Borates in Metallurgy
Borates have been used over the centuries for both non-ferrous smelting and precious metals refining. Evidence suggests that gold-makers used borates as a fluxing agent even in Babylonian times. Borates lower the melting point and prevent oxidation. They also remove metal oxides and help to adjust the slag’s viscosity for easier removal from the molten metal. Borates can also be used in lead recycling and metal recovery.
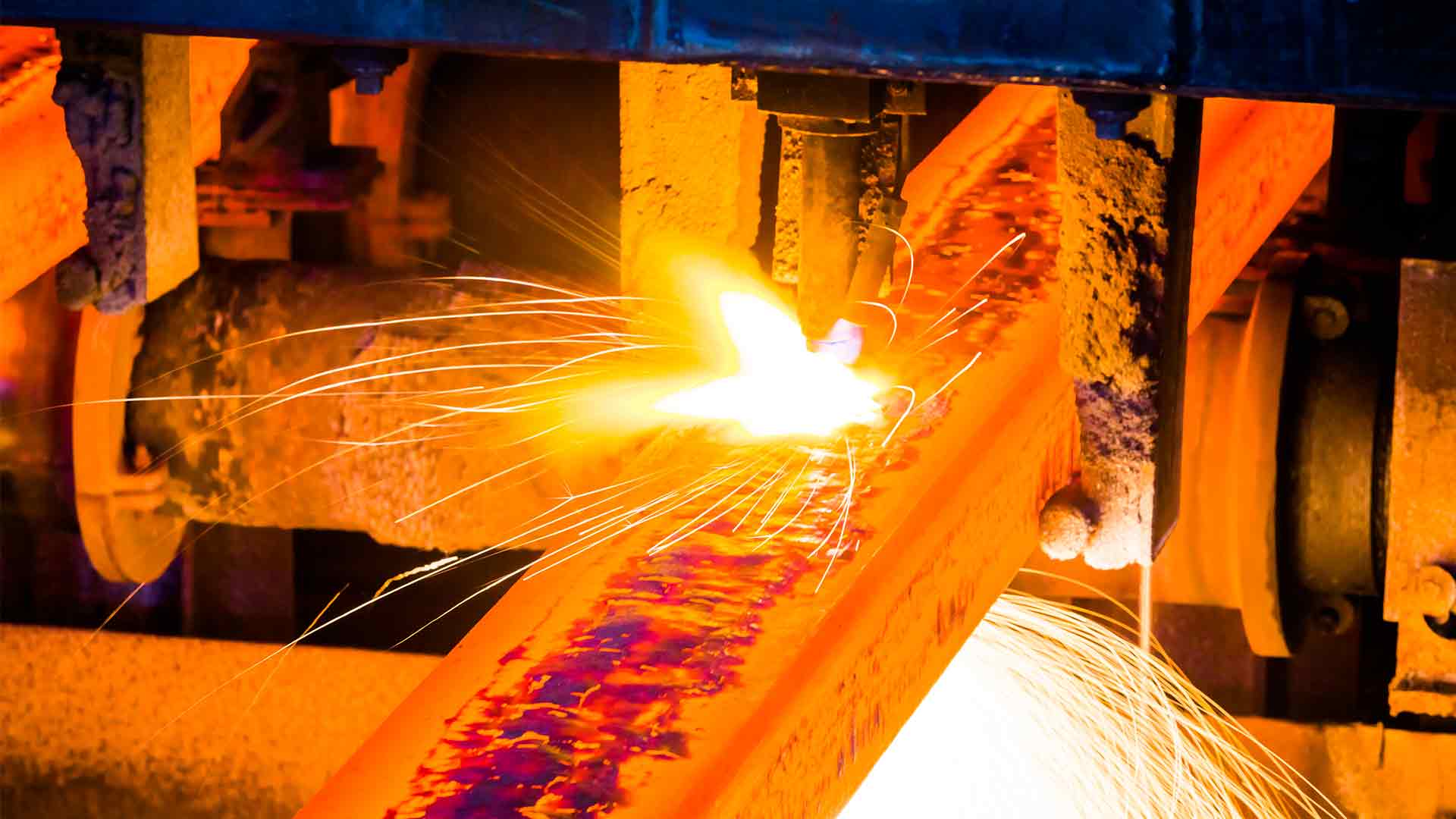
Borates in Metallurgy
History of Borates in Metal Refining
The history of gold refining dates back to Egypt between 5,000 and 2000 B.C. According to other legends, the Babylonian goldsmiths used borax as a metalworking fluid from the East. It is believed that Georgius Agricola (1400-1555), or Vanoccio Buringuccio (1480-1538), in their book “De Natura Fossilium,” suggested that Chrysocolla, also known as borax, was the fluxing agent for metal refining in that period.
Types of Borates Used in Metallurgy
Borates are used as a flux in smelting to produce steel and other non-ferrous metals. Borates are used in this capacity to dissolve metallic oxide impurities. These are then removed from the slag. Borates can also be used as a cover flux to protect against oxidation.
At a low enough temperature, borates can associate with metallic oxide contaminants. This allows for a reduction in the loss of precious metals and wears on melting equipment. Anhydrous borax is used for gold refinement in flux formulations to dissolve metallic oxides. It also serves as a flux in the gold assaying process. Anhydrous borax is usually added to the smelt at a rate of 10-50%, depending on the process.
Hydrated sodium borate (49% B2O3, water content 29%) can also be used. However, it takes longer to dehydrate the hydrated borate to form anhydrous borax in a melt because of puffing and intumescence. This can pose a safety risk and slow down production. Due to the higher water content in the borate crystal, it is more corrosive than anhydrous borax. However, it is less expensive than anhydrous borax.
To avoid the glare caused by sodium borate, potassium pentaborate can be used in fluxes for stainless and other non-ferrous metals. Potassium pentaborate is an alternative to fluorine-containing flux compounds in refining and producing copper, copper alloys, and precious metals. This helps to reduce fluorine emissions.
Benefits of Borates in Metallurgy
Borates can be used in non-ferrous smelting, fluxing, slag stabilization, precious metals refining, lead recycling, and metals recovery. Borates can reduce the melting point and prevent oxidation. It also removes metal oxides. Anhydrous borax is an excellent option for gold refining too. Some of the metallurgical processes and the benefits of borates are discussed below.
Fluxing
The glass, ceramic, or other vitreous industries have long known the benefits of borates’ fluxing value. The same fluxing action helps purify precious and non-ferrous metals (i.e., brass, bronze, copper, gold, platinum, silver, zinc, etc.) by lowering the batch’s melting point. Borates are an essential additive in the metal recovery process.
These non-ferrous and precious metals are often derived from scrap metals or the slag portion of the primary smelting process. If separated by metal oxides and other impurities, the secondary smelter will have a higher yield and much higher value.
A borate compound is used to charge the furnace. The target scrap metal is placed on top, with approximately half of the borax needed. The rest will be added during the refinement phase. The furnace’s ratio of metal scrap to borate will vary depending on the type of furnace and the metal being recovered.
The borate melts, creating a pool of fluxing materials covering the metal that has already started to melt. The molten borate compound helps bring these metal oxides and impurities from scrap metal to the surface.
Silica sand can sometimes be found at the melt’s surface. This helps to thicken the metallic liquid and increase the viscosity. After the impurities have been removed, the purer iron can be poured out of the furnace and allowed to cool ingot moulds
This process works well for cupola furnaces. However, other furnace technologies may require you to add borates to the scrap metal to charge the furnace with the reclaimed metal scrap.
Slag Stabilization
Most steel slags are rock-like and hard upon cooling—however, some slags, especially those made from stainless steel, form powdery particles. Anhydrous borax can be added to prevent the formation of dusty slags. This creates a βC2S-polymorph condition which results in a stable, rock-like material. This approach has many benefits, including less slag dust and easier slag handling, a reduction in regulatory oversight, and revenue from selling slag.
Recovery of Precious Metal Ore (Gold)
After the gold concentrate is separated into acid and base gangues and pyrite ore, it is subject to oxidation, sulfurization, and smelting to remove any metal oxides and impurities. The gold is usually refined in ceramic crucibles to reach its final state. To remove potential oxides in the gold-metal concentrates, oxygen is injected into the melt.
These oxides rise to the surface and form a slag. This slag is then removed from the melt before being poured into bars, more commonly called “bouillons.” Because of its safety and excellent fluxing, anhydrous borax is often used.
Borates in the recovery of gold have several benefits. It can recover precious metals with minor loss of slag. It helps to reduce the sintering temperature, which prevents the formation of combustible material and minimizes fuming.
Borates can form fluid slags with a tiny attack on refractories. They can quickly thicken slag, which will prevent intumescence and puffing.
Lead Recycling and Metals Recovery
Scrap or slag from primary smelting operations can recycle and recover metals like brass, bronze, copper, lead, and zinc. To produce a product that is as pure as the primary metal, it is necessary to remove all oxides and other impurities.
Borates are fluxes that help melt and combine with metallic oxides at low temperatures to bring them up to the surface of melt as a slag. This can be skimmed or decanted.
Borates are valuable in lead recycling and recovery and other metals. Borates are purer than other metals due to their high solvent activity on siliceous and metal oxides. Due to the lower liquidus temperature, highly fluid slags can be formed, allowing more lead extraction. Based on metal chemistry, slags can be thickened or skimmed easier.
The furnace’s melting point is lowered, which reduces energy costs. Inorganic borate compounds can be handled more efficiently and safely than other alternatives. They are also non-combustible and have a low fuming tendency.