Ford Motors Boron Steel Bodywork
Automotive makers, including Ford, are taking advantage of boron’s high tensile strength to build stronger, safer, and lighter cars. Boron steel is a crucial ingredient in the Ford Fiesta’s pillars and structural elements and its other car brands. Boron steel is steel alloyed with small amounts of boron. It is four times higher than the average high-strength steel.
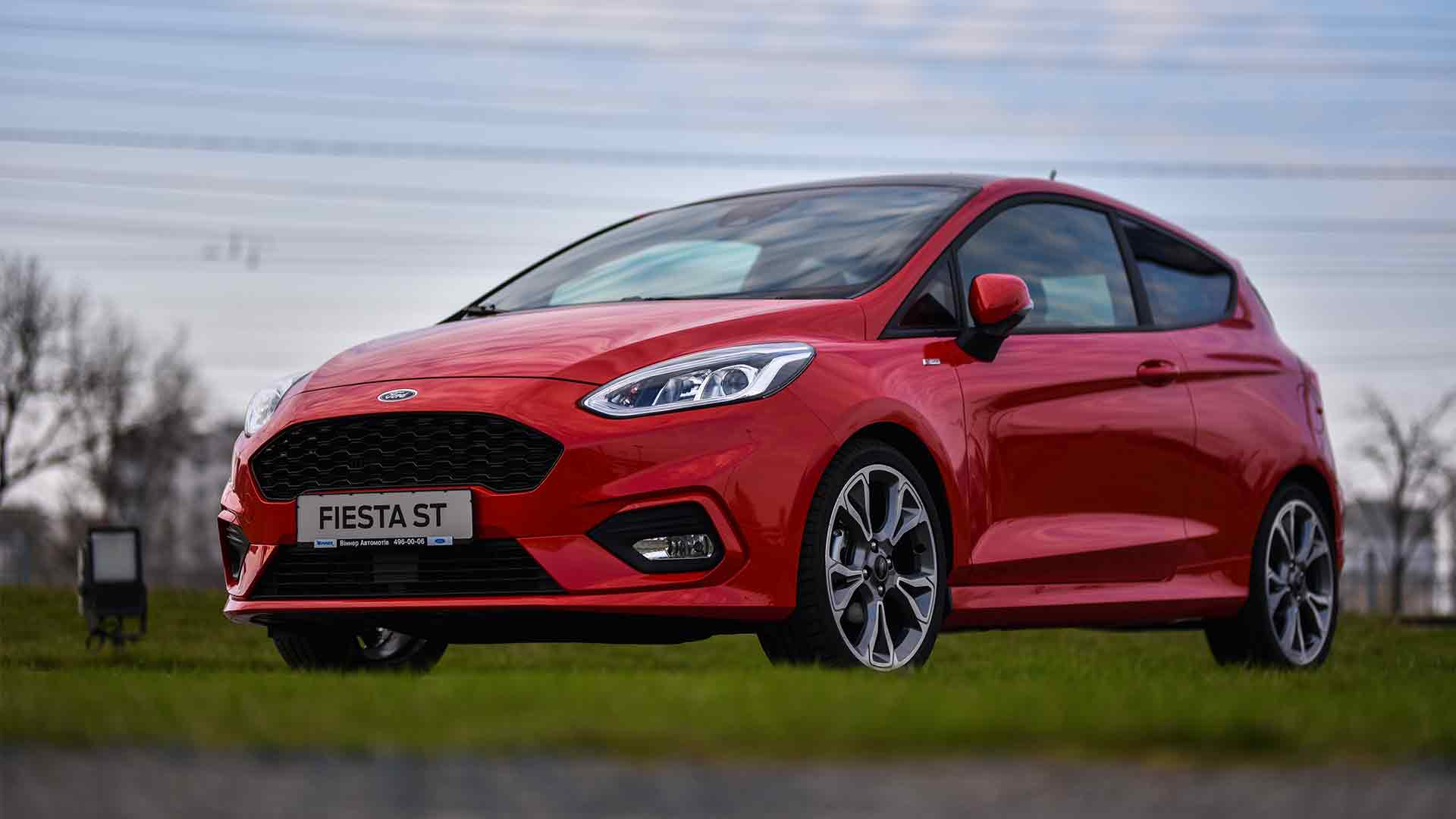
Ford Boron Steel
Boron Steel
Boron, a naturally occurring element, has many applications. Boron steel is steel alloyed with small amounts of boron. Boron steel can be made by adding small amounts (from one-tenth to 1%). This increases the alloy’s toughness. It is used extensively to make ultra-high-strength steel (UHSS). Boron steel’s yield point is between 1,350-1.400 N/mm2 (roughly 16,000 – 23,000 psi). This is four times higher than the average high-strength steel. It is widely used in automobiles. However, the process of making it takes away some steel’s workability properties, like being able to cut.
Blendtec Test Fails to Break Boron Steel down
Ryan Dembroski of Milwaukee, Ford Fiesta Movement agent, took a trip recently to the “Will It Blend?” studio in Orem, Utah. They tried to blend a part of the ultra-high-strength boron steel for the Blendtec Total Blender test.
Tom Dickson, the founder of Blendtec and host of the popular YouTube videos, fortunately, or unfortunately did not manage to crack, cut, or even crush the steel. Considering he could decimate different objects like Apple iPhone, marbles, and magnets, this is a shame. Perhaps this is not the most scientific of tests but shows boron’s strength as an ingredient in steel and aluminium and it is used to protect automobile drives and passengers. Boron strengthens not only car parts but also provides tensile strength in aerospace structures, golf clubs, and fishing rods.
Boron Steel in Automobiles
Automotive manufacturers have responded to new vehicle safety legislation and higher fuel prices in part by increasing car body stiffness and reducing weight. It has been a good thing for safety and fuel economy. These goals have been achieved by bringing together engineering, materials development, and manufacturing. Advanced steels, new forming processes, and new press concepts have been adopted to reduce weight and improve crashworthiness. Boron steel plays an essential role here.
Boron steel is extremely strong, but it is also very light. The car industry has long been interested in using boron as an alloy. Making boron-based steel can be done with less expensive materials than using a different alloy. It is generally used to add strength to the sill, roof, center posts, chassis, door strengthening bars, safety bars, inner pillars, dash panels, and dash cross-members. Boron can be effective even at low levels- 30ppm of boron can replace 0.4% Cr, 0.5% C or 0.12% V. Also, 30ppm of boron has been shown to increase low-alloy steel’s hardening depth (+50%). In SAE steel, a single molecule of a boron compound provides the same level of strength enhancement as a single atom of the more expensive elements.
European vehicles were the first to see boron steel (dash cross-member of the 2002 Porsche Cayenne SUV and safety bar around rear seats on 2003 Porsche Boxster), door strengthening beams on 2003 Porsche 911 Carrera, inner center pillars 2003 Mercedes-Benz E Class). Volvo uses the most boron steel (Bumper reinforcements, door supporting beams, seat recliner brackets for the 2004 Volvo S40 sedan, and 2005 Volvo V50 station wagon). Additional uses of boron in the 2003 Volvo XC90 SUV include the windscreen pillars, gussets in center pillars that meet with the roof sill and side channel, and the rear body panels. In 2004, boron steel was used by most vehicle manufacturers worldwide.
Research into Boron Steel
‘Hot stamped’ mild carbon-manganese-boron steel 22MnB5 has become commonplace in the body structure of the European vehicle over the past decade. Hot stamping produces an ultrahigh-strength martensitic microstructure resistant to abrasion (proof strength y1200MPa, ultimate tensile force y1500MPa), which allows for downgauging without compromising crash performance. New grades are required to meet the demands of downgauging. Recent research has led to the discovery of 38MnB5, a novel grade. 38MnB5 was hot stamped and showed a proof strength of more than 1400 MPa and ultimate tensile strength of over 2000 MPa. The automotive industry saw the new grade 38MnB5 as a significant weight and downgauging option due to its incredible strength.
Another study examines the possibility of using 20MnB5q, the boron micro-alloyed steel, to assemble body components. The steel is examined to see if it can be deformed without becoming globulised. Instead, it must be chilled in flux and then normalized. This will allow for a finer structure that tends to globulise. This research was done on samples of 20MnB5q native steel compared with samples from bars imported from the same French and Finnish origin. This research will continue to improve manufacturing technology for the 20MnB5q steel grade.
Boron Steel in Ford Fiesta and Other Models
The leading car manufacturer, Ford, uses boron and other ultra-high-strength lightweight steels. They are used in applications in different structural parts on their existing models, including Ford Taurus, Transit Connect, Flex, Mustang, F150, and Focus, as well as in Lincoln MKS. Boron steel is also a main ingredient in the 2011 Ford Fiesta to act as a protective agent for the occupants in case of a collision.
The body structure of the Ford Fiesta includes a high level of cold and hot high-strength steel. This steel takes up to 50 percent of the car model’s body structure which includes different grades like very high-strength, dual-phase steel, and ultra-high-strength aluminized boron steel.
However, the Fiesta structure is very lightweight even with all the additional strength. This is another most significant plus point of boron. Therefore, we can see that advancements in safety are possible with manageable fuel economy and CO2 emissions.
Fiesta Reinforcement
Structural strength and reinforcement are essential for crashworthiness and, the high-strength steels just offer that for the Ford Fiesta. The strength helps the floor structure, front rails, beams, and the model’s body-side reinforcement to provide the best protection against side impact.
It is possible to produce a strong B-pillar section and a strong rocker section fore and aft using high-strength materials. Additionally, you can also transfer the impact loads to the other side of the car through under-body cross members. It will help to increase the dissipation due to side impacts. The side intrusion can be avoided using the integrated body-side reinforcement in case of a collision. Therefore, the body structure can handle the consequences of other impacts effectively. It doesn’t matter if they are frontal, offset, or rear.
A slim A-pillar is a vital element of the body-side reinforcement. It forms the exterior front part of the vehicle’s roof arch, which is very modern. You can also find the intrusion-resistant B-pillar, the rocker panels, or lower rails that can manage the rocker bafflers, side roof arch as well as the lower A-pillar. These are the individual high-strength elements that are an essential part of the Ford Fiesta. They come together as a mini assembly during the manufacturing itself.
This assembly process will provide great joint strength and a very efficient body structure. In today’s world, an element like boron provides exceptional applications in almost every industry. Their role in Ford Fiesta and other models leads to enhanced safety for the occupants.