Coating of Protective Shield for Neodymium Magnets
Neodymium magnets are known for their strength, comprising three elements Neodymium, Iron, and Boron. They are also known as Neodymium Iron Boron Magnets or NdFeB magnets. These magnets create a stronger magnetic field than other ceramic or plastic-coated magnets. Still, Neodymium Iron Boron Magnets can be corrosion prone due to their vulnerability to oxygen and moisture contact over time. Fortunately, there are some coatings available that help neodymium magnets prevent corrosion.
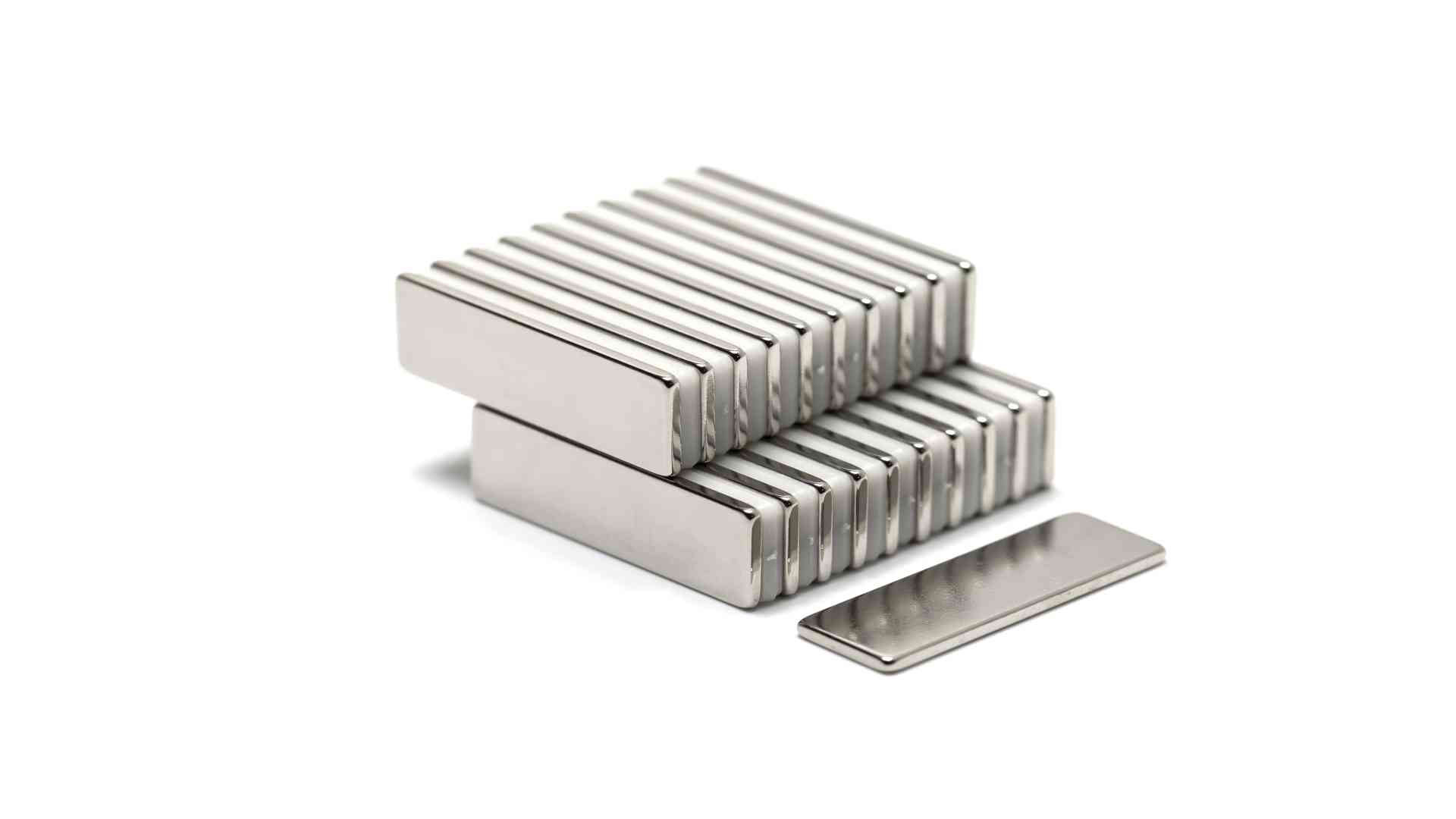
Neodymium magnets
Types of Neodymium Magnets Coating
When it comes to coatings, various options are available to suit the environment or application. Below is a list of several popular coatings and their effectiveness in certain environments:
1. Nickel
Nickel coating is an excellent choice for many applications. It offers great protection against wear and abrasion, making it ideal for indoor use.
Additionally, it can be used outdoors, provided it is kept from rain and humidity. Its three-layered structure (nickel-copper-nickel) provides a strong, durable coating that will last many years without needing to be refinished or replaced.
2. Zinc
Zinc coating is an effective way to protect magnets against corrosion. Its single-layer protection makes it ideal for parts frequently exposed to the elements, creating a white coating that acts as a barrier to keep the underlying metal safe from damage.
3. Gold
The gold coating is one solution for improving the look of neodymium magnets without affecting their performance. It also has protective properties that act as a barrier against oxidation and help extend the magnet’s life.
4. Epoxy
Epoxy coating for neodymium magnets provides an excellent barrier against salt air and water. These magnets can withstand harsh outdoor conditions and provide a reliable hold over long periods.
However, the epoxy coating is quite delicate and needs to be handled carefully during assembly to avoid scratches or other damage.
5. Plastic
ABS plastic coating is a great option for neodymium magnets because of its high corrosion resistance. To create this protective shell, an injection molding process needs to be used in which heated plastic is injected into a mold at high pressure, forming a protective shell around the magnet.
The shell needs to be thicker than other coatings to flow adequately during the injection process. The end result is highly robust and effective from any elements that may come into contact with them.
6. Teflon
Teflon is an excellent material for magnet shells because of its resilience and corrosion resistance. Its properties make it ideal for the extreme environments that magnets are often subjected to. To create this shell, an injection molding process is used. This ensures that each enclosure fits perfectly around the magnet and seals out any moisture or contaminants.
7. Chrome
Chrome coating is often used on neodymium magnets to improve the appearance and provide limited protection from corrosion in ambient air. Chrome plating is not as effective as nickel plating when it comes to protecting the magnet, but it offers a more attractive look. Additionally, chrome coating does not protect from humidity, water, or saltwater.
Which is Better for Neodymium Magnets: Nickel or Zinc Coating?
Choosing the right coating for these powerful magnets is critical to their performance and longevity. Nickel and Zinc are two popular options for neodymium magnet coatings.
1. Price
Zinc coating is affordable compared to nickel coating. Zinc provides a protective layer on metal surfaces that prevents corrosion, making it ideal for steel and other metals used in manufacturing.
Zinc’s price point makes it attractive for many industrial and everyday applications. Nickel plating is much more expensive than Zinc but offers enhanced protection against wear and tear, making it the preferred choice for more specialized applications.
2. Polishing
Compared to nickel-plated neodymium magnets, zinc-plated ones are not as shiny or aesthetically pleasing due to their dull finish. Nickel is much better at polishing than Zinc, making the finished product brighter in appearance – just like the color of our coins!
3. Performance
The temperature resistance of Zinc-coated magnets is poor compared to Nickel-plated ones.
Nickel has a much higher melting point than Zinc, so it can withstand higher temperatures without deteriorating. In addition, the conductive properties of Nickel make it an ideal choice for electromagnetic applications.
4. Anti-Rust Properties
Zinc coating has general rust-resistant properties, while nickel coating provides superior rust protection. Depending on the particular environment in which the magnets will be used, you may find one type of coating more appropriate.
Surface Treatment Comparison Chart
Surface treatments can extend the life of a neodymium magnet by increasing its resistance to corrosion and abrasion and providing additional protection against erosion caused by exposure to moisture or chemicals. The following table shows some of the most common surface treatments used on neodymium magnets:
Effect on environment Electric plating Thermal spraying Deposition Electrodeposition Parylene coating Hi-DEN COAT
Process Wet Dry Dry Wet Dry Dry
Selection of object to be coated Large objects are difficult Large objects are difficult No problem Small objects are difficult Large objects are difficult No restrictions
Choice of color Only metal colors None Only metal colors Fairly large None Fairly large
Hydrogen embrittlement Potential risk None None Potential risk None None
Effect on environment Very large Small Small Small Small Small
Deposition adhesion Strong Strong Weak Strong Weak Strong
Insulation Only certain materials Only certain materials Only certain materials Yes Yes Yes
Machining after processing Not possible Not possible Not possible - Not possible Possible
Deposition speed Slow Fast Slow(limited) Fast Slow Slow
Productivity Good Difficult Difficult Good Good Good
Addition of modifying material
(Specific to properties of various types) Not possible Not possible Not possible Not possible Not possible Possible
Adherend strength Weak Very weak Weak Strong Weak Strong
Source: Magfine
The Importance of Corrosion Protection for Magnets
Corrosion protection is a vital factor in maintaining the strength and performance of Neodymium Iron Boron magnets. An uncoated magnet can rapidly deteriorate when exposed to environmental elements such as moisture or salt, causing volume loss of the magnetic alloy material and reducing its magnetic field.
To ensure consistent performance and reliability, it’s important to use a protective coating on any magnet exposed to environmental elements.
The type of coating chosen should depend on the environment and application requirements; for example, Neodymium Iron Boron requires more substantial protection than Samarium Cobalt due to its higher reactivity with salt and moisture.
Final Note
Magnets are unique creations with various uses. The neodymium magnets we use today are powerful and can be found in products worldwide. To keep them functioning at their best, it’s important to protect them from corrosion. Coating magnets can extend their life and keep them looking great for years.