Borates in Ceramics – Glazes and Enamels
Ceramics – Ceramic glazes and enamels – are applied to ceramic ware, sanitary ware, tableware, and tiles. Borates are used extensively in such enamels and ceramic glazes. Borates used include colemanite, ulexite, and several specialty borates, which provide efficient production and protection against the elements to the finished products.
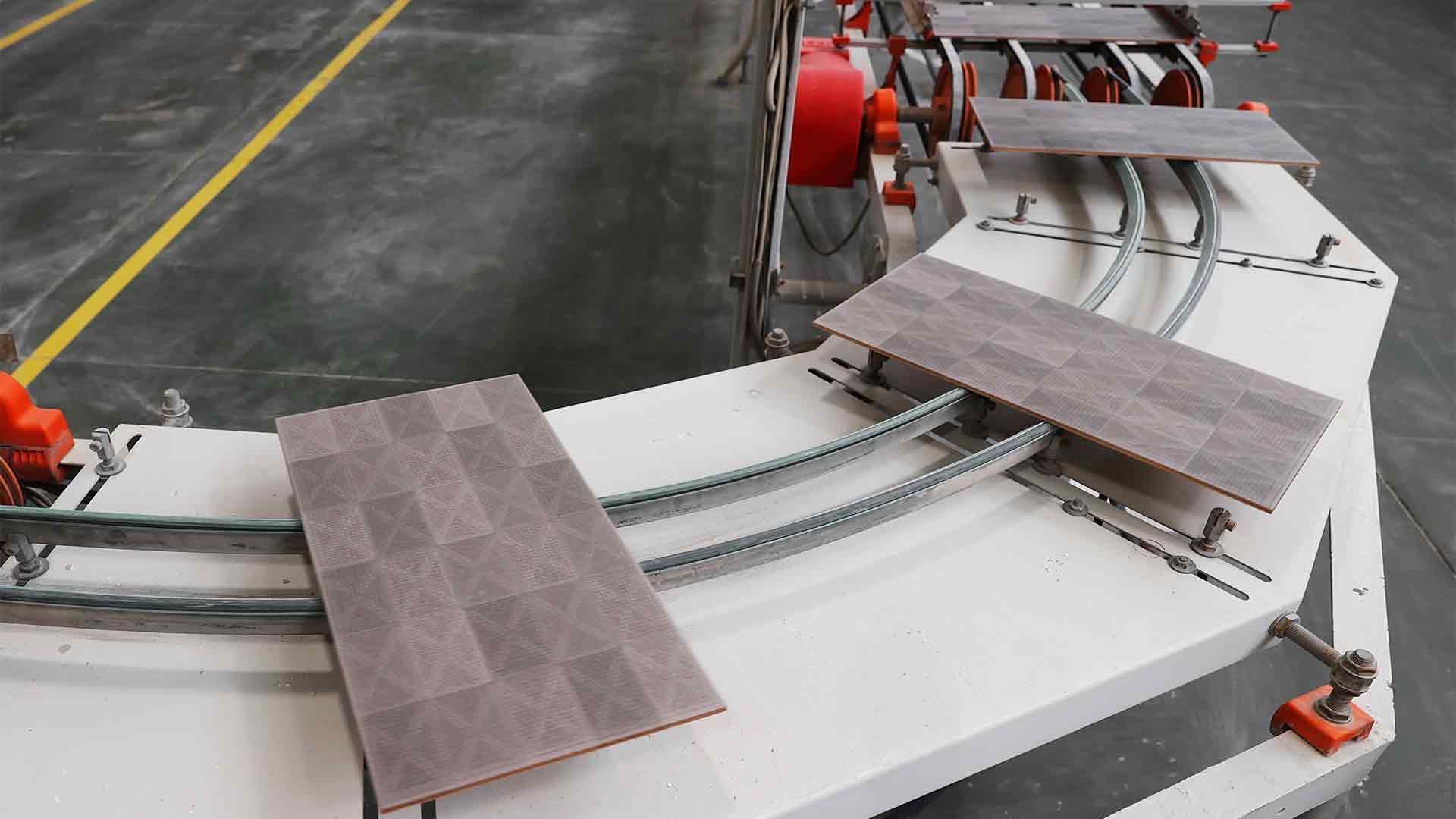
Boron in Ceramics
Borates in Ceramics
Borate compounds are regularly used in ceramic glazes and enamels to improve appearance, reduce firing times, glass viscosity, and lower surface tension. Borates also increase durability and resistance against chemical or aqueous attacks and increase mechanical strength and scratch-resistance of the final product.
Ceramic glazes are used in tile production at 75 to 80%, instead of 10-15% for sanitary ware or 5-10% for tableware. Tiles are the most crucial glazed product in terms of boron use. Some borate is used in tableware glazes, including china, porcelain, and stoneware. Boron is not permitted in glazes for porcelain sanitary ware and vitreous china.
Borates can also be incorporated into frits to make them insoluble. The resultant material is mixed with water and finely ground to form a suspension that can then be applied to the substrate. The substrate is then dried and fired to fuse the enamel or glaze onto the surface.
Borates for Smooth Production
Borates are used in ceramics in enamels and glazes not just for the appearance and protection of the finished product but for efficient production. Borates inhibit the formation of glass in the initial stages of melting. Borates are a base for the dissolution of colouring oxides.
Borates help reduce firing times, glass viscosity, and surface tension. This allows the glaze/enamel to mature quickly and form a smooth, even surface. Borates also reduce the thermal expansion coefficient of glazes.
Types of Borates Used in Glazes and Enamels
Colemanite and ulexite, borax pentahydrate and decahydrate, boric acid, anhydrous borax are all examples of borates used in glazes and enamels.
Many factors influence the type of borate product used in ceramic/enamel glazes. The final ceramic product’s processing conditions, the composition of its final glaze, its requirements of secondary oxides like sodium and calcium, and the availability and cost of borates, and other raw materials, all play a role in determining which type of borate is used.
Although lower-grade colemanite is acceptable for some ceramic frits, iron levels must be controlled due to its colouring effect.
Anhydrous borax (anhydrous salt tetraborate) eliminates the need for crystallization but is often more expensive than other products. Borax pentahydrate may be the most commonly used refined borate on cost grounds.
Formulations that do not require sodium use hydroboracite, boric oxide, and boric acid. Boric oxide is used in glazes and enamels to reduce melting temperatures and improve glaze in ceramics. The enamel or glaze that results is beautiful, durable, and lustrous.
Standard Production Processes
Ceramic Glaze Production
Ceramic glazes are thin glassy coatings made from frits, coloring, or other oxides and processing aids. They can be formulated for specific purposes. Many glaze ingredients, such as boron, are insoluble in water. They can be applied to clay bodies wet and would absorb the contents. Glaze ingredients are fused into silica to create an insoluble frit and applied to the substrate before firing.
Glazes can be described using maturing or firing temperatures. When the glaze melts and flows smoothly across the article’s surface, and any defects like bubbles or pinholes disappear, it is called growing temperature.
Ceramic frits can be made by melting a mixture of crystalline materials at temperatures up to 1,500°C. The fundamental constituent of frits is usually silica (glass former), along with other elements that act as fluxes (such alkalis, alkaline earth, boron, and zinc), opacifiers, including zirconium or titanium, and colorants (iron chromium cobalt and manganese, for example). Depending on the product and firing temperature, there are many frits.
Formulation of Glazes Using New Boron Raw Materials
In 2019, RTM and Instituto de Tecnologia Ceramica in Castellon, Spain, developed a new borate material that allowed glaze compositions to be formulated using various materials without traditional frits. E4972 is a calcined borate that contains silica, SiO2, alumina, Al2O3, boron oxide, CaO, and sodium oxide. The boron dioxide content in the borate is between 10-11% by weight. The raw materials are calcined at temperatures much lower than those used for traditional ceramic frit production. This product is very amorphous and has low insolubility. It also has quartz as the main crystalline phase. RTM ran a pilot plant with a capacity of 7,000 tonnes per annum in western Europe using raw borate materials from its Californian operation and local raw materials. The first market was for matte glazes or semi-matte glazes to high-temperature porcelain tiles.
The new fritless glaze compositions were compared to traditional ones in their fired properties. It has now been confirmed that these new glazes have good chemical and mechanical properties and aesthetic characteristics.
Ceramic Tiles Production
Tiles can be fired once (monocottura) or less commonly twice (bicottura). About 90% of tile is made by pressing a spray-dried granulate into dies. After a switch to single firing, ceramic tiles are more commonly caused by one firing. This is to save energy and labor costs.
Borates are added to ceramic tiles to improve strength and decrease energy consumption during production. A small amount of boric acid can be added to ceramic tile bodies to promote the formation of a transparent phase with low viscosity. Borates can increase the dry mechanical strength by approximately 40%.
As firing times and temperatures have changed, so has the type of borate used. Double firing is necessary for sodium oxide, so sodium borates were used. Single firing is not recommended for wall tiles because of the high sodium oxide content. Therefore, frits are usually made with a non-sodium borate. Low viscosity frits are still made from sodium borates and used to enamel metals (mainly cast iron, steel, and aluminum).
Tableware Glaze Production
Many tableware glazes contain boron – boric acid. Options for tableware bodies, glaze types, and decorations can be made of stoneware, earthenware, porcelain, or bone china. In practice, most tableware glazes are made from silica, and some contain boron in boric acids. Tableware glazes have a high ability to crystallize partially and high mechanical strength. They also resist acids and alkalis.
Glazes can be single or double fired and are typically applied by spraying. Most tableware is fired twice. The temperature is low enough to prevent any uncontrolled deformation but high enough to fuse the glaze.
Porcelain Enamel Production
Porcelain enamels can be applied to various metal products to improve their appearance and provide corrosion resistance. Porcelain enamel is most prevalent in domestic appliances. Enamel can also be applied to cast iron and sheet-steel baths, sanitaryware, and cooking utensils, as well as chemical plants, hot pots, silos, and architectural panels.
Ceramic frits are not the same as porcelain enamel frits. Ceramic bodies are usually fired at more than 1,100°C and have a low thermal extension coefficient whereas enamel frits are fired at 800°C. To make them less viscous, higher amounts of boron are used in enamel frits.
Enamelled steel is the primary substrate for enamel frits. It can be fired at 800°C and has twice the thermal expansion coefficient of ceramic bodies. Enamelled steel, the primary substrate for enamel frits, has a lower viscosity than ceramic frits. It also has a higher thermal expansion. This is possible by using more sodium and boron – sodium borates – than in ceramic frits.
Porcelain enamels are usually made as a first coat and then a second coat. The ground coat is designed to form a strong bond with the metal substrate. This coating provides a decorative finish, chemical resistance, and opacity.