An Introduction To Boron Carbide
Boron Carbide crystal formation is formed as linear rods consisting of three carbon atoms and twelve boron atoms arranged in a dodecahedral pattern. The material has a chemical formula of “B4C.” Its hardness (Mohs scale 9.3) makes it suitable for use as an abrasive. Various applications such as cutting tools also benefit from its high density. It is even considered a rocket fuel.
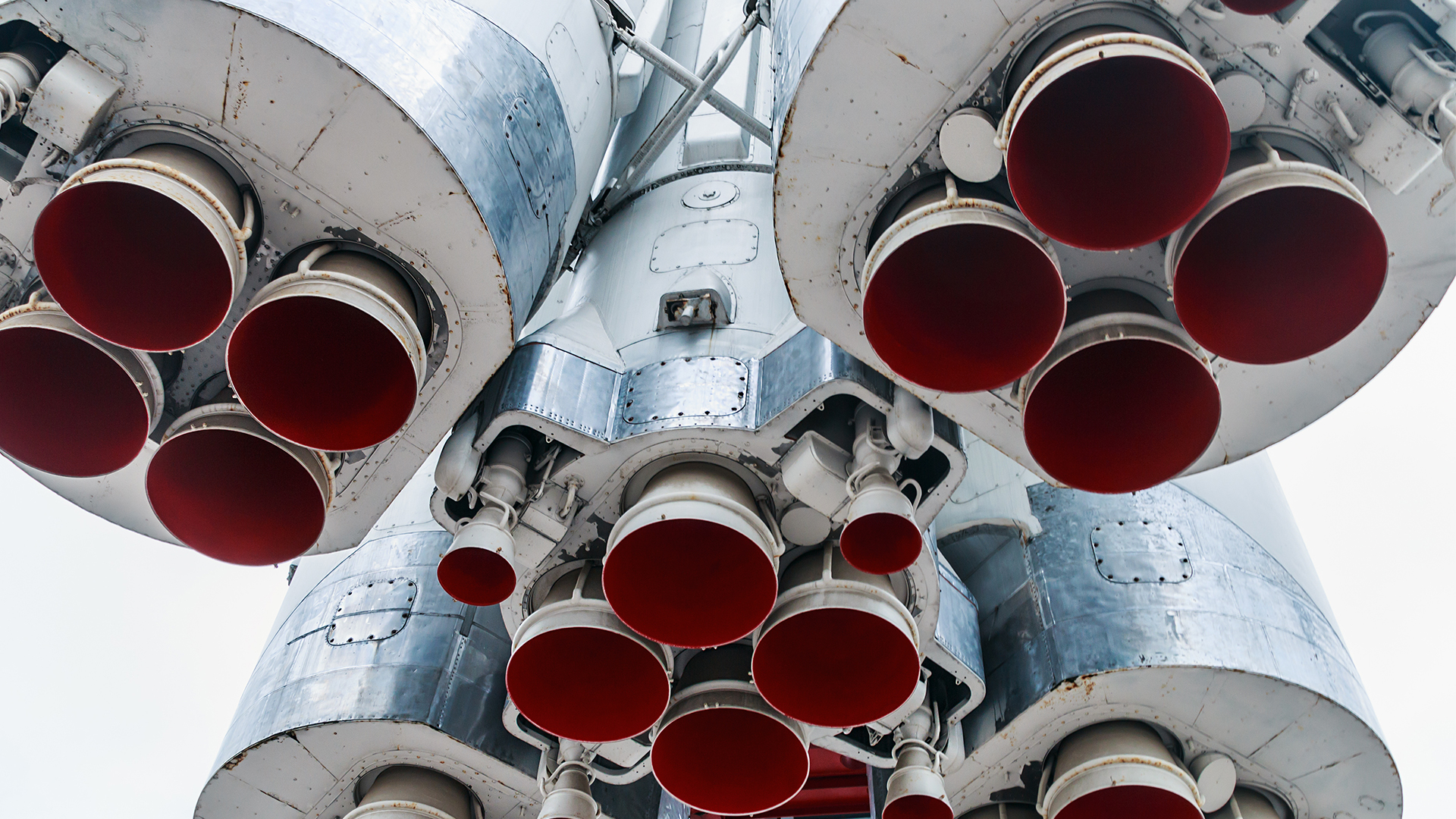
Boron Carbide
Boron Carbide Properties
Boron carbide exhibits the following properties:
High hardness; Low density; High melting point; high elasticity; chemical inertness; high neutron absorption cross-section; excellent thermoelectric properties.
The crystal structure of boron carbide is highly complex. A layer of multiple atoms composes the structure of all borides. The bandgap energy is about 2.09 eV, so the c-axis runs parallel to the surface. Mid-bandgap states complicate photoluminescence spectra in the crystalline structure.
Boron carbide powder has a density of 2.5 g/cc, 99.4 percent of its theoretical density. It has an average hardness of about three thousand KHN. However, the literature indicates that the optimum hardness ranges from 2,800 to 3,300 KHN.
It should be handled with care, as it is highly susceptible to thermal shocks because of its crystalline structure. Even though its chemical structure does not easily change, it does not break in contact with metal. Temperatures as high as 500°F are not a problem. Because of this, the metals in it can be cut easily by knives. A sharp blade may not perform as well due to the same reason.
Boron Carbide has a melting and boiling point of 2763 degrees Celsius. Consequently, the material is suitable for a wide range of temperatures. Its density is estimated to be 2.52 grams per cubic centimeter.
Production Methods
Boron carbide is produced as large ingots by mixing petroleum coke with boron oxide at high temperatures – 2000 degrees centigrade -. Carbon is reduced with boron anhydride in two steps using the following process:
B₂O₃ + 3CO = 2B +3CO₂
4B + C = B₄C
Above 1400°C, B2O3 reduction with carbon monoxide becomes thermodynamically feasible. The reduction temperature needs to be maintained beyond 2000°C to achieve a faster reduction rate and the production of boron carbide during the second stage.
In a resistance or electric arc furnace, boric anhydride (B2O3) is carbothermically reduced at temperatures exceeding 2000°C to produce boron carbide. Arc furnace products contain about 70-75% boron, along with a high percentage of free carbon. In contrast, resistance furnaces have carbide with a boron content close to stoichiometric (78.9%).
Carbon /1,2 and boron anhydride can also be reduced by magnetic isothermic to form boron carbide. Due to the reduction process, a very fine amorphous powder is obtained.
The material is well suited to the fabrication of sintered products.
Manufacturing
Boron carbide can be machined as green, biscuit, or fully dense, depending on the machining process. The green or biscuit form allows for relatively easy machining into complex geometries. However, sintering is required to fully densify the material, which causes the Boron Carbide body to shrink by approximately 20%.
Due to this shrinkage, boron Carbide pre-sintering can’t be machined to very tight tolerances. Diamond tools should be used to machine/grind fully sintered material to achieve very tight tolerances.
The desired form is created by rubbing away the material with an exact diamond-coated tool/wheel. The material’s inherent hardness makes this a time-consuming and costly process.
Boron Carbide Applications
1. It is the material of choice for engineering applications, given its high melting point and thermal stability.
2. It is used in refractory applications. It is also used as an abrasive coating material because it resists abrasion.
3. In military applications, its hardness and low-density properties are utilized in ballistics and the development of lightweight armour ceramic composites.
4. Boron carbide is also used in the nuclear sector as it absorbs neutron radiation absorbent. Because it offers good neutron absorption properties in both thermal and epithermal energy ranges, it is widely used in the nuclear industry as a control and shielding material.
5. In addition, is also a suitable coating material for rocket nozzle throats because of its good adhesion properties and resistance to high temperatures and chemicals.