The Rise of Boron Nitride: Is this the New Carbon?
Boron nitride is a versatile compound with applications ranging from electrical insulation to cosmetics. But in recent years, this compound has been recognized as a potential successor to carbon in nanotube science.
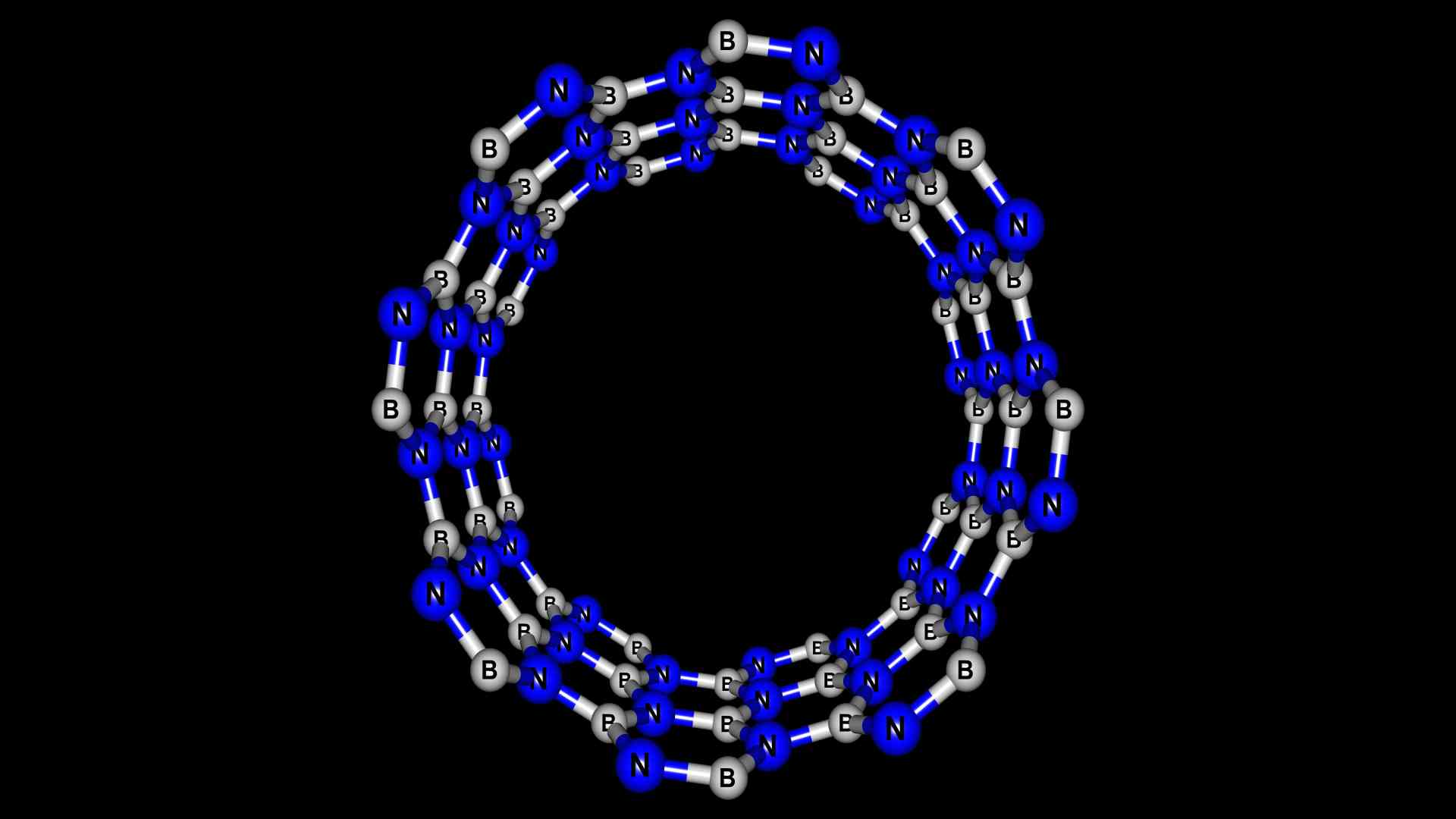
Boron nitride
Synthesizing Boron Nitride Nanotubes
Hexagonal boron nitride, a single-substance material called white graphene, is highly versatile. It has similar properties to carbon-based graphite in terms of molecular weight and strength and has a transparent appearance.
Engineers from MIT and the University of Tokyo created centimeter-scale structures from hexagonal boron nitride. These structures are visible to the naked eye and stuffed with tens of trillions of hollow aligned fibers or nanotubes.
Because hBN is transparent and electrically insulating, it can be integrated into boron nitride nanotubes and uses transparent windows to insulate detectors inside electronic devices.
The research team also looked to incorporate nano-fibers into membranes for water filtration and blue energy, a renewable energy principle in which electricity is generated by ionic filtration of seawater into clean water.
Aligned Boron Nitride Nanotubes
The findings published in the journal ACS Nano are paving the way for the mass production of aligned boron nitride nanotubes (A-BNNTs). Researchers use the technique to create bulk-scale clusters of these nanotubes, which would be coupled with other materials to create bigger, more powerful, more heat-resistant composite materials, such as those used to defend space formations and hypersonic aircraft.
MIT Professor of aeronautics and astronautics, Brian Wardle, compares the team’s findings to a decades-long search for producing carbon nanotubes.
Long, thin carbon nanotubes were first discovered in the early 1990s. Since then, scientists have been perfecting the process of creating these nanotubes in bulk quantities. However, it has proven to be a difficult task.
Aligned Nanotubes
As researchers continue investigating the potential of two-dimensional materials, hexagonal boron nitride has emerged as a significant player. hBN, like graphene, is made up of a regular pattern of hexagons, but these hexagons are made up of alternating boron and nitrogen atoms.
Researchers discovered that hBN sheets have exceptional power, stiffness, and resilience at extreme temperatures. When these sheets are rolled into nanotubes, their properties are enhanced even further, especially when the nanotubes are closely aligned, such as tiny trees in a tightly packed forest.
Wardle says that aligning the nanotubes makes it easier to utilize boron nitride nanotube properties in bulk quantities to create physical composites, devices, and membranes.
In 2020 at the University of Tokyo, Rong Xiang and colleagues discovered the ability to create high-quality boron nitride nanotubes by developing a forest of a few micrometers long carbon nanotubes.
They used the conventional chemical vapor deposition method and layered it with boron and gaseous nitrogen precursors. These are then solidified onto the carbon nanotubes at high temperatures to produce high-quality hexagonal boron nanotubes.
Burning Scaffolds
Wardle and Acauan’s latest study broadens and scales Xiang’s approach, expelling the underpinning carbon nanotubes and placing the long boron nitride nanotubes to remain by themselves.
Wardle’s group, which has spent years concentrating on the fabrication of high-quality, aligned clusters of carbon nanotubes, was discussed. The researchers were investigating ways to tweak the pressures and temperatures of the chemical vapor deposition method to eliminate the carbon nanotubes whereas keeping the boron nitride nanotubes unchanged in their ongoing work.
The team eventually discovered a combination of pressures, temperatures, and precursor chemicals. They initially replicated the measures taken by Xiang to generate the boron-nitride-coated nanotubes using many processes.
They also discovered clear crystallites in the microscopic examination, indicating that boron nitride nanotubes are highly quality. Furthermore, the structures were concentrated.
To prove the versatility of their methodology, the researchers developed bigger carbon-based structures such as a carbon fibers’ weave, a mat of fuzzy carbon nanotubes, and buckypaper sheets of randomly distributed carbon nanotubes.
Before burning the underpinning carbon, they layered carbon-based specimens with boron and nitrogen precursor chemicals. In every demonstration, they were given a boron-nitride scale model of the actual black carbon scaffold.
They also demolished BNNT forests, resulting in horizontally aligned fiber films, a favored configuration for integrating into composites.
Wardle and his team also worked on fibers to strengthen composite materials for space and hypersonic applications, window panes, and optically transparent devices.
Research Contributions
ANSYS, Airbus, Boeing, Lockheed Martin, Embraer, Saab AB, and Teijin Carbon America contributed to this investigation through MIT’s NECST (Nano-Engineered Composite Aerospace Structures) Consortium.