The Role of Boron in Nickel Plating
Nickel Plating is a reliable method of decorating, protecting against corrosion, and reducing stress while also increasing wear resistance and lubrication on the substrate. Nickel boron plating (NiB coating) is a well-known nickel depositing technique. NiB coatings are utilized for multiple purposes including protection against corrosion, reducing stress levels on surfaces being treated, and increasing wear resistance while maximizing lubricity which contributes towards augmenting functionality yet preserving aesthetics.
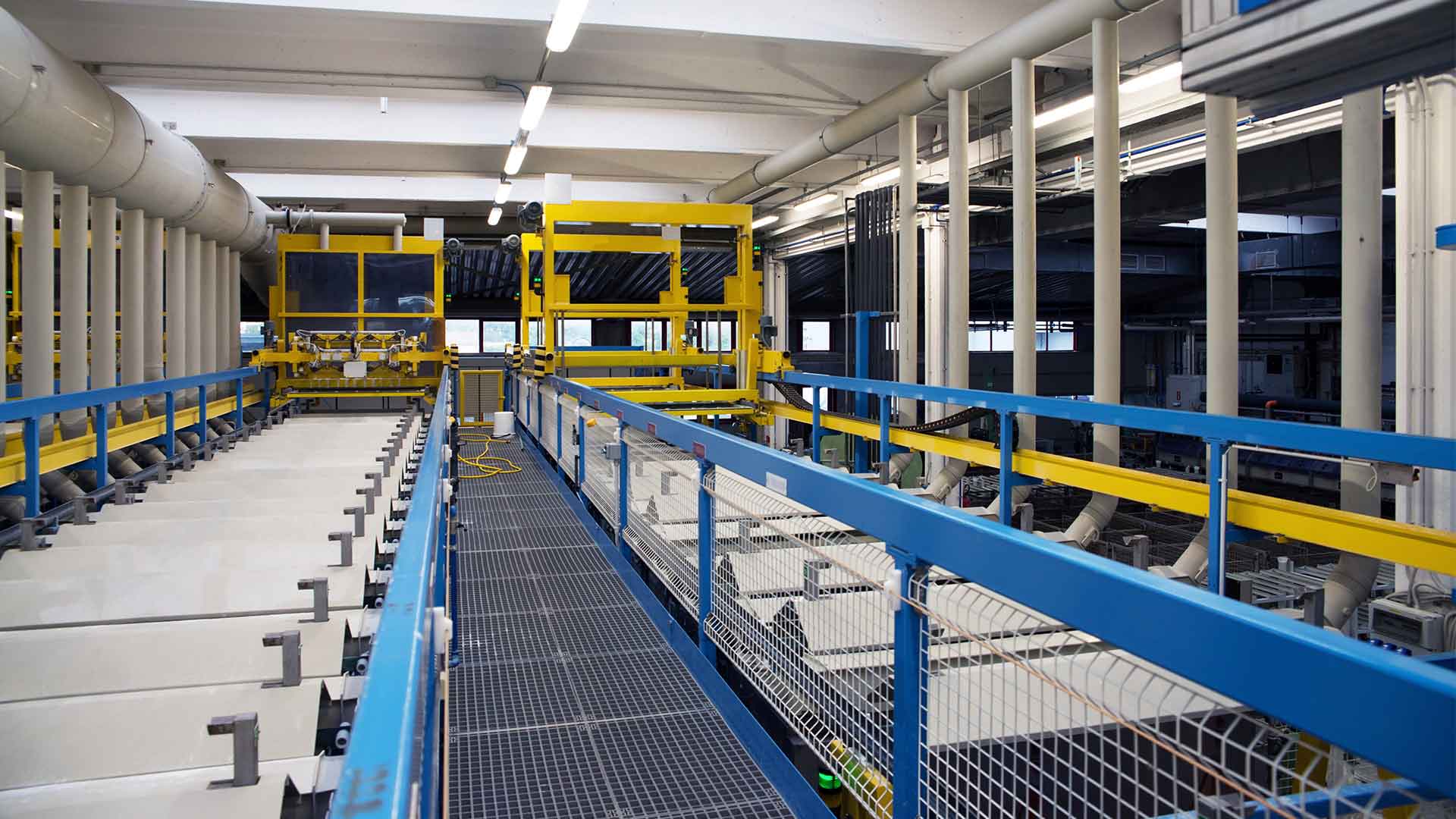
Nickel Plating
Discovery of Electroless Nickel Boron Plating
Electroless nickel-boron plating was developed in a variant of the nickel-phosphorus process. Charles Adolphe Wurtz accidentally discovered it in 1844. In 1969, Harold Edward Bellis from DuPont filed a patent for a general class of electroless plating processes using sodium borohydride, dimethylamine borane, or sodium hypophosphite in the presence of thallium salts, thus producing a metal-thallium-boron or metal-thallium-phosphorus; where the metal could be either nickel or cobalt.
According to the patent, the boron and phosphorus content could vary from 0.1 to 12 percent, while that could range from 0.5 to 6 percent. The coatings were described as “an intimate dispersion tri nickel Boride (Ni3B), or Nickel phosphide(Ni3P), in a soft matrix made of nickel and thallium”. (Charles Edward McComas patented several different versions of this process over the years).
Bellis’s formulation was modified by adding more potent -chelating agents (“Generation 1”. A method for applying nickel-thallium-boron to titanium without fatiguing the titanium substrate was also developed and commercialized; by Purecoat International under the brand “NiBRON.”
In 1986, McComas patented an improved formulation (“Generation 2”) for nickel-cobalt-thallium-boron coating, which further increased the stability and repeatability of the process. According to the patent, the coating was composed of hard, amorphous nodules with high nickel content dispersed in or rooted within a soft alloy of high cobalt. “
McComas created another formulation in 1994 (“Generation 3”), patented in 1998. This allowed for the replenishment of chemicals during plating making it a continuous process instead of a batch.McComas patented a further improvement in 2000 (“Generation 4”), using lead-tungstate instead of Thallium sulfate at pH 10 to 14. UCT Coatings sold this formulation under various brands, including FailZero, and Ultram.
How Electroless Nickel Boron Plating is Done?
Electroless plating requires the reduction of metal cations in solution by electrocatalytic reactions, which take place purely chemically. Electroless plating produces an even metal layer, regardless of the surface geometry. This is in contrast to electroplating, which suffers from uneven current densities because of the effects of substrate shape on its electric field. Electroless plating is also possible on non-conductive surfaces. Usually, the plating bath contains buffers, complexants, and other control chemicals.
The most commonly used nickel baths for plating are Watts baths. These use a combination of nickel sulfate, nickel chloride, and boric acid. Boric acid plays a vital role in establishing the upper limits of the applied current density.
A metal stabilizer is added to the nickel-boron bath before the electroless nickel-boron coating is applied in electroless nickel-boron plating. Usually, the stabilizer is a metal compound or salt. The amount of the metal stabilizer is 1%-5% of the weight of the coating. The final composition of the coating consists of between one to five percent boron and one to five percent metal stabilizer. The co-deposited nickel and boron are considered poly-alloy deposits of nickel and boron.
Application of Nickel Plating
Electroless nickel-boron plating, as can be surmised, is overwhelmingly for application to surfaces and hardware requiring durability, anti-corrosion, and self-lubrication. The potential and actual uses of electroless nickel boron coating include saw blades, ship propellers, downhole crude oil pumping equipment, firearms, and even semiconductors.
Saw Blades
Electroless nickel-boron plating (ENBP) is a non-electrolytic process that deposits nickel, nickel-boron, and nickel-phosphorus coatings directly on steel or stainless steel tools substrates and workpieces. The coating is applied to various substrates, including steel, stainless steel, and aluminum. The coating is typically used in thicknesses ranging from 0.03 to 0.08 mm (0.000 1 to 0.003).
The electroless nickel plating in saw blades combines the two metals, boron, and nickel. The former increases the blade’s corrosion resistance, and the latter increases its hardness. Moreover, it is less prone to breakage than the last. Therefore, the material is more pliable, ensuring a longer-lasting performance.
The electroless nickel plating effectively reduces drag in liquid and gas flows. These types of coatings also improve heat dissipation and minimize surface-surface contact. These characteristics make electroless nickel-boron a popular choice for saw blades. A typical example is when a saw blade needs to cut a hole in a piece of wood.
Ship Propellers
Electroless nickel-boron plating is used to protect ship parts and components from corrosion. The process is quick, safe, and efficient. Its modular structure prevents marine growth on a ship’s propeller. This nickel plating is used on applications, including stern and apron shafts. It is easy to apply and requires a low-temperature process. Its modular and columnar structure helps reduce friction, wear, and corrosion. Moreover, it is highly resistant to extreme temperatures, reducing heat build-up.
Electroless nickel plating also reduces drag and oxidation in gas and liquid flow. This material is highly corrosion-resistant and ideal for various ship components.
Electroless Nickel-Boron plating in Ship propellers is increasingly popular due to its many benefits. The process deposits a thin layer of nickel plating on a solid substrate without applying electrical power. This method usually begins by cleaning and degreasing the substrate, and surface activation may also be required. For example, grit blasting can be performed to remove rust and grease.
Crude Oil Pumping Equipment
Electroless nickel-boron plating is common in the oil and gas industry. It is an excellent choice for pumps and other equipment for its superb corrosion and high wear resistance.
The nickel plating process is critical to pumps, pipe fittings, and piping systems. Its properties make it ideal for various industrial applications, including packaging machinery. The benefits of electroless nickel plating are transparent, allowing companies to see immediate results. The environmentally safe process meets global coating specifications, making it an intelligent choice for various applications.
Electroless nickel-boron plating in Crude Oil Pumping Equipment is a low-cost solution. This plating offers long-term durability and does not require electricity. It is an environmentally-safe and economical alternative to chrome plating. However, this method does have some drawbacks. It is susceptible to out-of-tolerance parts and lacks mechanical and environmental protection. Compared to chrome plating, electroless nickel plating are more durable.
Firearms
For years, gun manufacturers who need to prevent product corrosion and have the dual benefits of a hard protective surface have used hard chrome plating for finishing. Chrome provides high resistance to corrosion and also protects against wear. But for those who seek even higher protection and anti-corrosion with self-lubricating properties, then Nickel boron is the standard.
Nickel boron is highly resistant to corrosion and wears firearms in extreme climates and conflict zones. Its low coefficient of friction allows the electroless nickel barrel treatment extensions to resist frictional heat build-up and protect barrels for a lifetime.
Nickel plating is especially prized in combination with a repeating barrel-loading firearm, notably the BCG or Bolt Carrier Group, most often found in gas-operated weapons, which manages the multiple functions of the weapon load and discharge in automatic firearms.
Regarding the AR-15 weapon, a firearm used all over the planet in military engagements, nickel boron offers a slight increase in surface durability. Still, most importantly, it is not sticky like a phosphate finish. It is more slippery, making cleaning easier, especially if not regularly cleaned.
Nickel Boron is preferred in a BCG for its slick, lubricated surface. Everything runs smoother when the critical characters of a bolt carrier system (inside-out) have a low coefficient for friction. Lubrication helps nickel plating friction reduction between the mating surfaces of the carrier, upper receiver, and cam pin. These areas can cause friction, leading to loss of carrier velocity and failure to feed, extract, or eject rounds properly.
Nickel Boron BCGs will remain slick regardless of whether the lube is evaporated, rubbed off, or burned off during shooting. This increases reliability when the rifle has been used less frequently or is not adequately lubricated. This is also true for suppressed guns and AR pistols.
In sum, nickel plating provides the following benefits for firearms:
- A high melting point (1,976 degrees Fahrenheit) protects against extreme heat
- Superior friction resistance
- Increased ductility
- Strong heat dissipation properties
- No risk of hydrogen embrittlement
- An eco-friendly alternative to hexavalent chromium
Semiconductors
In the semiconductor sector, the usage of Nickel Boron as a coating layer has been explored but, until recently, was considered insufficient due to a lack of research on its potential as a coating on printed circuit boards. However, a 2016 study by Hardinnawirda Kahar et al., Deposition of Electroless Nickel Boron as Printed Circuit Board Surface Finish, found that Nickel Boron can improve wear resistance due to superiors’ hardness and protective capabilities.
The study investigated the mechanical and physical properties of electroless Nickel Boron as a potential printed circuit board coating layer by soaking the material in a Nickel Boron plating bath solution with different concentrations of Sodium Borohydrate – (NaBH4), 0.4, 0.6,0.8,1.0 and 1.2 g/l. By measuring surface roughness and hardness, they found that the surface roughness and hardness resistance were positively affected by Sodium Borohydrate (NaBH4), which correlates with the surface microstructure.