Borates in Paints, Inks, and Coatings
Borates in paints are widely used in paints, coatings, and printing inks as buffering agents. They also provide flame retardant, anti-corrosive, and anti-bacteria protective benefits, applied in marine and aviation coatings for example. Boric acid, borax decahydrate, borax, zinc borate, and perborates/metal borates are compounds most used in paints and coatings.
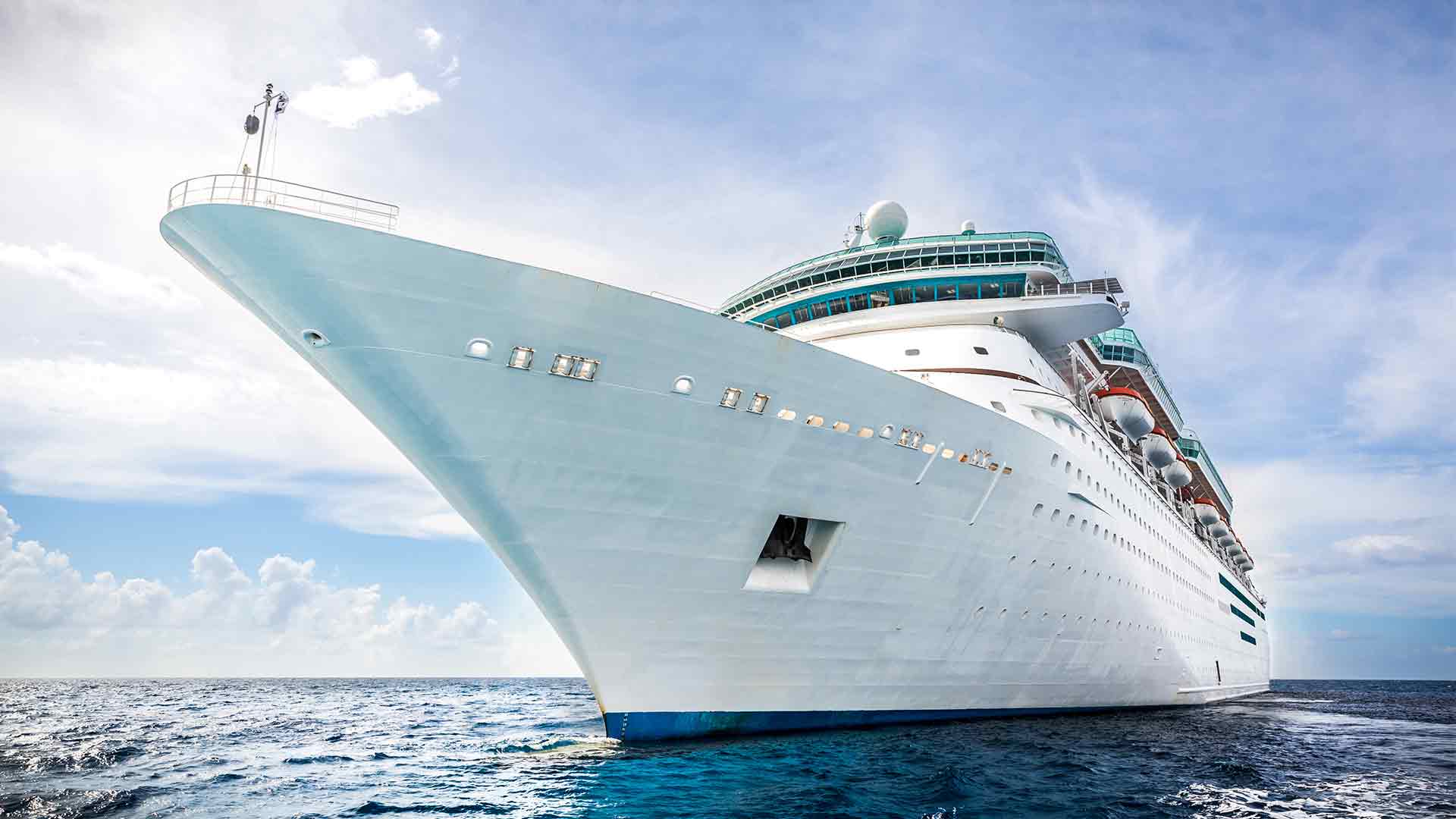
Boron in Paints, Inks and Coatings
Use of Borates in the Paint & Coating Industry
Borates are used in the paints and coatings industries in various ways. These include coil coatings in steelworks (coil coatings), body shops, and use in metalwork. Use in car refinishing, offset printing inks (as specialist driers), interior wall paint, use as a corrosion inhibitor and catalyst, and use in marine, yacht, and aerospace protective coatings for fire retardancy are the other applications of borates.
The literature also refers to the role of borates (especially sodium borate) as buffering agents (for controlling pH) in printing inks. Borates can also be used as multifunctional coating additives. Borates have flame retardant, biostatic, and stain resistance properties that are particularly beneficial for wood coatings.
Types of Borates and Applications
Borates are used extensively in marine, yachting, and aviation coatings. Borates (especially sodium borate) can act as a buffering agent (controlling pH) for printing inks. They can also be used as multifunctional coating additives. Borates’ flame retardant, biostatic, and stain resistance properties are particularly beneficial for wood coatings. Two prominent examples of such coatings are Borogard and Firebrake – see below.
Marine, yacht, or aerospace coatings can be enriched with borax decahydrate and boric acid to improve flame retardancy. Barium metaborate (also known as barium diborate) is a fungicide, bactericide, and anti-corrosion pigment added to paints and coatings.
The soluble barium compound is used in production, along with sodium metaborate. Additions of 10-15% are recommended for industrial primers. Corrosion can be prevented by adding as low as 1% barium metaborate.
Perborates/metal borates are specialist driers for oxidation drying sheetfed offset inks commonly used to print paper and board packaging. This helps to reduce cobalt oxide dryer consumption. Magnesium triborate (MnB4O7.3H2O) and magnesium dihydrate (MnH4O(BO3)2) is used mainly as surface driers for paints.
Perborates also have flame retardant properties. Borax powder, zinc borate, and several other borates are also used in paints or coatings. Zinc borates serve as multifunctional coatings additives.
(image: applications of borates in paints etc.)
Benefits of Borates
Flame-retardancy
Boric acid is used to make an intumescent fireproofing coat for structural metalwork (e.g., buildings) and in protective marine, yacht, and aerospace coatings. Boric acid is necessary to achieve the technical performance needed to protect structural metalwork from fires. They provide time for the evacuation of buildings and allow the fire service to respond effectively.
Only certified and trained professionals can apply these products. They use complete protective equipment to reduce the chance of being exposed to the coating. Therefore, these products are vital for avoiding loss of life, which should outweigh any residual risk.
Drying
Perborates and metal borates when they are not more than 0.5% by weight in a specific number of types of offset inks types of printing inks (e.g., oxidation drying sheet-fed offset inks), specialist driers are used to reduce the overall level of driers and specifically the levels of cobalt driers (such as cobalt octoate).
These transition metal borate and perborate complexes are unique in being water-activated driers. They are inactive in ink until they reach the aqueous fount solution used on lithographic printing presses at the point of printing. They are only effective where required, allowing for smaller driers overall.
This reduces costs, minimizes hazards, and decreases rejections of printed products due to oxidation byproducts from excessive drying. This is a very niche application, but it is hard to replace.
Alternatives include cobalt carboxylates and manganese carboxylates. However, to replace metal borate driers with metal borate driers, higher levels (up to 150% more) would be required for cobalt and manganese-carboxylate driers.
Buffering
Borates have excellent buffering properties. Due to the variety of borates’ physical properties, including different aqueous solubilities (anywhere from pH 4 to 11), the formulation environment can be matched, and incompatibility or stability issues can be avoided.
Miscellaneous Benefits
Interior wall paints that are multi-colored can have 0.01 to 0.06% borax powder. This is used to increase fleck formation and strength, and flocculation. This prevents different color particles in paints from showing up when the paints are applied to a wall. Borates increase luster, durability, and chemical resistance. Boron lends paint anti-bacterial, antioxidant, and antifungal properties.
Borates for Efficient Coatings
Borates can be used as multifunctional coatings and additives. Borates can enhance wood coatings by their flame retardant, stain resistance, and biostatic properties. Borates are also cost-effective and can be used to produce high-performance coatings. For example, if zinc borate were being used for tannin stain resistance, it is unnecessary to use a separate dry film fungicide, in-can preservative, or in-can corrosion inhibitor.
Borates also have a low effect on dry paint films’ optical properties and transmission properties. This is important in a time where semi-transparent wood staining is gaining popularity. In conclusion, borates are cost-effective, non-harmful, and safe for the environment and thus are an excellent alternative for coating formulation. Borogard is a well-known example of such a coating. Firebrake is another.
Borogard
Borogard (2ZnO.3B2O3.3.5H2O), an EPA registered zinc borate, is used to inhibit corrosion in organic solvent-based as well as waterborne coatings. This bright white powder is easily dispersible and does not affect brightly colored or pure-white coatings. Borogard can be used in place of zinc chromate. The typical dosage levels are 60 to 120g/l. Zinc borate can be used as an in-can preservative and a corrosion inhibitor in both aqueous or non-aqueous coatings. It can also be used in specific fire retardant or intumescent coatings.
Firebrake
The company Borax also supplies Firebrake, a boron-based coating ingredient. It comes in many forms.
Firebrake 415 (zinc borate) is one version that is used as a flame retardant and smoke suppressant in coatings. It has a high temperature at which dehydration can begin. It’s suitable for systems that require very high temperatures.
Firebrake 500 (dehydrated Zinc Borate) is another option. It is used in coatings as a flame retardant, smoke suppressant, and fire retardant. It does not contain water of hydration and has a significant positive effect on heat release.
Firebrake-ZB, which is multifunctional zinc borate, is another option. It can be used as a flame retardant and smoke and afterglow suppressant. It is suitable for systems that require high temperatures. It retains a lot of translucency and can be used with low pigment loading. It can be combined with antimony oxide, alumina trihydrate, magnesium hydroxide, and silicone polymer.