Boron Lubricants for Drilling
Boron lubricants are multifunctional additives used in oil and gas exploration, drilling, and production. In addition to controlling pH, viscosity, and corrosion, they are also used to provide lubrication and exert other physical and chemical effects. Borates may be used in drilling fluid formulations to achieve several of these effects.
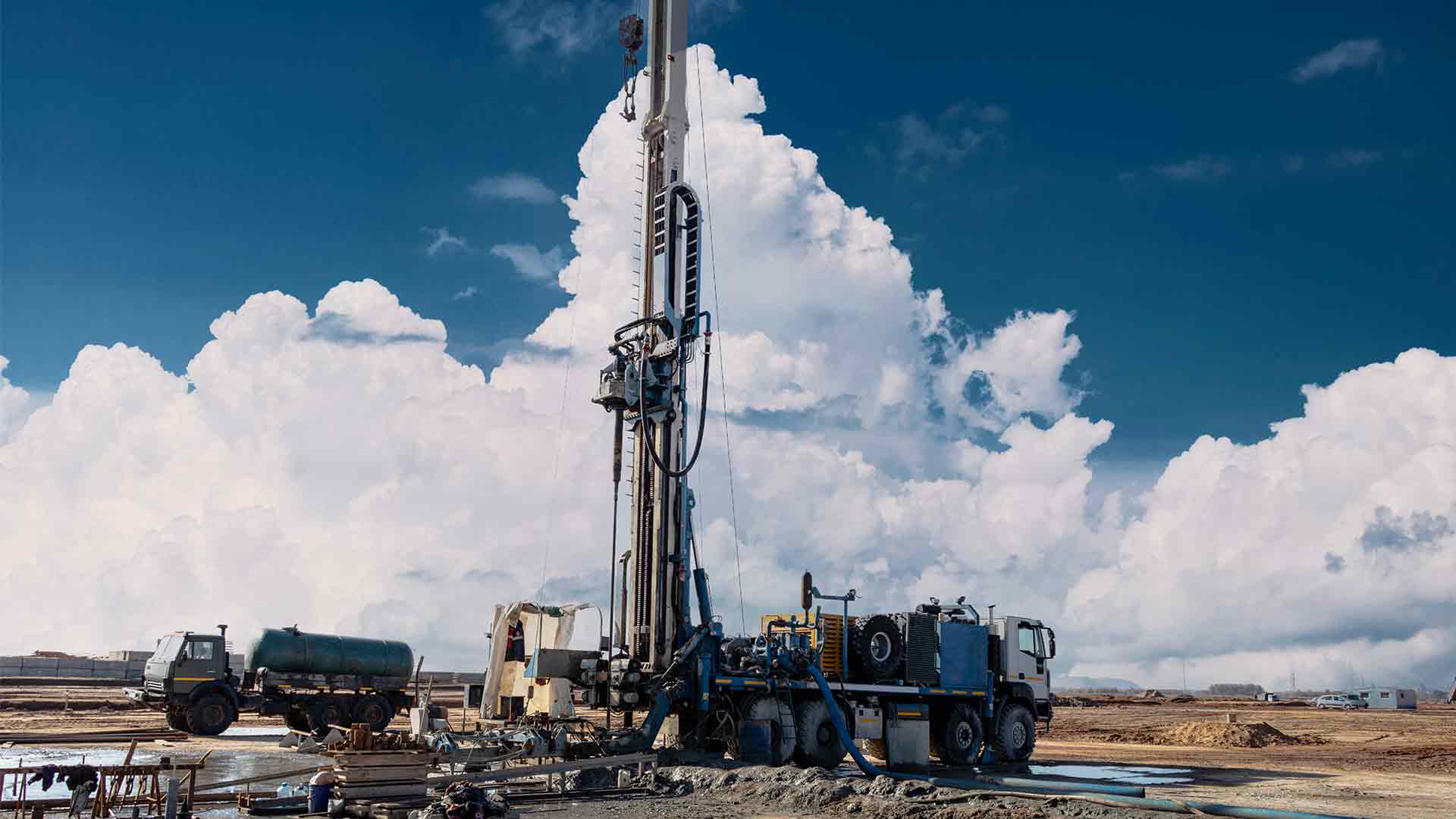
Boron Lubricants for Drilling
In oilfield drilling, sodium pentaborate provides lubrication and stabilization to wells and downhole drilling. This article will learn about the manufacture, application, and size of the sodium perborate market. Please continue reading to learn more about the Boron lubricant agent.
Sodium Pentaborate: What can it do?
The chemical formula of sodium perborate is NaH2BO4, Na2H4B2O8, or, more specifically, [Na+]2·[B2O4(OH)4]2−. There is a tendency to abbreviate its name as PBS (not confused with phosphate-buffered saline).
Compounds commonly exist in anhydrous form or hexahydrates (also called monohydrates or PBS-1 or tetrahydrates or PBS-4, based on the early assumption that NaBO3 was anhydrous). In terms of commercial importance, the monohydrate and tetrahydrate of these substances are white, odorless, water-soluble solids.
When sodium perborate is in contact with water, it undergoes hydrolysis, resulting in hydrogen peroxide and borate. The concentration of the solution increases, resulting in the appearance of other perborate species. This occurs in the presence of excess hydrogen.
Chemical Properties of Sodium Perborate
You can add sodium pentaborate to cement reinforcements to stabilize drilled wellbore walls. Borates adhere to the surface of cement grains, where they react with calcium ions to form calcium borate coatings that inhibit the grain’s hydration and the setting of the cement.
In nuclear power plants, sodium pentaborate can be used as a precursor to producing isotopically enriched materials with boron-10, necessary to ensure safety.
Formulation for industry
In contact with water, sodium perborate undergoes hydrolysis, forming hydrogen peroxide and borate.
The cyclic anion is hydrolyzed into two anions [B(OH)3(OOH)]-, which then enters into equilibrium with boric acid B(OH)3, hydrogen peroxide H2O2, the hydroperoxyl anion HOO−, and the tetrahydroxyborate anion [B(OH)4]−:
[(B(OH)₂OO)₂]²???? + 2H₂O ⇋ 2[B(OH)₃(OOH)]????
[B(OH)₃(OOH)]???? ⇋ B(OH)₃ + HOO????
B(OH)₃ + HOO???? + H₂O ⇋ [B(OH)₄]????
Other perborate species become more significant as the concentration of the solution increases. Excess H2O2 results in the formation of the anions [B(OH)2(OOH)2], [B(OH)(OOH)3], and eventually [B(OOH)4]. Due to its relatively low solubility, sodium perborate with dimeric anion crystallizes at high borate concentrations.
Monohydrates dissolve more readily than tetrahydrates and have higher heat stability; heating tetrahydrates create them.
A free-flowing white crystalline product, Sodium Pentaborate Technical Granular is manufactured in France by Borax Français S.A.S.
Source – www.borax.com
Application of sodium perborate for drilling downhole in oil fields
As a drilling fluid, sodium pentaborate can help improve the performance of some polymer-based fluid-loss additives and the lubricating and pH control characteristics of water-based liquids. It is effective in a wide range of drilling environments and helps decrease the potential for formation damage.
Sodium pentaborate is a compound that can help inhibit corrosion by protecting steel tubing, casing, and pipework from rust and decay. It can also reversibly cross-link viscosity-modifying polymers in water-based fluids, significantly when drilling deviated or horizontal wells. This helps maintain the fluid’s viscosity and prevents it from thinning out too much.
Explain the steps involved in making sodium pentaborate?
The process of manufacturing sodium perborate involves crystallizing a polymer derived from maleic anhydride, preferably one that contains plenty of free carboxylic groups, selected from the copolymers of maleic anhydride and an organic compound having an ethylene bond.
First, sodium metaborate is formed by combining borax and sodium hydroxide at a temperature of 90°C. The mixture is filtered when impure borax is used. In the second step, the reaction mixture is heated to 25 degrees Celsius, cooled to 15 degrees Celsius, and filtered off the precipitated sodium perborate hexahydrate. The reaction mixture may be stabilized with silicates or magnesium salts. A hot air dryer removes any residual moisture (between 3 and 10 percent). Following the second step, the mother liquor may be returned to the first step for further processing.
The end product contains ca. 10.1 to 10.4% of active oxygen (theoretically 10.38%). During the processing of the perborate, special steps are employed to adjust the bulk density to match that of the other components in the detergent (light perborate). There are no older manufacturing processes that use sodium peroxide or electrochemical methods. Hydrogen peroxide reacts with borax (Na2B4O7) to produce sodium perborate tetrahydrate.
Market size for Sodium Pentaborate
The most commercially important boron compound in terms of dollar sales is Na2B407.5H20. This pentahydrate is used in vast quantities to manufacture insulation fiberglass, Drilling lubricant, and sodium perborate bleach.
In 1986, Turkey produced nearly one million metric tons of mineral concentrate, whereas production of refined borate chemicals was 89,500 metric tons. Annual production capacities of chemicals at Eskiseher were pentahydrate borax, 160,000 t anhydrous borax, 60,000 t, and decahydrate borax, 17,000 t. Capacities at Bandermes were decahydrate borax, 55,000 t boric acid, 33,000 t, and sodium perborate, 64,000 t.