Boron Becoming Essential in EV Production
Demand from the EV industry for key metals such as Boron is on a swift upward trajectory. Copper, nickel, and lithium are some of the key metals required for EV battery production. As a result, demand growth for nickel from EVs is expected to increase 14 times between 2019-2030. Lithium and copper are expected to experience a growth in demand of 9-10x.
The growth in battery production and increased fuel efficiency standards have created a need for more copper, nickel, and lithium. As a result of this demand increase, the price of these metals will also rise exponentially over the next few years. (Source: Visual Capitalist)
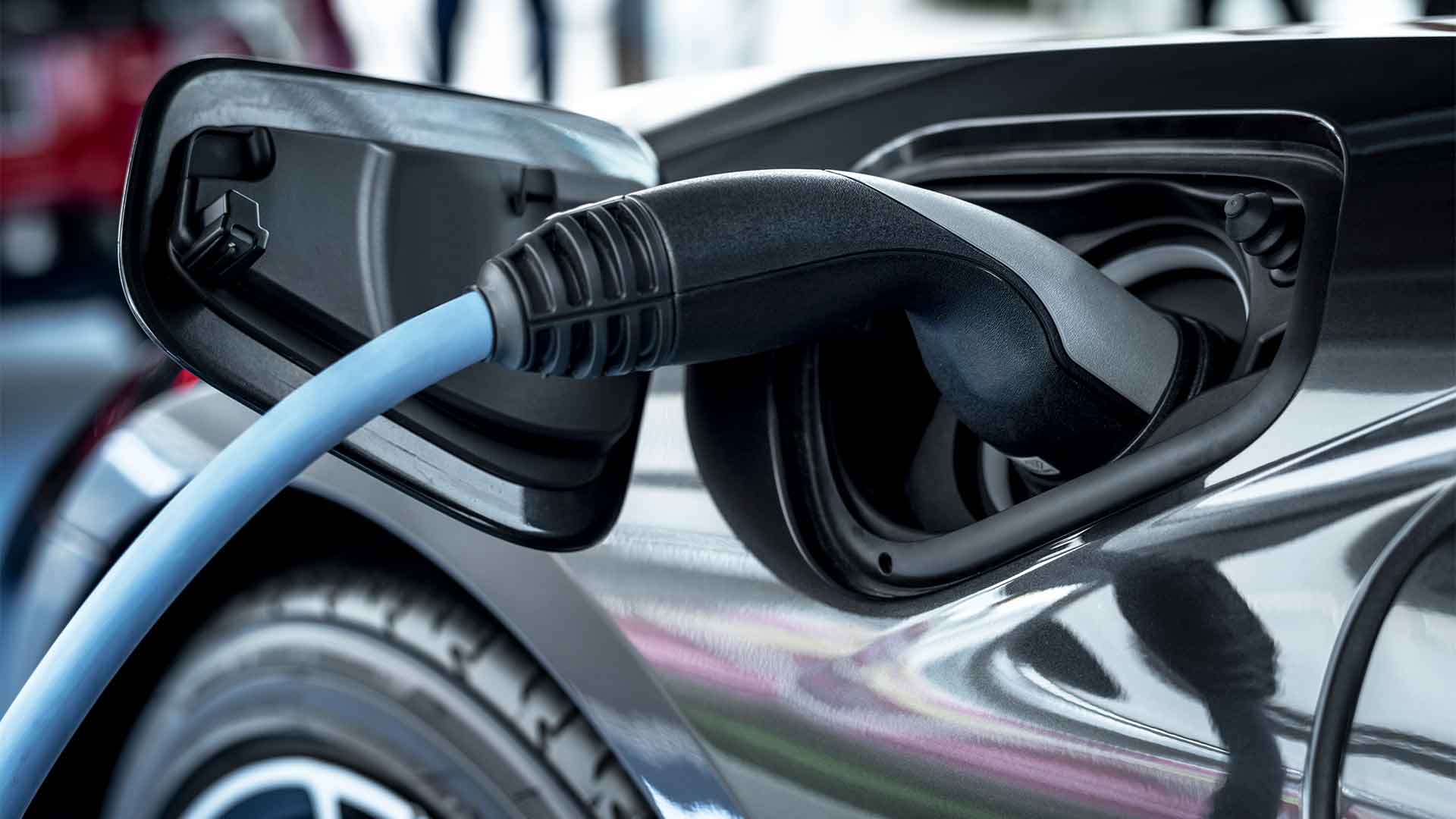
Factors driving the growth of the EV market
Climate change is making people more aware of the environment and they are demanding products with fewer emissions. In 2040, it’s predicted that half or even more cars sold will be electric vehicles because of this shift in demand.
The electric car is an innovation that has the potential to radically change transportation as we know it. Governments around the world are aware of this and have committed to a new goal: 20% of all cars must be EVs by 2025.
Tesla is leading the pack in the electric car market, and investors are noticing. Tesla shares have seen a 1,000% increase since March 2020 due to its impressive innovation skills as well as other popular EV makers like NIO of China. However, traditional automakers like Mercedes-Benz are also shifting their focus to this new technology trend that’s taking over America’s roads
Vital chemical elements in building Electric Vehicles
The EV Revolution is in full swing, many people are wondering what it takes to build an electric vehicle. The first element is Lithium, which can be found in the Earth’s crust. The second element is Cobalt, which is mined from rocks and soil. The third element is Nickel, which comes from deposits of coal or ore.
Finally, the fourth and final necessary element for EV cars to work properly are Graphite electrodes that store electricity on one side and discharge it on the other. When these four elements are combined, they create a battery that powers electric vehicles (EVs). These batteries have high energy density making them an environmentally friendly way to power the car. Aluminum, Phosphorus, Iron, Copper, Manganese are also few other elements used in building an EV.
Plan To Replace Two Billion Gas-Run Vehicles with Electric Powered Cars
With the focus on redesigning cars, buses, and HGVs around lithium-ion batteries, part of this Government’s Road to a Zero strategy is all about replacing two billion gas-run vehicles with ones powered by a more sustainable technology like electric power. Will, there be enough resources for everyone to have an eco-friendly vehicle.
The solution to the battery problem may be much easier than we think. The only two things needed are boron and hydrogen, which are available in abundance. Almost all of the world’s reserves for both materials reside in Turkey. What makes this even more incredible is that water contains two parts hydrogen per one part oxygen, so it should not be too hard to find many sources around us.
Boron: The Fuel of Supercapacitors
Electrical capacitors are necessary for storing electrical energy. One of the most popular types is made from borate chemicals, which can be found in many formulations and parts of manufacturing aluminum-plate capacitors. Supercapacitor technology relies on an electrolyte containing a small amount of Boron that allows them to store 10 times more charge than traditional batteries with better durability over time making electric cars possible.
Boron has a higher energy density than lithium
Boron is a chemical element known for having the highest energy density than lithium, and there’s mounting evidence to indicate that it could power tomorrow’s technology. It can sustain high temperatures without melting, which is why scientists are exploring its potential in areas like advanced hybrid car engines and batteries.
Lithium batteries are prone to catching fire when overcharged or overheated, which could present safety risks
Lithium batteries, the ideal power sources for a variety of devices and machines, are prone to catching fire when overcharged or overheated. Battery safety is important in transportation industries such as airplanes and hybrid-electric automobiles. Boron-based batteries have a higher threshold for charging. This means they can be recharged more times without overheating or getting puffed up, saving you time and money in the long run.
The cost of manufacturing boron-based batteries is much lower than the cost of producing lithium-based batteries
Boron-based batteries are quickly becoming a more affordable option for those searching for rechargeable battery power. What sets them apart is that they use significantly less rare earth materials to produce which translates into much lower manufacturing costs a full 30% less expensive than lithium-ion. They also boast an impressive 20,000 charge cycles before needing replacement.
If scientists can find an efficient way to produce boron-based battery materials, they will offer better performance and longer lifetimes at a lower price point
The future of battery technology is now. Scientists are working on developing an efficient way to produce boron-based batteries, and if successful these new materials will offer better performance, longer lifetimes, and a lower price point. Until this discovery scientists have been limited to the lithium carbonate material for their energy storage units (batteries).
Lithium cells often wear faster than anticipated due to daily exposure to heat fluctuations that cause expansion within the cells which leads to a loss in voltage strength and electron leakage over time. This is where boron comes in; it has excellent mechanical properties as well as promising electrical conductivity that has increased total capacity by up to 25% with three times stronger stability during charge/discharge cycles.
Scientists have already begun experimenting with using renewable sources like solar power for the production of boron-based battery materials
Within the field of cathode materials, there are few people less well-known than Dr. Henry Klopman, Sr. When discussing the possible outcome of a shift to renewable-based battery production, he is optimistic about the future for our planet as well as for researchers and electrochemists. “I spent my life working specifically on boron chemistry and light elements,” said Dr. Klopman from his laboratory at Cornell University. “Producing electrodes with clean energy means performing identical equipment setups without any power source.”