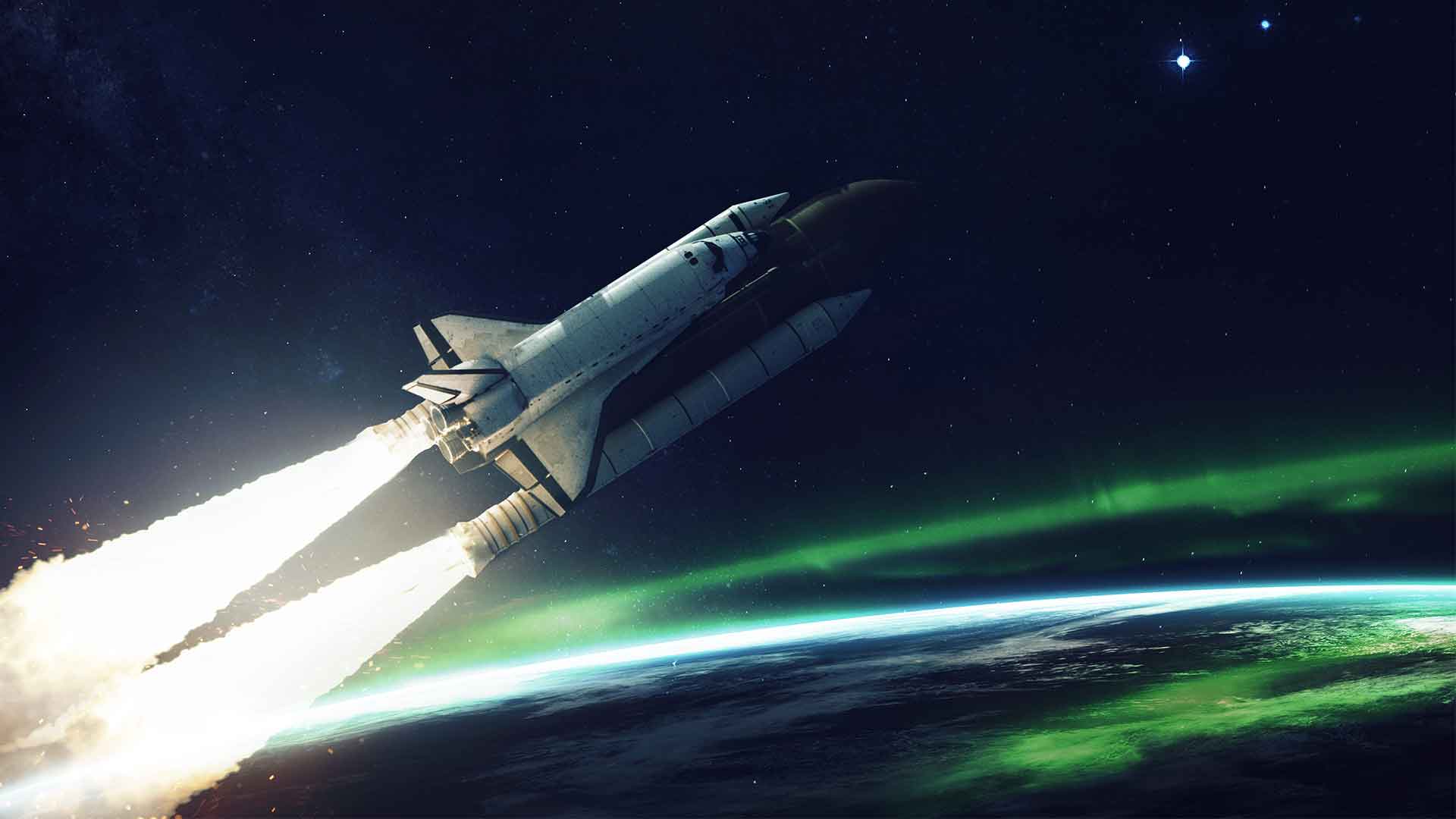
What Is Hypersonic Flight?
Hypersonic flight is a flight through the atmosphere below about 90 km at speeds ranging between Mach 5-10, a speed where dissociation of air begins to become significant and high heat loads exist.
As an aircraft moves through the air, the air molecules near the aircraft are disturbed and move around the aircraft. Exactly how the air reacts to the aircraft depends upon the ratio of the speed of the aircraft to the speed of sound through the air. Because of the importance of this speed ratio, aerodynamicists have designated it with a special parameter called the Mach number in honor of Ernst Mach, a late 19th-century physicist who studied gas dynamics.
For aircraft speeds that are much greater than the speed of sound, the aircraft is said to be hypersonic. Typical speeds for hypersonic aircraft are greater than 3000 mph and Mach number M greater than five, M > 5. We are going to define a high hypersonic regime at M > 10 to account for re-entry aerodynamics.
The chief characteristic of hypersonic aerodynamics is that the temperature of the flow is so great that the chemistry of the diatomic molecules of the air must be considered.
At low hypersonic speeds, the molecular bonds vibrate, which changes the magnitude of the forces generated by the air on the aircraft.
At high hypersonic speeds, the molecules break apart producing an electrically charged plasma around the aircraft. Large variations in air density and pressure occur because of shock waves, and expansions.
Why Is it Important?
Hypersonics could have the potential to transform the industry in a manner not seen since the introduction of supersonic flight in 1947 and supersonic transport in the late 1960s. While hypersonic travel, weapons, and defenses are just starting to be discussed more frequently, some will likely be ready for use within the next year.
Imagine being able to fly from Miami to Seattle in less than an hour. A study funded by the U.S. Air Force and completed by researchers at Binghamton University and NASA is taking steps towards that possibility.
An average flight from Miami to Seattle takes about six hours and 40 minutes, but imagine being able to reduce that time to 50 minutes or less. A recent study by NASA and Binghamton University researchers could lead to a drastic decrease in flight times. The study, funded in part by the U.S. Air Force, is one of the first steps toward the creation of planes able to move at hypersonic speeds, five to 10 times the speed of sound.
The Introduction Of Boron Nitride Nanotubes
Within the next decade, planes could be capable of traveling across the country by hypersonic flight in less than an hour all it would take is some boron nitride.
A key factor for a vehicle to maintain extremely high speeds is the intense amount of heat generated during travel; for example, the now-retired supersonic Concorde aircraft experienced temperatures of up to 260°F at its lazy cruising speed of 1,534 miles per hour. As such, the materials used to build these aircraft must also be able to withstand very high heat, in addition to being structurally stable and lightweight.
A study conducted by researchers from NASA and Binghamton University investigated the properties of nanotubes made using boron nitride, a combination of boron and nitrogen. The study revealed it could potentially be used to make hypersonic travel speeds above 4,000 miles per hour possible.
Currently, carbon nanotubes are used in aircraft due to their strength and ability to withstand temperatures up to 400 degrees Celsius (752 degrees Fahrenheit). Boron nitride nanotubes (BNNTs), however, can withstand up to 900 degrees Celsius (1652 Fahrenheit). They can also handle high amounts of stress and are much more lightweight than their carbon counterparts.
Applications
Currently, certain airplane structures use carbon nanotubes, a strong, lightweight structure that can withstand temperatures up to 450 degrees Celsius. But as this study showed, boron nitride nanotubes, which are similar in function, can withstand 900 degrees Celsius, temperatures that extremely fast airplanes need to be equipped to handle. They are also lighter and better than carbon nanotubes. Planes made from this structure could potentially reach hypersonic speeds, says Ke. (newsweek.com)
These nanotubes are something of a super-material. They are single-dimensional, tubular ” nanostructures ” that are not very dense and are therefore light. They have high tensile strength and are chemically and thermally stable.
In addition to being used in planes, boron nitride nanotubes could be added as a filler to ceramic or metals to make them stronger without damaging them. They might also be useful in environmentally efficient cars nanoelectronics While the price of $1,000 per gram is much too high to invest in for fast airplanes and rockets, economies of scale are at play. If NASA manufactures enough of the better material, the price will go down.
And as Ke points out, carbon nanotubes cost about the same in the 1990s. But because they have been manufactured so extensively, high-quality carbon nanotubes now cost about $10-$28 per gram. Ke believes that boron nitride nanotubes could be the standard manufacturing material in airplanes in the next five to ten years.
Boron Fibers Amplify Performance
In January 1969, Grumman Aerospace Corp. (now Northrop Grumman, Falls Church, Va., U.S.) was awarded the Navy contract for the F-14 Tomcat fighter aircraft. In December of that year, the Air Force awarded McDonnell Douglas (now Boeing) the contract for the F-15 Eagle. Both aircraft were fixed-wing designs that required a high-strength, high-modulus fiber to reduce flutter and minimize the mass of each aircraft.
At that time, carbon fiber was not available in continuous lengths and glass fibers did not have sufficient modulus. Ultimately, Grumman chose boron fiber for the horizontal tail skins on the F-14, and McDonnell Douglas chose boron fiber for the horizontal and vertical skins and rudder on the F-15. History was made when boron fiber (not carbon fiber) became the first high-performance fiber to be used in a production application.
Aerospace-grade boron fiber must undergo a rigorous series of tests that assess tensile strength and elastic modulus. To produce the composite tape, the fiber is fed into a 1250-spool creel in which the fiber is collimated and precisely spaced, then combined with the epoxy resin film. The typical products shipped to aircraft companies are 500-foot long, 6-inch wide prepregged tapes.
A new application for boron fiber is used in space structure components for optical imaging. Boron is the only fiber with a positive coefficient of thermal expansion (CTE) that can be hybridized with a high-modulus graphite fiber and provide composite components that have zero CTE with stiffness as high as 56 Msi.
Another high-growth application is hypersonics. According to Michael Griffin, the Undersecretary of Defense for Research and Engineering, the development of hypersonic capabilities is the Defense Department’s “highest technical priority.” The government-funded budget for hypersonic development has grown from $85.5 million in 2017 to $256.7 million in 2019, with even higher growth rates projected in the next 5-10 years in both funding and jobs. SMI’s boron fiber is already being considered for some of these applications.
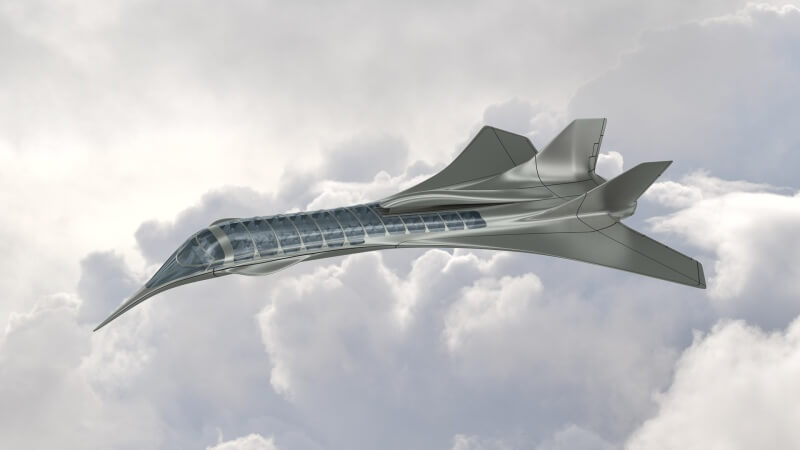