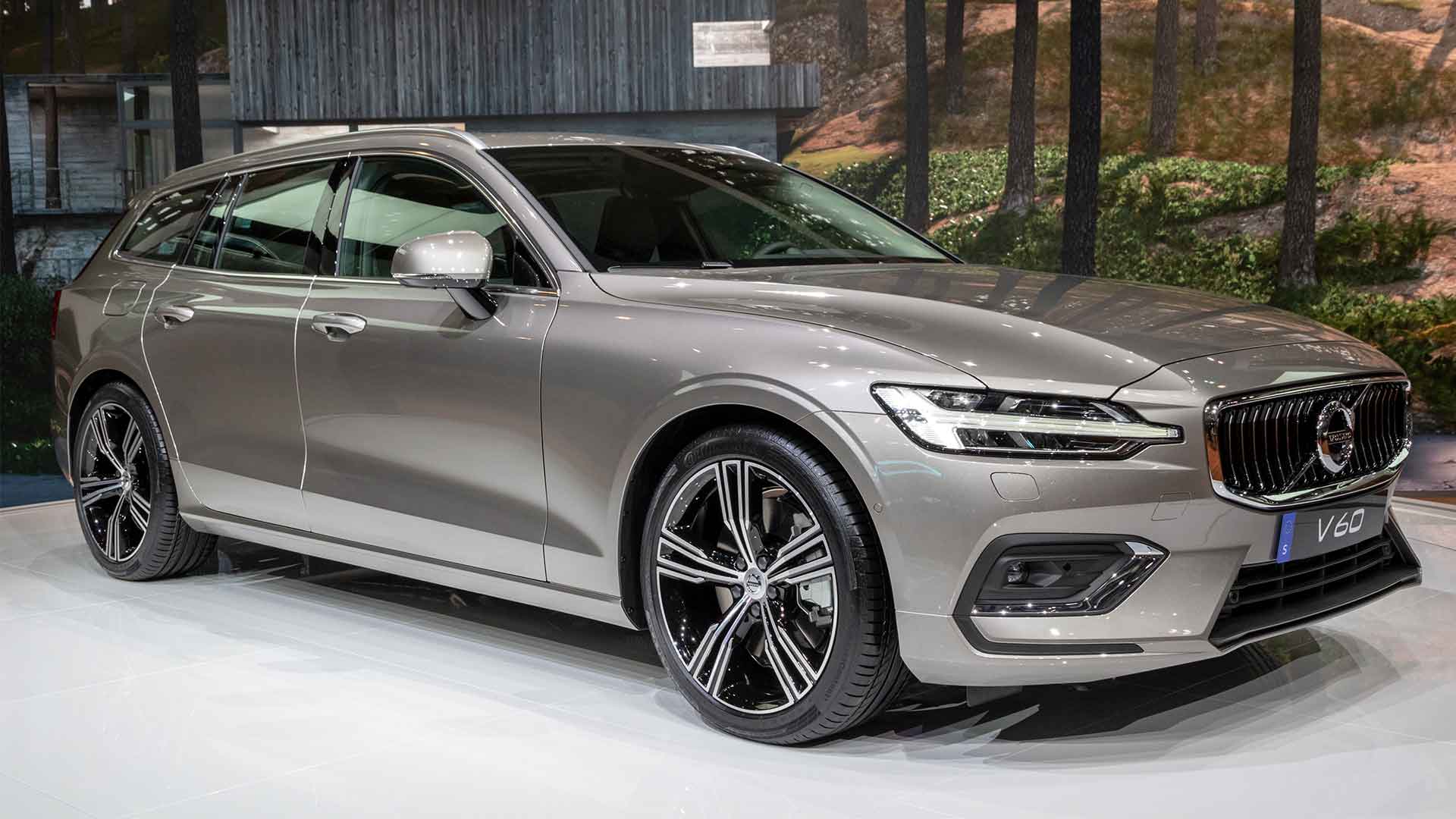
Boron used extensively in the Automotive industry
Boron is helpful as an alloying element in many materials in the automotive industry. Boron Steel has attained a point of about 1,350 – 1,400 N/mm2., Therefore, the item is about four times stronger than average high-strength steel. However, here it will be illustrated as an alloying element in the innovative technology of steel since the effect on solid structural enhancement. The element Boron is added to unalloyed and low alloyed steels to enhance hardness by enhancing hardenability. For example, Boron added to high-speed-cut steels having 18% W, 4% Cr, and 1% V helps to improve containing 18%W, 4%Cr, and 1%V enhancing their cutting performance but reducing their forging qualities.
Adding Boron in a considerable quantity of up to 0.01% to austenitic steels also improves their high-temperature strength. Boron steels are used as high-quality, heat-treatable constructional steels for carburization and cold-forming steels such as steels for screws. Adding 5 to 50 ppm B to ferritic steels improves the surface quality of stainless strips by avoiding errors, such as scale, ribbing roping, and ridging, which otherwise frequently occur in strip production. The ferritic steel contains containing 14% to 18% Cr to help in strengthening its assemble.
The primary effect of Boron on the steel is the enhancement of hardenability, which is evident already at a minimal concentration, at 0.0010% of Boron. Even in a few quantities of the degree in size up to 100 ppm, Boron gives the exact effect of the extended ability in strength enhancement as other more expensive elements, which provides a much larger quantity. Let’s consider the addition of 30 ppm B in SAE , replaces approximately 1% of Ni, 0,5% of C, 0,2% of Mn, 0,12% of V, 0,3%of Mo or 0,4% of Cr.
Automotive manufacturers have taken advantage of these tensile strengths provided by Boron with greater car body stiffness and lower body weight for safety. Another benefit is lighter chassis to address fuel efficiency with new vehicle legislation and increased fuel prices. Material development, engineering, and manufacturing departments have been working together to achieve these goals. Advanced steels, new forming processes, and new press concepts have been adopted to achieve weight reduction with improved crashworthiness.
The core advantage of Volvo cars to the user experience of including Boron to the steel is the exceptional rigidity to the body, where the micro-level of improvement matters to the company for a better user experience of their service. Provided by the type of steel and carbon content, Boron can be as micro as 3ppm to make the difference in rigidity and quality finish. Other substances can be added to steel to alter its characteristics; however, using Boron over other elements can improve steel properties at relatively low tempering temperatures, helping to reduce energy costs. Another benefit of Boron is better machinability compared with steels with similar hardness.
These properties mean that boron-containing carbon steels are used where the base steel meets most properties, such as wear resistance, but the rigidity is too low. In this case, Boron is a less expensive option than using a different alloy—one of the primary uses for boron steel in the automobile industry, particularly within first-world countries. Safety bars, inner pillars, and dash panels have used boron-containing steel.
The Volvo Group
Recently, the Volvo group has collaborated with SSAB, the first to produce fossil-free Volvo cars globally, doing a significant favour to this ecosystem. The multi-functional machine is a carrier for mining and quarrying purposes for the user.
According to the President and CEO of SSAB, “having the world’s first actual vehicle made using SSAB’s fossil-free steel is a true milestone. Our collaboration with Volvo Group shows that green transition is possible and brings results”,
“Together, we will continue reducing climate impact to the end customer while ensuring that our customer gets high-quality steel. We look forward to working with Volvo Group in research and development to produce more fossil-free steel products.”
“This initiative of Volvo group with SSAB sets the benchmark for a fossil-free future. Just as the world’s nations come together at COP26 to address climate change, many organizations and industries collaborate to develop innovative new solutions for a greenhouse gas emission-free future. Volvo Group is committed to pioneering partnerships such as this with SSAB to create attractive, safe, and efficient new vehicles and machines that pave the way for a mode of more sustainable transport and infrastructure system adopted for the future, “improve.
Increase in Demand for Boron Steel in Automotive Industry
In recent years, there has been an increase in demand for automotive parts containing Boron steel due to the increasing use of hybrid or electric vehicles. This trend is expected to grow further because of the growing awareness of environmental issues. According to the report published by IHS Markit, the global car battery market was valued at $11 billion in 2017, which is projected to reach $20 billion by 2025.
Moreover, according to the International Energy Agency, the share of electrified passenger vehicles worldwide increased from 1% in 2010 to 15% in 2018. As per the forecast, it is estimated that around 50 million EVs would be sold annually by 2030. Thus, the growth rate of EV sales could accelerate up to 20 times during 2020–30.
Accordingly, the production of batteries for these vehicles requires higher amounts of raw materials like nickel, cobalt, lithium, etc., which are sourced mainly from China. However, the supply chain of these metals is highly vulnerable to geopolitical risks. Hence, the need for alternative sources of raw materials becomes essential. The demand for Boron steel is increasing significantly in order to meet the requirement of multiple auto manufacturing.