Tensile Strength in Boron Alloy Steels
Boron alloy steels with high tensile strength can be carbon, low alloy, HSLA, and carbon-manganese. Boron’s high neutron absorption means that stainless steels used for the nuclear industry, for instance, are often enriched with boron. It can be as high as 4% but is more commonly 0.5 to 1 percent.
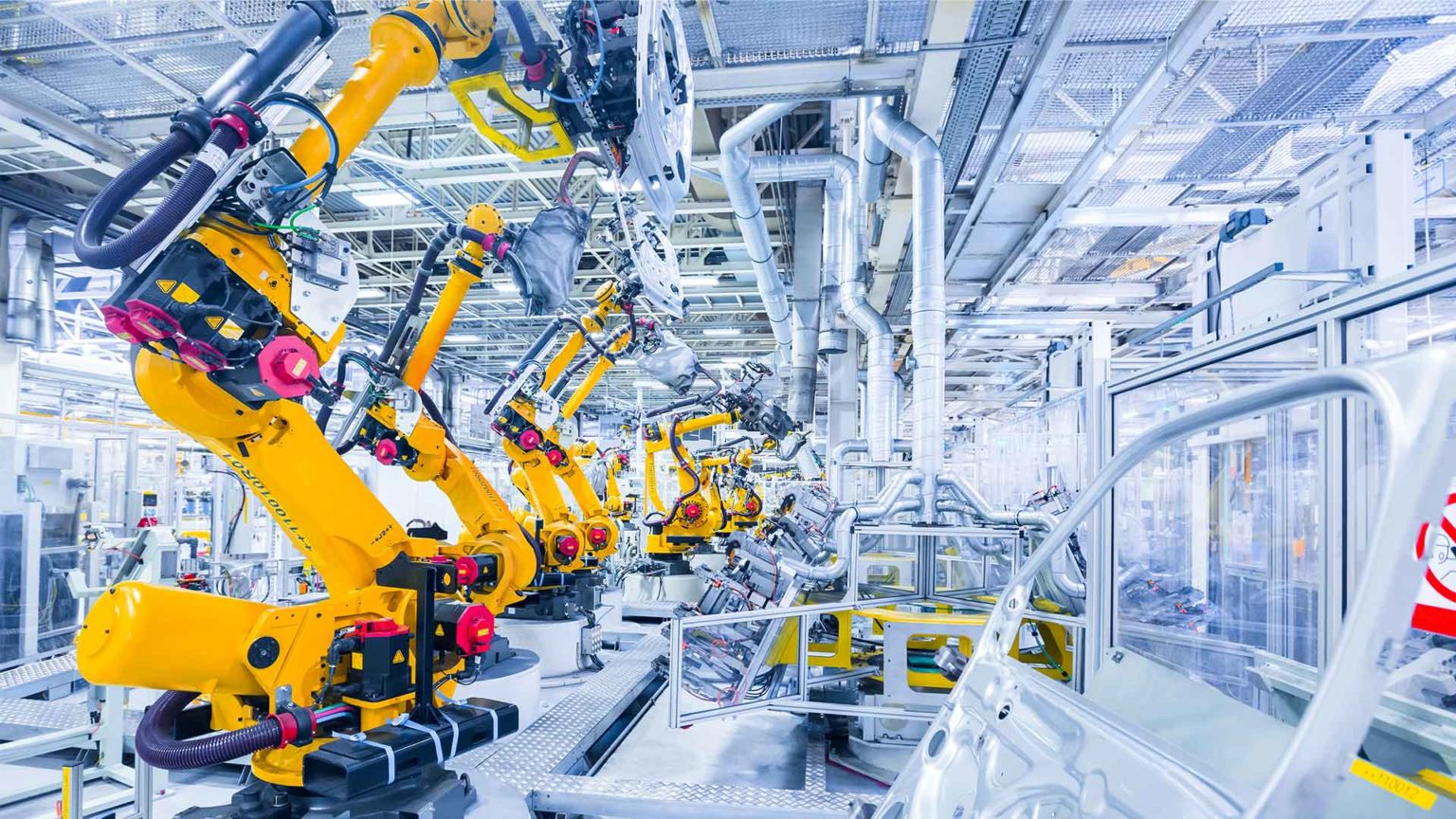
Boron Steel
Boron Steel is an ultra-high-strength steel used by automobile manufacturers, along with low-alloy and dual-phase steels, to help protect you while still passing on fuel savings. It can be melded into thinner components than normal steel, it’s lighter while still remaining super strong and stiff. Their high yield and tensile strength allow for complex shapes that can be wielded in key areas, such as pillars and bumpers.
Boron steel is also used in the door intrusion beams of all Ford vehicles to help protect passengers in the event of a side impact and other key areas on specific models, depending on their size and usage.
For automotive use, flat boron steel is hot stamped in cooled molds using austenitic states (obtained by heating to 900 -950C). The typical 22MnB5 steel shows a 2.5x increase of tensile strength from 600MPa as a result. You can stamp in an inert atmosphere or abrasive scales. Alternatively, you can use a protective Al-Si coating.
The introduction of aluminized steel with high tensile strengths uses hot stamped mild manganese-boron steel (22MnB5), which has proof strength ultimate tensile force 1500MPa. This has allowed for weight savings in the European car industry through down gauging.
New Hot Stamping Process for Boron Steels in Automobile Industry
Hot stamping via a new low-temperature hot-stamping process that includes pre-cooling for 22MnB5 Boron steel has been demonstrated in 2019 The International Journal of Advanced Manufacturing Technology volume 105, pages 669–682 (2019) Cite this study. It uses an advanced in-house prototyping machine and both 50mm and 64mm depths.
Experiments with hot stamping were conducted for various stamping temperatures and forming speeds. Post-form inspection of hot-stamped parts was done to determine the potential benefits of hot stamping at low temperatures. In-die quenching tests were also used to assess the potential advantages of hot stamping at lower temperatures. The new B-Pillars have a higher final thickness distribution than the old process. This is in addition to the improved mechanical properties and microstructures. The new process allows for increased productivity due to significantly lower in-die quenching.
Hot Stamping
North American and European car manufacturers overall specify hot-stamped parts for their new vehicles to take advantage of the superior strength achieved by hot forming and quenching. Hot stamping has shown exceptional development and growth for several structural parts, including front and rear bumper beams, A-pillars, B-pillars, roof rails, side rail members, tunnels, and door beams using boron steels.
Nissan – Leader in Boron Steel Usage
Nissan has expanded the use of Advanced High Tensile Strength Steel (AHSS) to up to 25 percent of the vehicle parts installed in its new production models. Nissan made use of advanced high-tensile strength steel starting in 2017 as one of its initiatives to help reduce vehicle weight.
The company has developed* 1.2 gigapascals (GPa) Ultra High Tensile Strength Steel with High Formability for use in the Infiniti Q50 2013 model. Before this latest tensile strength steel came out, it had been difficult to use high tensile steels for vehicle parts with highly complex shapes.
With the active adoption of 1.2 GPa ultra high strength steel, which is one grade among several types of advanced high tensile strength steels, Nissan looks to increase the adoption rate of AHSS as far as 25 percent of the gross weight of the parts installed per vehicle, aiming to reduce the weight of Nissan’s vehicles by 15 percent with corresponding body structure rationalization.