Boron Fiber – High Performance Technology
Boron fiber, commonly known as boron filament, is an amorphous element of B5 by-product, representing a primary industrial usage of elemental (free) boron. Boron fibers are manufactured to improve rigidity in synthesized materials where glass fiber was previously primarily used to reinforce amalgamation in days gone by. Boron fibers compete with high-modulus carbon fibers which have higher stiffness and lower cost.
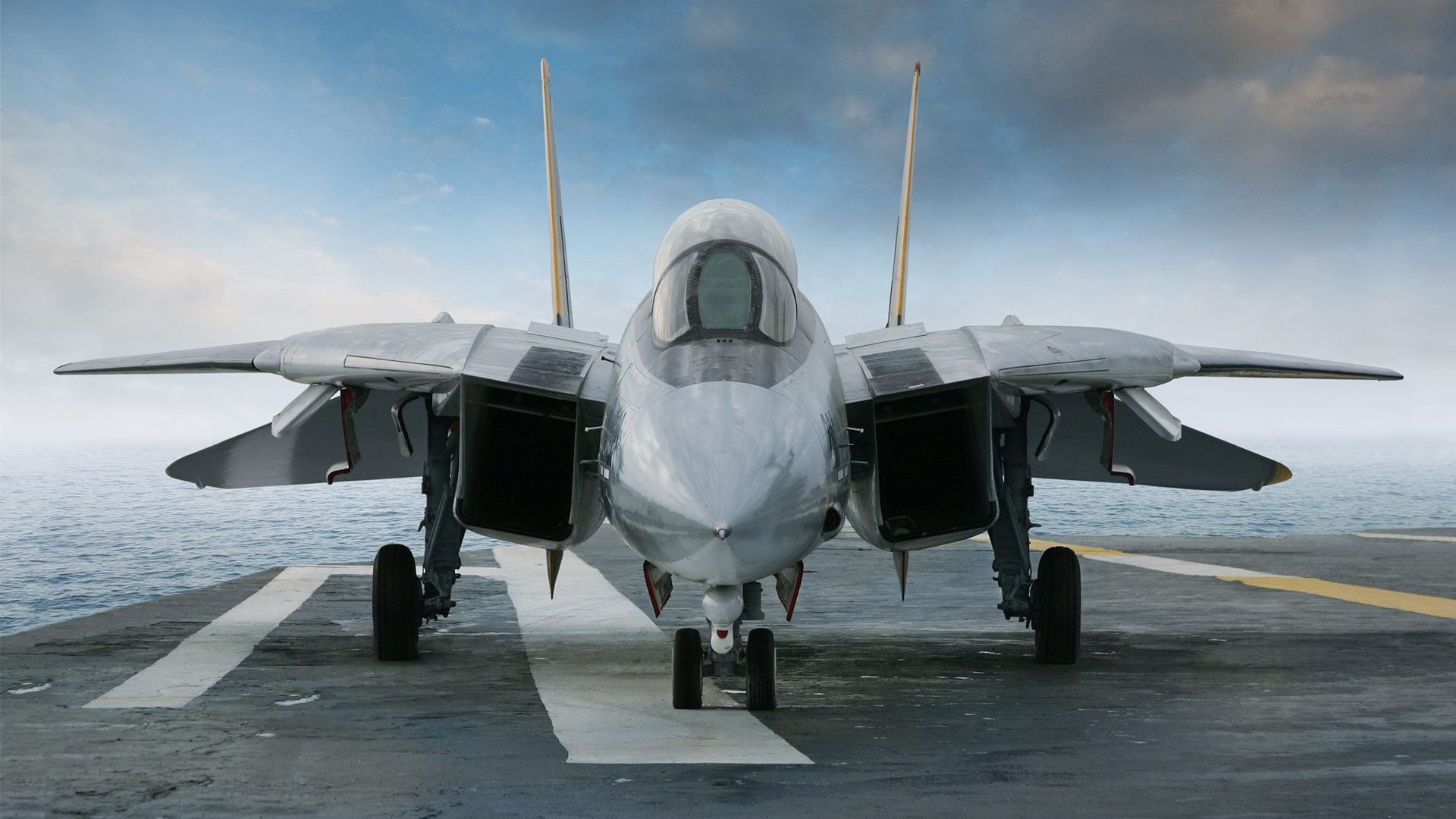
External Properties and Industrial Usage of Boron Fibers
Due to amalgam characteristics of boron fiber, complex internal stresses and defects such as voids and structural discontinuities indicate the presence of a core and deposition process. Hence, one would not expect boron fiber strength to equal the intrinsic strength of B5. The average tensile strength of boron fiber is 3-4 GPa, while Young’s modulus is between 380 and 400 GPa. The conventional use of boron fibers is for the formation of high tensile strength tapes, i.e. monofilament fiberglass tapes.Industrial Competence
Boron Fibre fabrication jump-started in 1959. Talley is applied in the process of halide reduction to obtain amorphous boron fibers of high strength. Since then, researchers have shown waxing and waning interest in using solid but light boron fibers as a possible structural component in aerospace and other structures. Alternative substances such as carbon fibers have proven to be more pliable and cheaper to work with in the past. One big challenge to the widespread use of boron Fiber is its high cost compared to other fibers. A significant portion of this high price is the cost of the tungsten substrate.Fabrication Methods
There are two methods involved in the fabrication of fiberglass from B5. At first, boron fiber is produced through the thermal decomposition of Boron Hydride. This method involves low temperature heating in the furnace with carbon-coated glass, used as substrate. The physical properties of boron fiber under this procedure are brittle because of the reduction in boron halide. 2BX3 + 3H2 ↔ 2B + 6HX , Here X is a halogen group : Cl, Br or I. During the process of halide reduction, the material rises to a high temperature of around 1000 º C – 13000º C; To mitigate this, a refractory material with a high melting point, in tis case tungsten, is used as a substrate. This method is preferred despite the disadvantage of being a relatively high-density substrate (the density of tungsten is 19.3 g cm -3). The upside is that this process gives boron fibers which are remarkably high grade and consistent in quality. Several firms produce boron fibers commercially using this process. In the process of BCI3 reduction, an exceptional tungsten wire (10-12 micron diameter) is pulled into a different reaction chamber at one end via a mercury seal, and out at the other end through another seal. Mercury sediments are electrical contacts providing resistance; avoiding overheating of the substrate wire. When gases (BCl3, + H2) pass through the reaction chamber, they burn the tungsten wire substrate. The borosilicate reactor can be one, multi-phased, vertical or in a horizontal reactor. There is a critical temperature needed for attaining Boron Fiber with the most favorable properties and structure. The required amorphous form of boron occurs below this critical temperature, while above this temperature, undesired crystalline forms of boron form. With the substrate wire, the stationary elements in the reactor will obtain this critical temperature, which is about 1000º C. In a systematic system where the wire is moving, this critical temperature is higher, increasing with the rapidity of the wire. The Fibers are formed in the region above the dashed line, which is relatively weak because they contain unpleasant forms of boron crystallization. Boron is sedimented at the right critical temperature and wire-speed in an amorphous state of matter. The speed of the wire is drawn out from the reactor, the higher the temperature. Indeed, the higher the wire drawing speed, the higher the production rate and the lower the cost. The B5 element sediments on a carbon monofilament of about-35 micron diameter substrate cover the carbon substrate by a film of pyrolytic graphite, accommodating the growth strains that result during boron deposition.Fabrication Procedure
A laser commercially manufactures boron fibers assisted by a chemical vapor deposition process involving a mixture of boron trichloride and hydrogen. The substrate is introduced through a mercury-sealed gas inlet and drawn through the reactor. At the same time, boron trichloride and hydrogen are presented at the top of the reactor. When the tungsten is kept through the reactor, the hydrogen forms boron on the substrate, mixing with trichloride. The unwanted gases of boron trichoride, hydrogen chloride by-product, and inactive hydrogen are exhausted through an outlet port at the bottom of the reactor. These gases are then either dumped or recycled for future production use. Boron Fibers of nominal diameter in the range of 0.1–0.2 mm are produced. They are characterized by low density, high tensile strength, and high modulus of elasticity. The boron filament of diameter is distinctively 0.004 inches (100 micrometers), which passes through another mercury pool. As it exits, the reactor and later winds up on a take-up spool. In-line optical scanners monitor the fiber diameter before take-up. With a few adjustments, thre rate can be increased or slowed down as needed by a feedback loop to ensure the diameter is within the desired requirements. An unusual feature of boron fiber is its rigid “corn comb” structure, which ensures a mechanical clutch between the boron glass fiber and resin material. The aerospace-grade boron fiber must undergo a rigorous series of tests that assess tensile strength and elasticity. Therefore, to produce the composite tape, the glass fiber is fed into a 1250-spool reel. The glass fiber is collimated and precisely spaced, then combined with the epoxy resin film. The specific products are shipped to aircraft companies – 500-foot long, 6-inch wide pre-pregged tapes. Boron fiber prepreg looks and handles like graphite fiber-based prepregs and is amenable to many manufacturing processes. A schematic of the process is give below.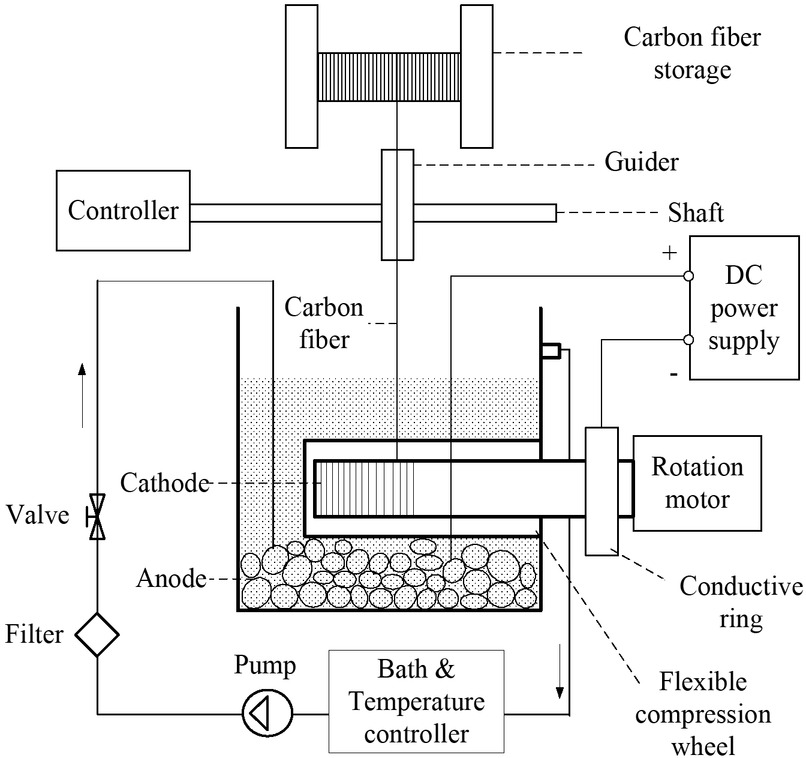