Boriding: The Process Of Surface Hardening
Boriding is the process of adding boron to a metal or alloy. It is a thermochemical surface hardening method used on various ferrous, non-ferrous, and ceramic materials. This has the primary advantage of significantly improving metals and alloys’ wear resistance and hardness without compromising their ductility.
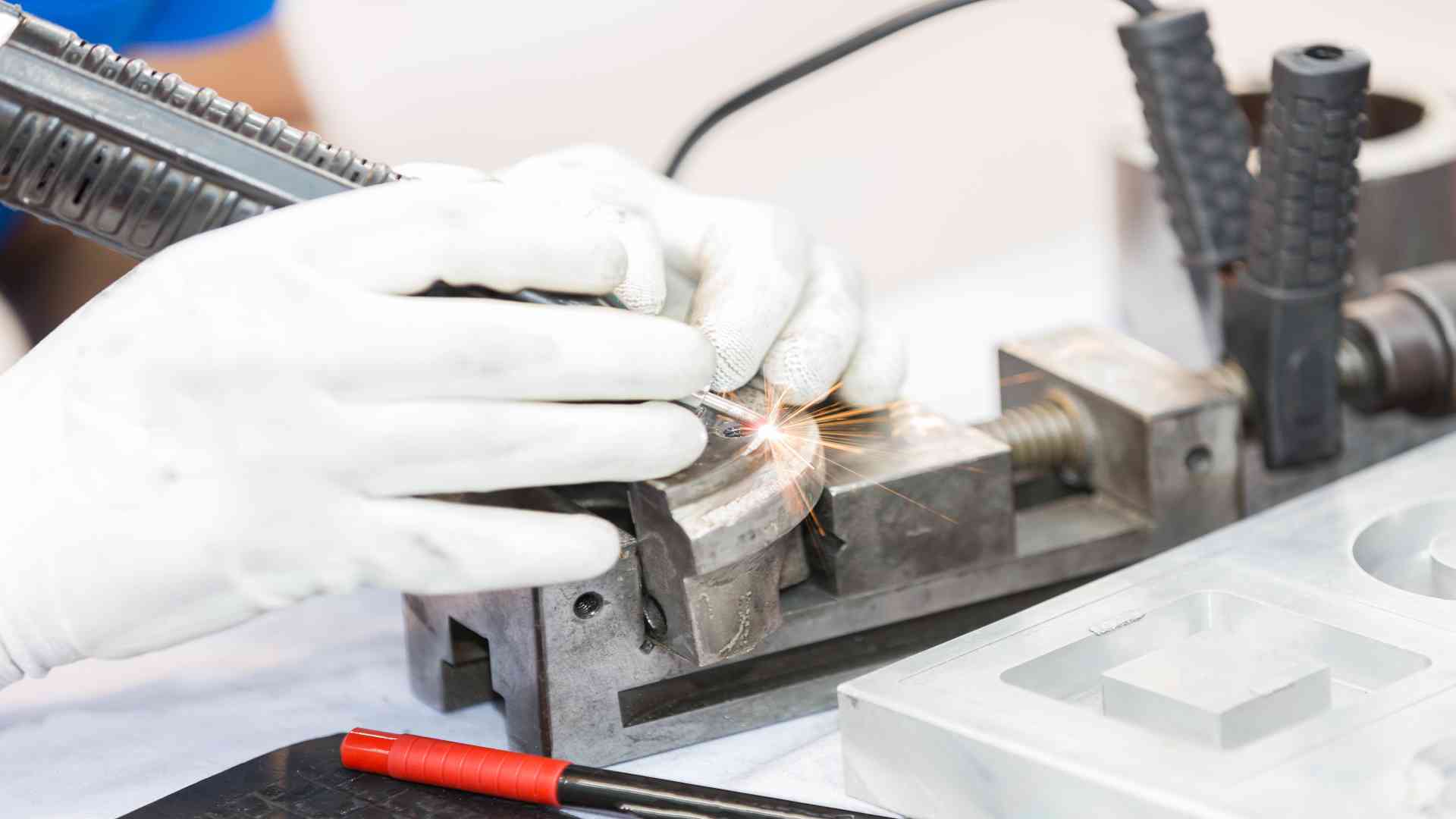
Boriding
Boriding
Boriding, also known as boronizing, is the method of diffusing boron atoms into the surface of a metal component to form a single-phase or double-phase boride surface layer. This surface layer is highly wear-resistant and can often outlast components treated with conventional thermal processing two to five times. It also prevents the workpiece from chemical attacks and cold welding.
Boron is used as a powder, paste, or granule, allowing for treating almost any type of workpiece, regardless of design. Boronizing is highly effective at corrosion resistance and can be used on mechanical engineering workpieces, valves, and power tools.
The process is achieved by packing the metal piece with a boronizing mixture and warming it at 900 °C. boronizing mixtures are typically boron carbide powder diluted with the other refractory materials. This method converts some of the Fe to iron boride, composed of two phases: FeB near the surface and diiron boride (Fe2B). Depending on the base material and treatment, layer depths can range from 0.001 to 0.015 inches (25.4 to 38 µm).
Boriding Advantages
Boriding is a surface hardening process that creates a uniform hardness layer from the surface to the diffused layer depth. The resulting hardness is many times greater than other surface hardening processes.
This combination of increased hardness and reduced coefficient of friction improves wear, abrasion, and surface fatigue characteristics. Other advantages include hardness retention at high temperatures, resistance to corrosion in acidic environments, reduced lubricant requirements, and a lower tendency to cold weld.
Boriding Applications
The process is performed on various ferrous materials, except aluminum and silicon bearing steels, such as structural steel, tempered, tool, ductile and sintered, stainless steel, cast steel, and air hardened steels.
Borided materials include nickel-based alloys, cobalt-based alloys, and molybdenum. Boriding a nickel alloy without compromising corrosion resistance results in an extremely hard surface wear resistance.
Steels that cannot be borided are nitrided and resulfurised steel.
Industries That Need Boronizing:
- Oil and gas
- Agricultural machinery
- Turbocharging
- Automotive
- Stamping
- Textile machinery
- Miling and crushing technology
- Extrusion
- Injection molding
Boronizing is often used on components that are subject to high levels of wear, such as valve components (gates, seats, stems, etc.), pump components (impellor housings, bodies, cylinders, etc.), agriculture equipment (harvesting combine cutters, crop transfer, separators, chopping components), and automotive parts (diesel engine oil pumps, gears).
It can also be used on stamping (dies and tooling) and textile (grooved drums).
Wear Resistance By Boronizing
Boronizing introduces boron in the form of powder, paste, or granules which is well suited to unalloyed and low alloyed steels. The diffusion rate and thus the thickness of the achievable boride layer decrease as the alloying element content increases. At the same time, alloying elements like nickel and chromium help to increase hardness and wear resistance.
Boronizing enhances the properties of various materials including cast iron, cast steel, most steel grades, and nickel-based alloys. However, it may not be suitable for materials containing silicon and aluminum. It may affect steels with high levels of these elements.
The boride layer, thus produced is extremely hard and has a significantly longer service life than other coatings such as nitriding, chrome plating, thermal spraying, carburizing, or plasma vapor deposition (PVD) coating. Borided surfaces are also more resistant to abrasive wear and cavitation.
Boronized surfaces have a lower friction coefficient, improving lubrication and reducing wear. Even at high temperatures of up to 1000 °C, the boride layer provides excellent urgency running properties in the event of a lubricating film break.
The Process of Boronizing
This is a two-step process that involves first reacting a boron-containing substance or compound with a metal part, followed by diffusion. This process results in the formation of a thin, dense boride layer. The boronizing reaction is typically carried out at elevated temperatures and times, depending on the desired final properties. After boronizing, the metal part will have increased resistance to wear and corrosion.
Boriding vs. Nitriding
Boriding and nitriding are thermochemical diffusion processes used to enhance mechanical properties and wear resistance. As the name implies, boriding uses boron to achieve this, whereas nitriding uses nitrogen.
While boriding can increase the hardness of material up to 2600 HV, nitriding can only achieve 950 HV for certain types of steel.
Nitriding is most effective on nitriding steels, whereas boriding is also used on steel grades containing nickel, nickel superalloys, and cobalt superalloys.
Boriding and nitriding are not coatings but rather diffusion treatments. This means that both treatments are much more permanent and can better protect the material. They will not peel or chip off as some coatings do.