Electric Car Batteries
Electric Car Batteries are rechargeable batteries that power electric cars, bikes, and scooters. They are specifically designed to give power over a sustained period and are deep cycle batteries. Lithium-ion batteries are usually used in EVs. Their relatively high power-to-weight ratio makes them ideal for powering electric cars and bikes.
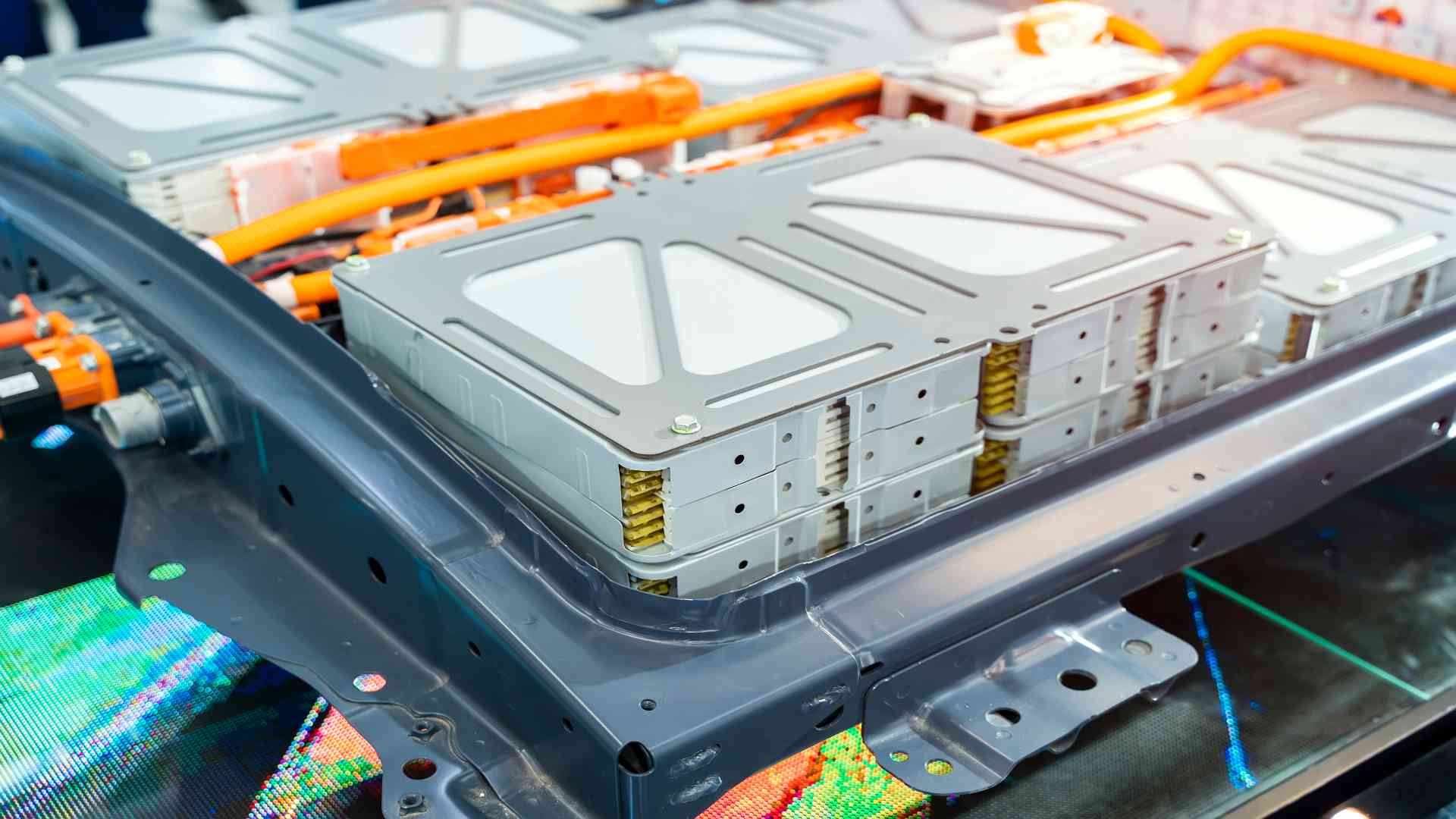
Electric Vechile Batteries
How Does an Electric Car Battery Function?
Where internal combustion-engine cars obtain their energy from gasoline or diesel combustion, an electric vehicle draws power directly from a large battery pack.
These are similar to a larger version of the lithium-ion (Li-ion) battery in your phone – EVs don’t use a single battery like a phone but rather a pack made up of thousands of individual Li-ion cells that work together. When the car is charging, electricity induces chemical changes inside the battery. These changes are reversed when it’s on the road to generate electricity.
The Technology used in Electric Car Batteries
Electric car batteries go through cycles of ‘discharge’ while driving and ‘charge’ when the car is plugged in. The amount of charge electric car batteries can hold decreases as this process is repeated over time. This reduces the range and time required between charging journeys. The majority of battery manufacturers provide a five to the eight-year warranty on their products. Current predictions suggest that electric car batteries will last between 10 and 20 years before needing to be replaced.
The connection between a battery and the car’s electric motor is surprisingly simple – the battery connects to one or more electric motors, which drive the wheels. When you press the accelerator, the car immediately supplies power to the motor, gradually absorbing the energy stored in the batteries.
Because electric motors also function as generators. When you take your foot off the accelerator, the car begins to slow down by converting its forward motion back into electricity – this occurs more strongly if you apply the brakes. This regenerative braking recovers energy stored in the battery, thus extending the vehicle range.
Electric Car Battery: Lithium-Ion Battery
Lithium-Ion batteries are lightweight, high-capacity batteries commonly used in electronic devices such as laptops, mobile phones, cameras, video game consoles, GPS receivers, digital music players, and electric cars and bikes.
These batteries have a high energy density. This means that battery manufacturers will be able to save space by decreasing the overall size of a battery pack.
Lithium is also the lightest of all metals, which further contributes to the compactness of these batteries. Another key benefit of lithium-ion batteries is that they do not contain lithium metal. Instead, they rely on ions to create an electric charge. This makes them much safer than other batteries that use lithium metal, which can be highly volatile.
Use of Boron in Lithium-Ion Batteries
- Lithium-ion batteries are used in portable electronics. These batteries rely on graphite as an anode material due to its low cost and good properties, such as high electrical conductivity and stability. However, lithium deposition can cause issues that lead to short circuits and safety concerns at high charge rates. Borate surface coating may safeguard against lithium deposition, improving the overall stability of the SEI, which serves as a boundary between electrode and electrolyte.
- One of the primary challenges of improving lithium-ion batteries is producing a highly ordered crystalline graphite structure through high-temperature heat treatment (which requires temperatures in the 3000°C range). Still, this process can be expensive and energy-intensive. However, adding borate before graphitization enhances electrochemical properties without increasing temperatures as high as with standard graphitization processes.
- For increasing crystallinity, boron is incorporated into the crystalline structure of graphite at higher temperatures that activate greater alignment and change the electronic structure. It acts as an electron acceptor resulting in a specific capacity of 437 mAh/g, higher than the standard maximum for pure graphite (372 mAh/g).
Recycling Electric Car Batteries
Although enabling a second-life application can extend battery life, electric car batteries must eventually be recycled. In many countries, BEV technologies lack a well-established recycling framework, making BEVs and other battery-powered electrical equipment a considerable energy expenditure, ultimately increasing CO2 emissions. Thus, there are five types of recycling processes currently in use:
- Pyrometallurgical Recovery
- Physical Materials Separation
- Hydrometallurgical Metal Reclamation
- Direct Recycling Method
- Biological Metals Reclamation
The pyrometallurgical process uses a high-temperature furnace to burn the battery materials with slag, sand, limestone, and coke to produce a metal alloy. The materials produced are metallic alloy, slag, and gases. The gases are evaporated molecules from the electrolyte and binder components.
The hydrometallurgical process separates the metal alloy into constituent materials. The slag, a metal mixture of aluminum, manganese, and lithium, can be reclaimed and used in the cement industry. This method is highly adaptable and relatively risk-free. It can work with a wide range of batteries because no pre-sorting is required. Furthermore, because the entire cell is burned, the metal from the current collectors could aid in the smelting process. The energy absorption can be reduced by burning electrolyte sand plastics due to the exothermic reaction. However, this process still necessitates a significant amount of energy, and only a limited number of materials can be reclaimed.
Physical materials separation recovers materials through mechanical crushing and using physical properties such as particle size, density, ferromagnetism, and hydrophobicity. Sorting can recover copper, aluminum, and steel casing. The remaining materials, known as “black mass,” are nickel, cobalt, and lithium.
The cathode materials must be crushed to remove the current collector for the hydrometallurgical process. The cathode materials are then leached by aqueous solutions to extract the desired materials from them.
As the name implies, direct cathode recycling extracts the materials directly, generating a cathode power that can be used as a new cathode pristine material. This method includes the extraction of electrolytes using liquid or supercritical CO2. The cathode materials can then be separated after the size of the recovered components is reduced.
The process of biological metals reclamation, also known as bio-leaching, employs microorganisms that selectively digest metal oxides. Recyclers can then reduce the oxides to produce metal nanoparticles. Although bio-leaching has been used successfully in the mining industry, this process is still in its infancy in the recycling industry, with plenty of room for further research.
Are Electric Car Batteries Safer?
Manufacturers of electric car batteries ensure that EV batteries are safe, installing smart management systems to prevent overheating and other issues. Batteries do get warm during charging and discharging, but cars are designed to keep them cool – high-performance EVs may have liquid cooling systems to assist.
Despite this, there have been a few instances of electric vehicles catching fire, but very few of these incidents were caused by battery failures. They’ve resulted from accidents that could have caused any car to catch fire, such as the 2013 case of a Tesla Model S colliding with a large piece of metal at high speed. In response to the incident, which resulted in a minor fire, Tesla CEO Elon Musk stated that Electric car batteries contain only about a tenth of the energy of a tank full of fuel, reducing their danger.
In fact, according to a 2017 study conducted by the US National Highway Traffic Safety Administration, the probability and intensity of fires caused by lithium-ion batteries were comparable to or slightly less than that caused by conventional vehicles. As more electric cars hit the road, we can be more confident that they are as safe as traditional vehicles.