Catalytic Cracking Processes
Fluid Catalytic Cracking (FCC) catalysts have recently been introduced by BASF to provide more flexibility to mild and moderate-resid feed units. The Borotec portfolio, based on the Boron Based Technology (BBT), uses boron as a key ingredient in the catalyst formulation, which results in increased yields of high-value products.
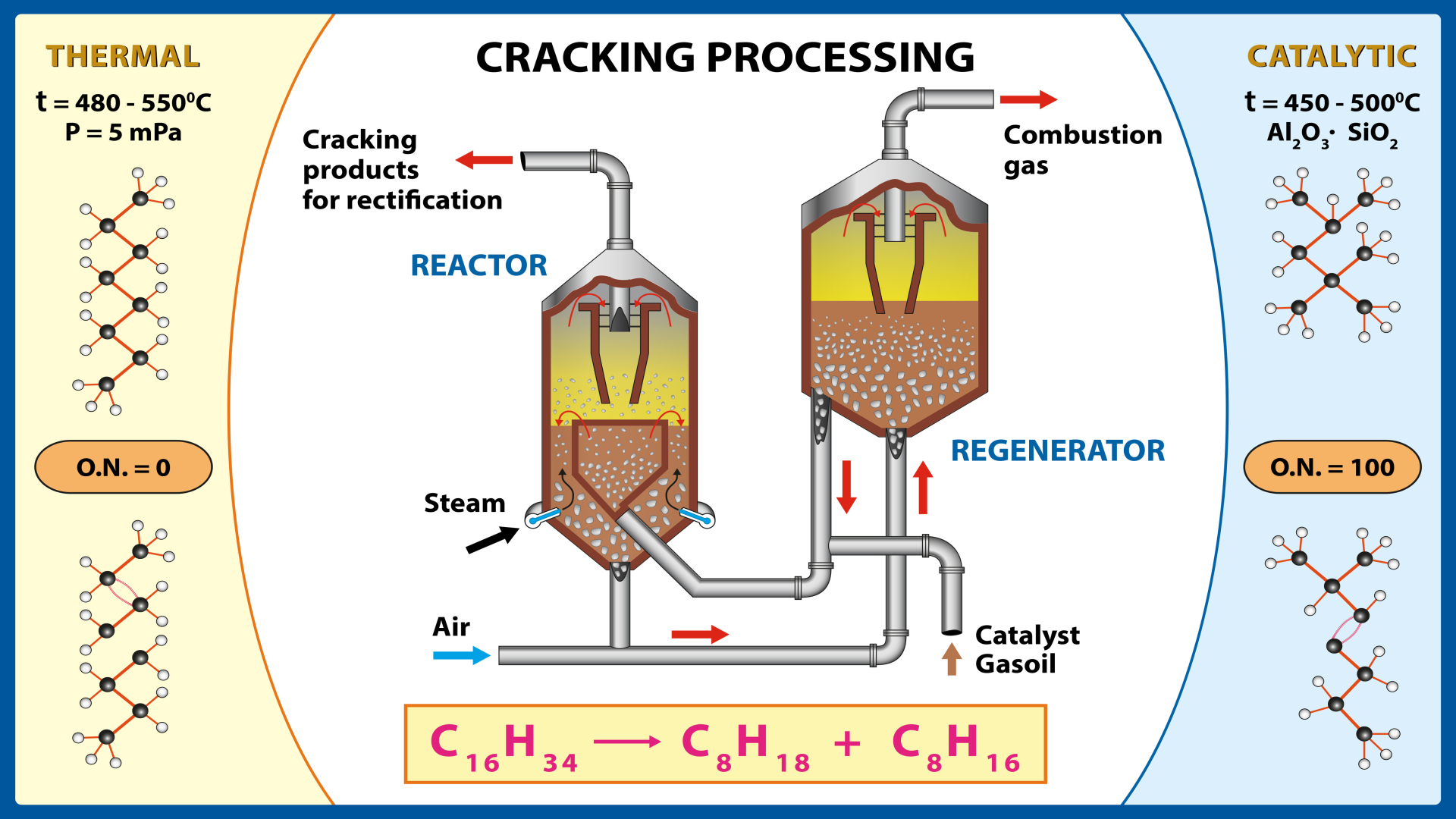
Catalytic Cracking Processes
What is Catalytic Cracking?
Catalytic Cracking is a conversion process used with a wide range of feedstocks, including gas oil, heavy crude oil, and residuum. Catalytic cracking is similar to thermal cracking, but it uses a catalyst that is not consumed, making it more efficient in the process and product slate. Usually, the feedstocks for catalytic cracking can be anyone (or a combination of them): Straight-run gas oil, vacuum gas oil, and heavy feedstocks such as heavy oil, extra-heavy oil, atmospheric residuum, vacuum residuum, and tar sand bitumen.
In the commercial process for catalytic cracking, a feedstock (usually a gas oil fraction) makes contact with a catalyst under pre-determined temperature, pressure, and time conditions. A substantial portion (>50%) of the feedstock is converted into gasoline and lower boiling products, typically in a single-pass cycle. However, during the catalytic cracking reaction, carbonaceous material accumulates on the catalyst, which reduces its activity and must be removed before the catalyst can be reused.
This carbonaceous deposit is formed by the thermal decomposition of high-molecular-weight polar species in the feedstock. The deposit from the catalyst is usually removed by burning in the presence of air until catalyst activity is restored.
What is Fluid Catalytic Cracking?
The Fluid Catalytic Cracking (FCC) process converts high-boiling-point, high-molecular-weight petroleum hydrocarbons (crude oils) into gasoline, olefinic gases, and other petroleum products. Thermal cracking was initially used to crack petroleum hydrocarbons. Still, catalytic cracking has nearly replaced it because it produces more volumes of high octane rating gasoline and by-product gases with more carbon-carbon double bonds (i.e., olefins) of higher economic value than thermal cracking gases.
The feedstock for the FCC conversion process is typically heavy gas oil (HGO), a portion of the petroleum with an initial boiling-point temperature of 340 °C or higher at atmospheric pressure and an average molecular weight of 200 to 600 or higher. Heavy gas oil is also called “heavy vacuum gas oil” (HVGO).
The HGO feedstock is heated to a high temperature and medium pressure before coming into contact with a hot, powdered catalyst. This breaks the long-chain molecules of the high-boiling-point hydrocarbon liquids into short-chain molecules, collected as vapor.
One of the challenges in processing heavier crudes is that they often contain nickel (Ni) contaminants. Ni can deposit on the FCC catalyst and cause dehydrogenation reactions that produce hydrogen and contaminant coke, both low-value products that reduce the FCC unit’s profitability.
There is a high demand for improved Ni passivation technology to address this challenge. This is helpful when the FCC unit functions at the wet gas compressor (WGC) limit. After removing the WGC limit, it is possible to increase profitability by increasing either the FCC unit efficiency or the operating severity. Passivators such as antimony or specialty alumina – or, more recently, Boron Based Technology – can be used to reduce the nickel’s effect.
Ni Passivation Technology
Ni passivation technology using antimony compounds was first invented by Philips Petroleum Company and is now used for over 40 years.
Antimony (Sb) based Ni passivation chemicals are infused into the feed to reduce the dehydrogenation effect of Ni by 20-40%. After infusion, dry gas production and delta coke are immediately reduced.
However, Sb can also pollute carbon monoxide (CO) combustion promoters and enhance nitrogen oxide (NOx) emissions. There are also environmental and safety concerns to consider. Because of this, the use of antimony is prohibited in all FCC units. Furthermore, the antimony pick-up by the FCC catalyst varies on several factors, reducing the effectiveness of this Ni passivation technology.
A common way to reduce Ni deposition and related problems in resid-FCC catalysts is to use specialty aluminas. These materials work by keeping Ni in an increased oxidation state, which reduces overall hydrogen and toxic coke production. However, the effectiveness of this approach is inhibited by Ni’s low mobility and the immobile nature of alumina traps.
It is well-known that Ni accumulation on resid-FCC catalysts follows a gradient, with more Ni accumulating on the outer surfaces of catalyst particles. This phenomenon can be quantified using the peripheral deposition index (PDI). It was observed that Ni generally has high PDI values, confirming its severely limited mobility.
Because Ni accumulates on the catalyst’s surface, making it difficult for alumina to reach and trap it, it indicates that alumina’s ability to passivate Ni is limited by a lack of alumina trap and Ni mobility. As a result, BASF set out to create the next generation of Ni passivation technology.
Boron Based Technology (BBT)
Boron-based chemistry is a highly effective way to passivate nickel, explicitly developed for BASF’s Boron Based Technology (BBT) platform. Researchers have examined boron chemistry to assess the Ni passivation process.
Multiple spectroscopic studies showed that Boron Based Technology helps Ni stay in a more electron-deficient state by reducing its reactivity in dehydrogenation reactions and thus reducing the formation of hydrogen and contaminant coke.
Furthermore, BBT provides several advantages as boron, unlike antimony, has no effect on NOx emissions in the FCC. Also, boron is mobile in FCC conditions, which shows its greater efficacy in Ni passivation than specialty alumina.
Alternatives for Refiners
Borocat, the first FCC catalyst based on the BBT platform, was introduced commercially in 2016. It has since been successfully implemented in refineries all over the world. The results show that refineries using Borocat can perform harder with more contaminated feedstocks and thus enhance profitability.
Refiners pleased by Borocat’s success requested BASF to develop a catalyst that is perfect for any quality or for mild to moderate-resid feedstocks. The solution was the Borotec FCC catalyst. Borotec, introduced in 2017, is BASF’s most recent innovation from its BBT platform.
Borotec was tested against other suppliers’ top-quality bottoms upgrading technologies at a refinery that processes a mild-resid feedstock. Borotec demonstrated good metals tolerance and improved liquid yields in a commercial trial. In comparison to competitors’ catalysts, Borotec allowed the refinery to:
- Reduce hydrogen and contaminant coke production
- Enhance activity retention at similar vanadium and sodium levels, and bottoms upgrading and liquid yields
- Enhance propylene and butylene productivity after optimizing catalyst
This successful commercial trial validated Borotec’s ability to improve performance, resulting in higher yields of valuable products and lower bottom-of-the-barrel yields. Borotec’s optimized metals tolerance feature offers better crude flexibility for refiners, increasingly engaging in spot buying to boost revenue. The Borotec FCC catalyst was created to provide them with improved operation and margins.