Boron Fibers in Aviation
Boron fibers in aviation are used extensively in military aviation as a tape product to repair cracked aluminium aircraft skins because of their thermal properties and anti-corrosive advantages. The application was first developed in the late fifties and used instead of carbon fibers that were unavailable in continuous lengths and glass fibers or with sufficient modulus. Boron fiber was the preferred product for the horizontal tail skins on the F-14 Tomcat fighter aircraft and the horizontal and vertical skins and rudder on the F-15 Eagle.
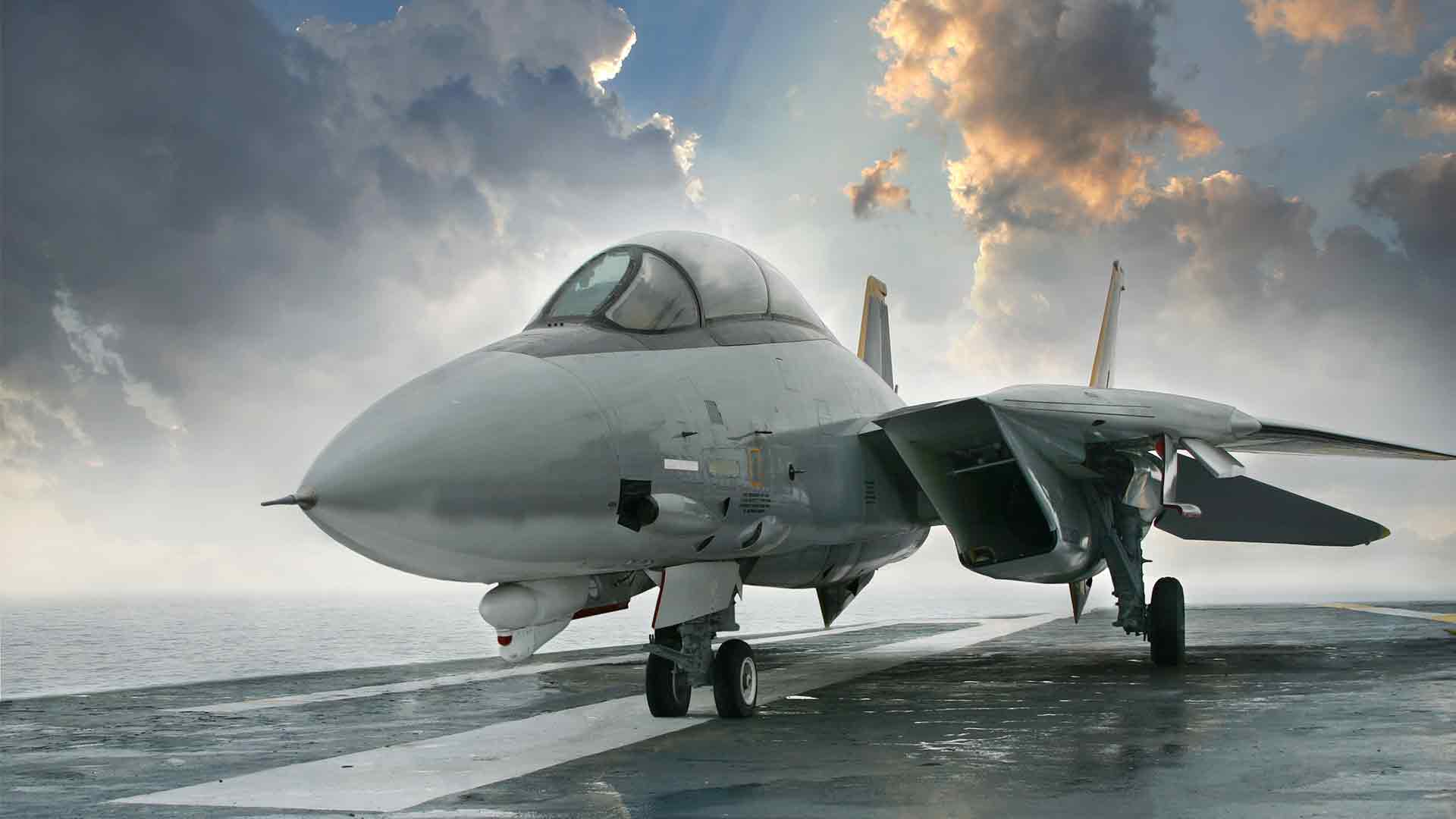
Boron Fibers in Aviation
What is Boron Fiber?
Boron fiber, also known as boron filament, is an amorphous elemental boron product. It is the primary industrial use for elemental (free) boron. Boron fibers have high compressive and tensile strength and are incredibly stiff. Boron fibers have a low density and high modulus elasticity. They are not flexible and therefore only available as prepreg tape products. The boron fiber is often used in conjunction with an epoxy matrix.
Boron fibers can be made by chemical vapor deposition (boron on tungsten or carbon core) of approximately 12μm in diameter. Boron fibers are 100–200 μm in diameter. They are very brittle and susceptible to surface damage. Boron fibers are used primarily in metal matrix composites. They will degrade when they contact aluminum and titanium matrices at temperatures above 500°C. Chemical vapor deposition, which covers the fiber surface with layers of about five μm-thick layers of silicon carbide, SiC, (such fibers are called Borsic), or boron carbide, is used to prevent this degradation.
Boron fibers can pose a danger to personnel and are extremely expensive; hence, they are mainly used in military aviation. In the 1990s, boron applications grew with the introduction of Hy-Bor (a combination of boron fibers and carbon fibers that maximizes their properties). These include the General Atomics Reaper unmanned air vehicle (UAV), bicycle parts, and fishing rods. Gen 2 Hy-Bor’s recent developments have led to a broader range of carbon fibers resins and have sparked interest in new applications such as hypersonics or sporting goods.
Applications of Boron Fibers in Aviation
Boron fibers are mainly used in military aviation. When carbon fiber was unavailable in continuous lengths and glass fibers did not have sufficient modulus, boron fiber was chosen for the horizontal tail skins on the F-14 Tomcat fighter aircraft, and the horizontal and vertical skins and rudder on the F-15 Eagle. Boron fiber was used to minimize the aircraft’s mass and reduce flutter.
Boron fibers are now available only as a prepreg tape product and can repair cracked aluminum aircraft skins. The thermal expansion of boron is similar to aluminum, and there is no possibility of galvanic corrosion.
History of Boron Fibers in Aviation
E.J. Weintraub first reported vapor deposition of boron fiber in 1911. However, Claude Talley and co-workers from Texaco Experiments, Inc. were first to demonstrate the possibility to produce a continuous, high strength, high modulus fiber by chemical vapor deposit in 1959. The U.S. Air Force Materials Laboratory funded further development of the process.
Along with Texaco, United Aircraft Research Laboratory, Avco Systems Division, General Electric Research Laboratory, Monsanto, Batelle Memorial Institute, and others were the initial contributors. Avco Systems and Hamilton Standard (a United Aircraft Corporation division) were the two remaining companies.
Avco built a 10,000 lb./year production plant in 1970. In 1971, it purchased Whittaker tape to make B/Ep tape. It also increased the fiber production capacity by several steps to 30,000 L/year. By the late 1970s. Avco and Hamilton Standard supplied B/Ep tape for Grumman’s horizontal stabilizer on the F-14 and McDonnell Douglas for horizontal and vertical stabilizers and rudders on the F-15.
The tubes were used for the Space Shuttle Orbiter’s mid-fuselage structure, which General Dynamics made. They also provided the dorsal longeron for the B-1B Bomber by Rockwell. Other applications include building the horizontal stabilizers for the Sikorsky H-60 Black Hawk helicopter and the Dassault Mirage 2000, and various sporting goods like golf shafts and tennis rackets.
Boron Fiber – Production Process for Aviation
Aerospace-grade boron fiber must pass rigorous tests to determine its tensile strength as well as elastic modulus. The fiber is fed into a 12-50-spool creel, where it is collimated, precisely spaced, and then combined with the epoxy resin film. The unique characteristic of boron fibers is their corncob structure.
This allows for better mechanical gripping between resin and fiber. Prepregged tapes measuring 500 feet in length and 6 inches wide are the most common products shipped to aircraft companies. Boron fiber prepreg is similar in appearance and handling to graphite-based prepregs. It can also be used in many of the same manufacturing processes.
However, boron fibres also have some disadvantages. The fibers are not flexible and have a large diameter. They can only be purchased as prepreg tape products if the surface of the parent material has a contoured form; the boron will not work well. Boron fibers can pose a danger to personnel and are extremely expensive.