Boron in Road Construction
Boron in Road Construction: Boron waste is discharged in the production of borax pentahydrate, borax decahydrate, anhydrous borax, and other compounds, with volumes increasing annually. But there is a solution. Given the right circumstances, boron waste can build a strong road base.
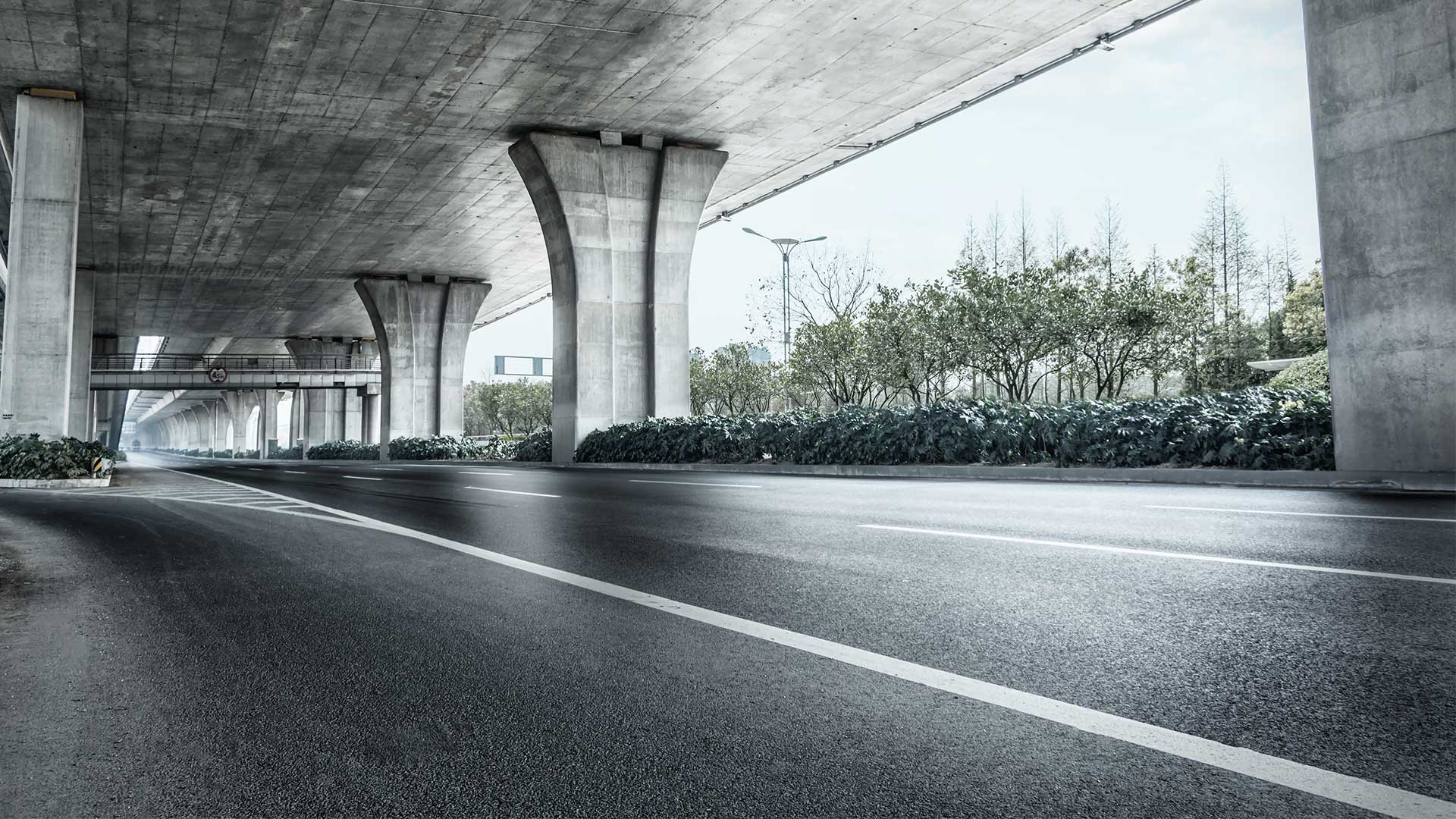
Boron in Road Construction
Making Good Use of Boron Waste
Boron waste is discharged in the production of borax pentahydrate, borax decahydrate, anhydrous borax, and other compounds. Its amount rises year after year. China has a 35 million ton reserve, but the emission rate is still 1.6 million tons annually. It is generally open-air and stacked close to the ore. Because the waste containing boron dioxide will pollute the groundwater and the earth, the harmful materials will also be transmitted to the groundwater resources.
Additional costs for disposal and storage are inevitable, but they will not be insignificant. It is necessary to allocate large areas for removal. Therefore, waste storage can lead to environmental pollution and economic loss. Recycling is a cost-saving and environmentally friendly means. It has been used in many countries as a building material.
Boron in Road Construction
A recent study found that boron waste could be an additive to road base material. Using boron waste for road bases can help reduce its environmental impact.
The waste mixture can be stabilized using lime and cement. Experimental methods were used to evaluate the mechanical properties of the stabilized mixture. The experiments included a compaction test and an unconfined compressive test, an indirect tension test, an indirect compression test, a modulus, a drying shrinkage, and a frost resistance testing.
The results showed that LSB’s (lime-stabilized boron waste mixture) mechanical strength meets the requirements for road base when the lime content is higher than 8%. Because of its low frost resistance, LSB cannot be used in frozen regions.
The lime-cement-stabilized mixture can be used in frozen areas when lime and cement contents are 8% and 5%, respectively. Effectively, aggregate reduces drying shrinkage coefficient. For mixture stabilization, aggregate is recommended. This study provided a suggestion for managing boron waste.
Performance
Stability and Strength
An unconfined compressive test is often used to determine the compressive strength. Higher UCS values indicate better engineering performance. It was thus used in the study to determine the optimal road base mixture.
It was found that a lime-cement-stabilized boron waste mixture has higher compressive and tensile strength than those of a lime-stabilized one. Unconfined compressive strength (UCS) increases with lime content and curing times. UCS’s can be used for curing 7 or 28 days if the lime content is less than 3%. When lime content is low, the cementitious phases, such as calcium hydroxide crystals and hydrated silicate, are not sufficient to form the bearing structure of the stabilized mixture. This can cause damage to the LSB.
According to Specifications for Design of Highway Asphalt Pavement of China, lime-stabilized materials’ UCS (or time required) should not exceed 0.8 MPa. It should not be less than 0.6 MPa for the sub-base. LSB can also be used for sub-base construction if the lime content exceeds 5%. For the road base, lime content should not exceed 8%.
Cracking and Shrinking
Micro-cracks are formed around aggregates due to drying shrinkage. This causes a decrease in mechanical properties and road foundation cracking. This study investigated the drying shrinkage characteristics of the stabilized waste mixture of boron.
Drying shrinkage coefficients of lime-cement-stabilized boron waste mixtures are all less than those of lime-stabilized boron waste. Soil and aggregate are suitable fillers to improve drying shrinkage. To reduce drying shrinkage, it is recommended that aggregate and soil be adequately combined.
Frost Resistance
Freeze-thaw can harm the mechanical properties and stability of stabilized materials. Therefore, the frost resistance of lime cement and lime cement stabilized boron waste mixtures was investigated.
The specimens were destroyed after four freeze-thaw cycles. Frost resistance indexes are not available for all types of LSB. The anti-freezing requirements of road bases or sub-bases are not satisfied by lime-stabilized boron waste. LSB can only be used in non-frozen areas. The other stabilized method must be considered if LSB is used in frosty regions.
Boron Waste in Concrete and Bricks
Boron waste has been gradually used in brick and concrete for sustainable development and industrial ecology. The impact of boron on concrete’s strength and workability was examined in a study. It had a slight effect on workability. Mechanical strength was not affected. Concrete’s power did not change when the concrete contained less than 10%. This waste also improved concrete’s durability.
Another study used boron waste to make lightweight brick. It was investigated how the heat, burning rate, and temperature affected the brick’s performance. It was suggested that the waste could not be used as a structural brick because it caused crashing during firing. Brick quality was better when the waste content was lower than 30%.
A study revealed that modified mortar had higher compressive and flexural strength than the control sample. However, the waste content was lower than 1.5%. The modified mortar had power almost equal to the control, even though its waste content was between 2.5% and 5.0%. The durability of mortar is not affected by waste. This waste was also used as a fluxing agent to produce red mud brick.
The results showed that the firing temperature dropped. Bricks with more than 15 wt% waste had a higher compressive property. They also recently used the waste to make lightweight artificial aggregate (LWA). The sieve and dewatering of boron waste (SBW, DBW) could create a lightweight aggregate. Reusing boron waste in concrete and brick increases management efficiency.